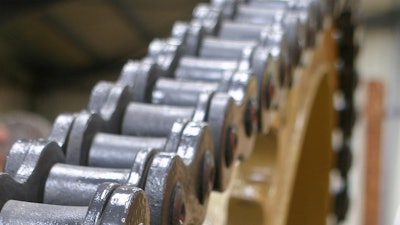
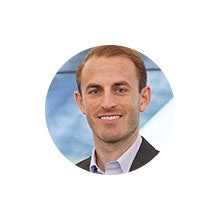
Proper lubrication through preventative, predictive maintenance will provide a range of benefits to ensure reliability of machinery parts and equipment. Among these advantages is the prevention and control of corrosion to help ensure surfaces are protected from caustic and harmful substances, including water and rust.
Corrosion is one of the most negative influences on equipment. It can be produced by moisture, certain substances and through oxidation. Insufficient corrosion control will lead to the degradation of the most important attributes of machinery, including the strength of its surfaces and overall appearance. Left unchecked, corrosion can create pitted, irregular surfaces and cause subsequent breakdown and downtime of equipment.
Practice Makes Perfect
Long- and short-term corrosion control can be achieved through a variety of tactics and methods, including using lubrication as a boundary to shield and protect the surface of machinery and preserve its integrity over time. The right oil, grease or aerosol will help mitigate oxidation and rust in many types of key equipment, including reducers, motors, compressors, bearings and hydraulic power units.
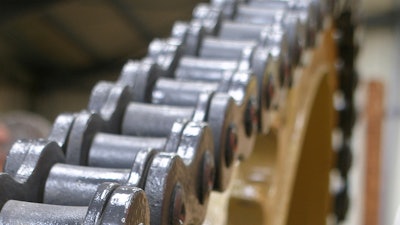
Inside The Facility — Chain
One of the most common pieces of equipment found in plants are chains for both drives and conveyors. They are susceptible to fatigue, overload, misalignment and premature stretching, but corrosion and contamination build-up is arguably the most serious problem. A chain will fail or perform improperly if excessive carbon and deposits are allowed to develop and build over time.
Lubricating chains properly means finding and pinpointing the correct lubricant for the application. From conveyors to bakery ovens, not all chains should be protected by lubrication in the same way. But, when lubrication is done properly, chain life can be increased exponentially.
For example, when lubricating roller chain on a conveyor, you would generally in most applications want to use a low to medium viscosity oil that has the ability to penetrate the pins and bushings from the inside. Depending upon your environment and temperature, your lubricant choice must be able to handle the specific conditions by maintaining a boundary film. This means your oil could be petroleum or even synthetic, based on the circumstances. If the roller chain is in a high washdown situation, an oil that can withstand excessive water over time is critical to the success of the operation.
Alternately, inside a bakery oven, the chain can be exposed to as much as 700 degrees Fahrenheit. Average petroleum-based mineral oils are not capable of handling this elevated level of heat. In many cases, a strong type of synthetic oil called an ester will help to protect, preserve and maintain a clean lubricated surface of the chain, negating the buildup of carbon and other contaminates. Ester-based synthetics are unique in their chemical composition and specially designed to provide stability and resist thinning at elevated temperatures.
Long-Term Prevention
Averting and preventing corrosion through lubrication is an important and critical part of a successful preventative maintenance program. It will lead to long-term equipment and machinery health, cost savings and decreased downtime. To achieve this in your facility, it is vital to adhere to OEM recommendations and consult a lubrication engineer or specialist to pinpoint the correct lubricant for the application. Not all lubricants are formulated the same way and they are designed to perform differently based on specific needs and applications. Successful corrosion control can be achieved by making the right decision with the proper lubricant.
Chris Kniestedt is a lubrication specialist for the San Francisco Division of Birmingham, AL-based Motion Industries, Inc.