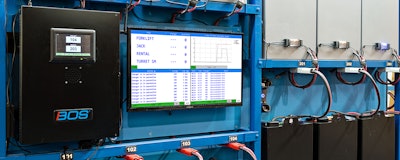
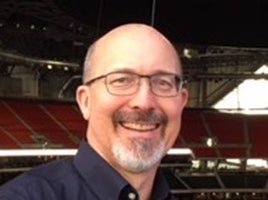
As warehouse and distribution center (DC) managers continually seek to wring every ounce of efficiency and savings possible from their facilities, they finally are turning their attention to “the last frontier” of improved warehouse efficiency and productivity: the forklift battery room. Despite the availability of a number of time- and cost-saving tools to improve forklift battery performance and warehouse productivity, some warehouses still operate their battery rooms as they did 10 or more years ago. Some of today’s battery maintenance technologies enable battery rooms to operate with less equipment, improve operator productivity, increase worker safety and save money.
Battery Rotation
The No. 1 cause of reduced battery run time and battery life is improper battery rotation. This occurs when forklift operators make their own battery selections without proper direction as to the “correct” battery to take. Left to their own devices, operators will take the closest battery (in order to make the quickest change) or the newest battery (in hopes of getting the longest run-time). The “correct” battery – the battery that has had the longest cool down time since charging – may be in the back of the battery room.
The consequences of improper battery selection are costly. Site tests have shown that when battery selection is left to an operator, 30 percent of the batteries will be underutilized and 20 percent will be overused. The result: uneven battery usage, premature battery failure and lost productivity.
When proper battery rotation practices are implemented the results are dramatic. In a study of one company’s good battery rotation practices, the average battery run time increased from 6 hours 30 minutes to 6 hours 57 minutes—nearly half an hour.
Battery Management— The Key To Proper Rotation
Battery management systems are the single most effective tool for ensuring proper battery rotation. Some of these systems monitor all batteries in a pool and eliminate operator judgment in battery selection by determining which battery has had the longest cooling time since charging. Once charged, each battery is placed in queue. A display then tells the operator which battery to take. An audible alarm alerts the operator when the wrong battery is taken. And, a battery room manager can use an on-site computer to continuously monitor battery selection activities.
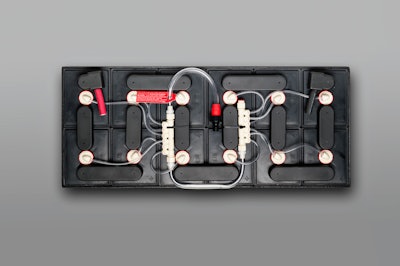
Rightsizing
Rightsizing a battery room also offers significant potential cost savings by properly matching the size of the battery fleet to the operational needs of the forklift fleet. When a battery fleet contains too few batteries, battery assets are being over-utilized, reducing battery run time and battery life. When there are too many batteries in a fleet, unused assets are being wasted.
The most efficient method for rightsizing a battery fleet requires ongoing operations feedback and measurement from a battery management system. Key areas to measure include battery availability at any given time; the length of cool down time; and battery cycles per week.
Battery Watering—Determining When to Water Batteries
Watering industrial batteries has been called “a simple job done poorly.” In most warehouses, batteries are watered on a set schedule—typically every week. This can be a real time waster, as many of the batteries that are checked don’t need watering – and many that are checked needed watering far earlier, and costly, permanent damage may already have been done to the battery.
The fastest way to determine when batteries need watering is with battery watering monitors, which attach to the top of each battery. Monitors allow watering on a labor-saving, “as-needed” basis instead of a hit-or-miss schedule. Battery watering monitors not only save money and improve productivity, but enhance warehouse safety by reducing employees’ exposure to acid.
Watering batteries quickly and precisely
The precise watering of batteries is critical to their long run time and long life. Over-watering a battery can cause boil overs, creating a hazardous condition. It also decreases the battery’s useful life because sulfates are washed out of the battery during a boil over, and sulfates are needed to maintain capacity. Over time, boil overs can decrease the life of a battery by six months or more.
Under-watering can happen when batteries aren’t watered on schedule or when they are manually watered and the operator accidentally skips a cell. When a cell is skipped in a typical watering regimen, it might not get the water it needs for another week. When parts of the battery’s positive and negative plates get dry, battery capacity is decreased. And even when water is re-introduced to the dry cell it will not return to its previous performance. In the worst case, a damaged cell would need to be replaced entirely.
The most common factor contributing to over- and under-watering is the hand-watering of batteries. It is estimated that more than 50 percent of industrial batteries in North America are filled by hand, despite the fact that more efficient means have been available for years. For example, single-point watering systems incorporate injectors or valves that are inserted into each battery cell. The injectors or valves are connected by plastic tubing, forming a single, continuous flow path on top of the battery. The operator attaches a water hose, opens a valve and waters a single battery in about 15 seconds—a fraction of the time it takes to water a battery by hand.
The systems save money in two ways. First, they cut labor costs, often paying for themselves within their first year of operation. Second, they extend the life of each battery they are installed on due to improved quality of watering. Single-point systems also improve safety and environmental cleanliness. They automatically fill each cell to the correct level, so there is no electrolyte overflow during charge.
Eye-Popping Savings
Personnel at one large DC found that poor battery maintenance was causing shorter battery life and run times, underutilized personnel and an excess number of batteries.
The DC had 194 36-volt batteries, 544 24-volt batteries and 229 chargers. Personnel installed a battery management system in the battery room and single-point battery watering systems and battery watering monitors on the 36 volt batteries. Guided by data from the battery management system, the DC applied corrective strategies and achieved the following results:
- The time spent changing batteries was reduced from seven to five minutes.
- The number of battery changes was reduced by more than 30,000 per year at a savings of $194,728 (based upon an estimated hourly wage for drivers and battery room attendants).
- Pallet jack and forklift batteries’ cool down time increased an average of 8.9 hours. Longer cool down times after charging enable batteries to last longer and achieve longer run times.
- The DC reduced the number of pallet jack batteries from 544 in 2014 to 380 in 2016 – and reduced the number of forklift batteries from 194 to 153, saving $650,000 on batteries not purchased over two years. The DC sold its excess batteries for a one-time scrap payment of $81,074.
- The DC increased the life of its batteries by four to five years or more while reducing the number of batteries required. In 2016, the DC spent $137,883 on new batteries — 35 percent less than in 2014.
- The DC’s net cost for management equipment was $58,000, which included the battery management system ($100,000) and the battery watering and monitoring systems ($39,000) minus the money earned from the scrapped batteries ($81,000).
- The DC’s net yearly savings totaled $237,600, which included labor savings ($195,000) and equipment savings ($42,600).
Charles R. Snyder is Vice President of Sales and Marketing and Philadelphia Scientific.