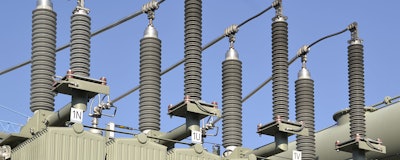
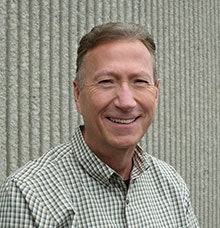
While working in the reliability field with a focus on electrical systems, I have discovered a number of myths that have led to a significant increase in transformer failures and an escalation of economic repercussions. See if you’ve fallen victim to any of these:
Myth No. 1 — Replacing an Older Transformer Eliminates The Risk Associated With A Failure And Potential Downtime
This sounds logical, but unfortunately it’s not true. Before computer modeling, transformer design was accomplished by slide rule. These transformers were heavier and overbuilt, and the industry came to rely on them.
Computer modeling emphasized reducing cost while still designing to the nameplate rating. The amount of copper, steel and insulation used in manufacturing was reduced. However, these new, lighter units created consequences for which there was no plan.
The quality of newer transformers has not been compromised, but the industry approach to maintenance has not been correspondingly altered. Consequently, traditional PdM or PM practices are effectively a recipe for failure.
Myth No. 2 — Transformers Have No Moving Parts, So There Is Little You Can Do Other Than Test The Oil For Gases.
Sampling transformer oil is the gold standard to understanding what is happening inside the unit. A battery of oil tests is necessary to ascertain the true overall condition of the transformer. Oil quality affects the condition of the paper, which in turn determines the life of the transformer
Conducting a dissolved gas analysis (DGA) is a sound practice, but much more is needed. A transformer with little or no fault gases may actually contain high moisture or high acid build up, conditions not detected with DGA alone.
It is widely accepted that hot oil cleaning of the transformer is one of the least expensive and most effective maintenance practices available. Yet decades of data document that a majority of transformer owners do not process their oil to clean both the oil and the solid insulation.
Our recent study of 1,534 decommissioned transformers provides the evidence in the following illustration.
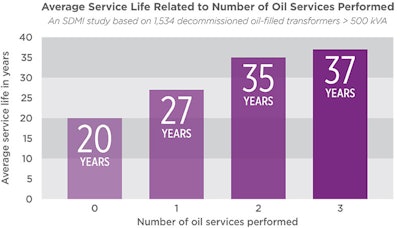
These findings should convince maintenance budget developers to use the diagnostics and recommendations from oil testing to employ good PdM principals. Yet this is seldom done until a transformer failure shuts down a plant for a long time period. Disaster has often become the wake-up call.
Myth No. 3 — Oil Processing Is Basically The Same From Vendor To Vendor, So Go With The Lowest Price
There are four considerations regarding effective oil processing:
Safety. Safety lapses always come with consequences. The amount, quality and timeliness of the training required of the crews, along with proper tools and equipment, are primary considerations.
Crew competence. The more experienced the crew, the better the outcome.
All equipment is not created equal. There are differences in quality, reliability and endurance of processing equipment. These differences can greatly affect the quality of the service performed.
Clean oil does not necessarily mean a clean, dry transformer. There is about 100 times more moisture in the paper insulation than in the oil. Drying the oil does not dry the paper. The same holds true for acids. The amount of heat and the number of passes impact the long-term success of the processing.
Myth No. 4 — Senior Management Understand The Risks Of Aging Transformers And Are Including That In Their Capital Planning
If only this were true. In one of our recent reliability studies, we reviewed all the critical transformers for a large metals-processing plant. The average unit age was more than 30 years, with some over 35 years. Their OEM-suggested life was about 20 years, confirmed also by a transformer insurance executive.
Eventually one of the older transformers failed, causing millions of dollars in lost production. At that point senior management made PdM a priority. These failures are being repeated in every major industry that relies on electrical power. The financial losses are staggering.
Myth No. 5 — We’ve Checked With Manufacturers, And The Lead Time For Replacing A Transformer Is Not A Problem
There is some truth here, but just enough to be dangerous. With worldwide competition, transformer supply should not be a problem. However, the more unique a transformer’s design, the more likely lead times will be extended.
For larger units, a major issue is transportation. Despite reduced transformer weights, road and bridge infrastructure can often impose staggering obstacles.
Regarding replacement, unit footprint is an important factor. It is also common to find cabling and construction requirements that considerably increase costs and extend replacement times.
Myth No. 6 — The Reliability Engineer Understands These Concerns And Has Everything Covered
Reliability engineering is a rapidly growing discipline requiring very rigorous study and training. It involves a higher level of reliability concerns than those typically represented by standard maintenance practices.
The diagnostic tools and techniques used in O&M — while similar — are different enough to require specialized training for electrical reliability. In addition, lifecycle planning for transformer assets must be approached differently than for many other assets. Unfortunately, all too often transformers fail to get the attention they truly deserve.
Myth No. 7 — Installing DGA Monitors On My Critical Units Will Reduce The Risk Of Transformer Failures.
There is just enough truth here to make it sound reasonable. Theoretically, as compared to periodic oil testing, a DGA monitor can potentially reduce the risk of a transformer failure by alerting you sooner to a developing problem, giving you more time to act to prevent a failure.
However, we have learned from an 18-month industry-wide study covering 95 percent of fault gas monitors that they tend to produce too many false alarms. The other challenge is the overwhelming amount of data that is generated. Therefore, from a practical viewpoint, these factors encourage the tendency to either ignore the alerts or distrust the data, which can lead to an adverse compromise of the production system.
Conclusion
In order to advance your reliability program, it is time to put these myths to rest. We cannot overestimate the value of having best practices in place for testing, maintenance and monitoring. Your production system and the stability of your company depend on it.
Alan Ross is the Vice President of Reliability at SDMyers LLC in Tallmadge, Ohio. He is responsible for developing and executing long-term reliability strategies and next-generation leadership for all operating units, both domestically and internationally. Alan often presents at industry conferences and has written two books: Unconditional Excellence and Beyond World Class. He completed his undergraduate work in Mechanical Engineering at Georgia Institute of Technology and an MBA in Marketing from Georgia State University, graduating Magna Cum Laude. Alan is a Certified Reliability Leader, SMRP designee to the DOE’s Strategic Transformer Reserve task force and member of the IEEE Reliability Society.