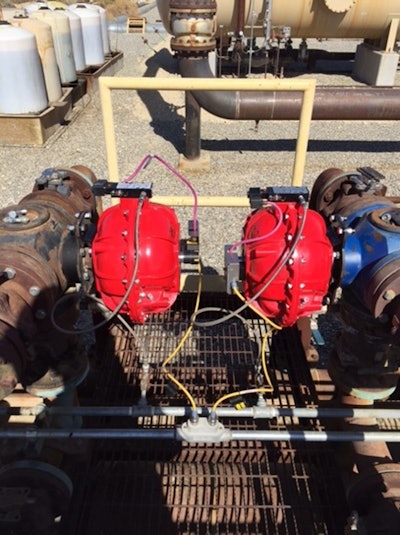
Pneumatic actuator designs have virtually remained unchanged for the better half of the past century. A valve actuator compresses an internal spring when the actuator moves the flow control element away from its starting position (open or closed) and then uses the energy stored in the spring to move the flow control element back toward its starting position. As the piston/rack drives a pinion, it also compresses a series of springs. Upon loss of compressed air, the springs return the piston to its selected fail position.
Unfortunately, spring return actuators are not cost effective, as actuators must be sized to overcome the spring tension and to the required torque of the valve and system. This requires the actuator to be oversized, which increases the cost of the actuator. With the addition of the spring assembly, costs can be anywhere from 30 to 80 percent higher than the standard double-acting actuator assembly. Springs are also subject to corrosion from atmospheric conditions and degradation from constant compression.
Many industry experts and end users are aware of an alternative to the use of springs to accomplish the fail-safe mode of operation. This is achieved with the use of external air reservoirs to store compressed air needed to supply the required force to fail the valve to the fail-safe position. Applications for such fail-safe setup can be observed in applications for actuating large emergency shutdown valves. Air reservoirs have traditionally been supplied as an added piece of equipment which requires custom brackets and mounting hardware. External reservoirs require ASME code certified tanks that are mounted to the actuator assembly. These reservoirs not only add to the size and cost of the system but also require a considerable amount of external tubing. These considerations add to the overall footprint which limits the usefulness and cost efficiencies.
Over time, durability, safety, efficiency and cost all become factors in which end users and industry experts must contend and compromise. This is becoming more evident in a global economy that thrives on efficiency and technology advances.
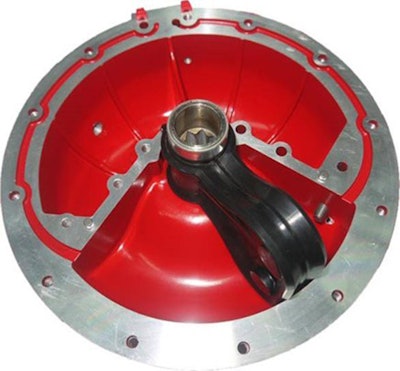
Today’s Actuators
Today, new generation actuators need a cost effective and space conservative design to supply enough pressurized operating medium to perform the fail-safe action, without the use of springs or external reservoirs. The ultimate design would be to integrate the reservoir into the pneumatic actuator housing to provide the necessary stored energy. With the proper pilot assembly, the reservoir would be constantly pressurized and available to perform the fail-safe operation during a power failure or a catastrophic air failure. These features have been designed, built and field tested as seen below. This reservoir is internal to the actuator and is sized to allow for the fail-safe operation. With the reservoir internal to the actuator, springs are not required, therefore reducing the size, weight and footprint of the actuator. The fail-safe operation is accomplished by utilizing a properly ported solenoid valve or pilot assembly. Both of these will pressurize the reservoir during normal operation with full operating pressure. At the loss of power or catastrophic air loss, enough air is maintained in the reservoir to fail the valve in the pre-selected fail position.
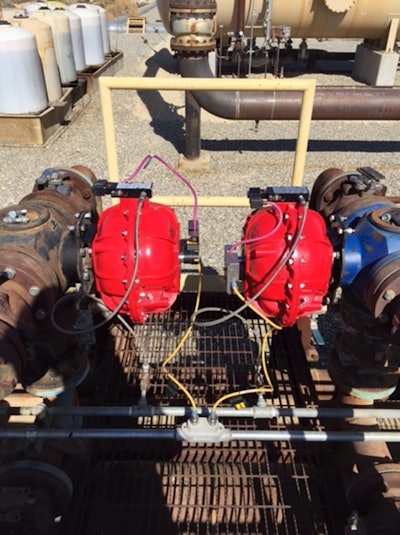
Some of the benefits of utilizing a pneumatic actuator without springs are:
- Actuator size reduced as a result of not having to overcome the spring torque
- Reduced actuator weight by virtue of smaller actuator and lack of a required spring pack
- No spring corrosion or degradation over time which leads to longer actuator durability.
- Safer, as there is no need to replace or adjust springs.
- Overall dimensions of actuator reduced due to reduced size and elimination of springs
- Reduced inventory and operating costs as the same actuator and solenoid package can be used for double-acting or fail-safe.
- Reduced operating costs by utilizing smaller actuator due to not having to overcome spring torque.
- Reduced corrosion as no environmental air is ever introduced into actuator.
- NEMA 4, explosion proof and low voltage version available for all pneumatic fail-safe actuator design, whereas it is significantly more cost prohibitive for electrical actuators. Emergency shutdown valves are primarily associated with the petroleum and petro-chemical industries although other industries may also require this type of protection system. These two industries, as well as others, will require explosion proof actuator assemblies.
- Reduced maintenance costs.
Already, the biggest beneficiaries to this platform are vane actuators, which inherently have an inability of incorporating springs internal to the actuator body. Whereas alternatives such as rack & pinion, cylinder, diaphragm or scotch yoke designs can install springs internal to the actuator body. Traditionally, vane actuators are an excellent choice for durability, safety and efficiency as a result of vane actuators creating pure rotary force, as opposed to rack & pinions which convert linear force generated by a piston transferred into rotary torque through the small radius of the shaft. However, when the requirement for springs come into play, traditional vane actuators are not cost competitive to its alternatives; with this new platform, vane actuators can now be offered at costs less than the traditional spring return actuator.
The introduction of the pneumatic fail-safe actuator without the use of springs, external reservoirs and an emergency backup operating medium has significantly changed the pneumatic fail-safe industry. This technology is in line with the global trend towards advancement in durability, safety, efficiency and cost of pneumatic actuators
Prior to founding Easytork, George Wang was part of a group that founded Taiwan Ball Valve, one of the larger ball valve manufacturers in Taiwan that was eventually sold to Tyco in 2002. Along with his original group, they created and patented the design for Easytork. Jack Dovenbarger is a sales manager for Easytork. He has held senior management positions with several nationally known valve and actuator manufacturers, with positions ranging from sales and national sales manager to vice president of product development.
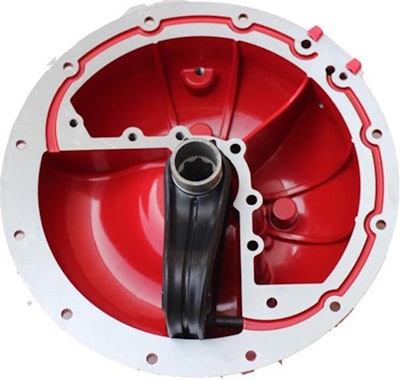