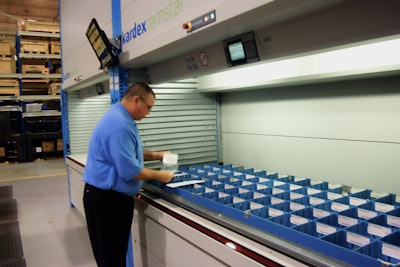
Manufacturers around the globe depend on Okuma, a world leader in CNC (computer numeric control) machine tools and controls. Okuma delivers complete package solutions that help manufacturers gain competitive advantages through the open possibilities of Okuma machine tools. With the largest independently owned distributor network in the industry, Okuma provides high performance solutions without compromise.
Okumaβs extensive parts program provides customers speedy access to a large global parts inventory, maintaining the high performance that is expected of an Okuma machine tool. Further, their βzero obsolescenceβ policy means they provide parts for every Okuma CNC machine ever made. The extensive global inventory enables Okuma to achieve a service parts fill rate greater than 95 percent, meaning itβs likely the part the customer needs is on hand and ready for delivery.
With over $38 million in parts inventory, the US-based aftermarket parts facility in Charlotte, NC recently integrated three Shuttle XP Vertical Lift Modules from Kardex Remstar to provide even faster and more effective parts replacement service to customers. With the mechanical repair area in need of expansion, Okuma considered two options - a building expansion or using vertical storage to decrease the warehouse footprint. βAs we researched, we found automated vertical storage would provide improved worker ergonomics and productivity, tighter inventory control and the space savings we were looking for β it was the best choice,β Mike Vassil, Senior Manager Service Parts.
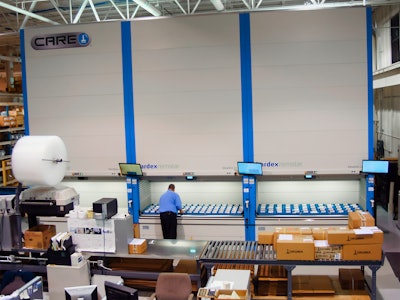
Expanding Vertically
A 1,200 square foot mezzanine parts storage area was replaced with three 18-foot tall Shuttle VLMs occupying only 400 square feet β a 66 percent floor space savings. βThe renovation gives us better control of inventory accuracy and expedited shipping of parts,β said Vassil, βBy streamlining storage and maximizing space in our warehouse, we were able to expand the mechanical repair area, increasing mechanical exchange capabilities to service more spindle and cam box repairs.β
Faster & Easier Parts Access
With an average worker tenure of 20 plus years, Okuma has a knowledgeable and experienced work force. The VLMs deliver all parts to the worker, eliminating walking, searching and stair climbing associated with the previous mezzanine shelving. Further, parts are presented at an ergonomic access opening eliminating bending, stooping, reaching to retrieve parts. βNow workers are standing within 10 feet of every part,β said Vassil, βRemoving excessive walking, bending and reaching from the parts fulfillment process has increased productivity and made the job easier for our warehouse staff - allowing us to easily maintain our 7pm order cutoff time,β said Vassil.
Tighter Inventory Control
The VLMs are integrated with Power Pick Global inventory management software providing tighter control and more accurate inventory counts. Warehouse employees must scan their badge before the machine will store or retrieve a part. βEvery part is tracked from when and who receives it, where itβs stored within the unit and when and who retrieves it; ensuring all parts are accounted for,β said Vassil. Transaction logs and inventory reports are available to managers on demand.
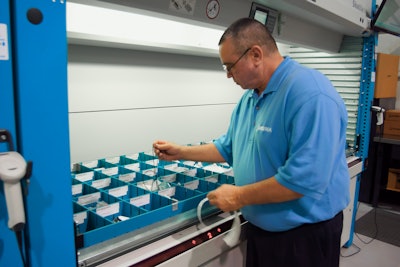
Order Fulfillment
When parts fulfillment is needed, the ERP system generates a series of labels for each order that print in the warehouse. Each label indicates V1, V2 or V3 and the warehouse worker takes the labels to the correct VLM where the parts are stored. When at the VLM, the worker must scan an employee badge to gain access. The worker then scans the bar code on each label within the order, and uses a touch screen monitor mounted at each VLM to begin the picking process.
The VLM moves to retrieve the part required and delivers it to the access opening. Equipped with pick to light technology, the TIC (transaction information center) uses a light bar to direct the worker to the exact location of the pick and indicates the part number and quantity to be picked. Once picked, the worker labels the part and pushes the confirmation button and the VLM moves to retrieve the next part required. The worker moves from V1 to V2 to V3 collecting all of the parts for the order on a cart. An auto log out feature within the software automatically logs the worker out for security.
Once all of the parts required for the order are collected, the worker uses the pack counter located just next to the VLMs to prepare the order for shipment. There is a small portion of larger bulk items stored on adjacent shelving. When required for an order, these parts are retrieved and matched with the VLM parts to complete the order.
Replenishment
Replenishment is easily handled seamlessly between Power Pick Global and the ERP system. Minimum quantity levels are set and Power Pick Global automatically generates reorder reports that are sent to procurement. Parts are received and replenished by the warehouse in the morning when order volume is lower.
Transitioning To Automation
The Okuma warehouse renovation was handled by Alternative Handling Technologies (AHT), one of the nationβs largest material handling distributors. They provided the system concept, solution, installation and service. βRenovating a parts operation can be risky, but AHT made it a smooth transition for us with their creative solution approach and excellent communication throughout the installation process,β said Vassil.
Kardex Remstar, LLC, a company of the Kardex Group is a provider of automated storage and retrieval systems for manufacturing, distribution, warehousing, offices and institutions. For information about its dynamic storage solutions, call 800-639-5805 or visit www.kardexremstar.com.