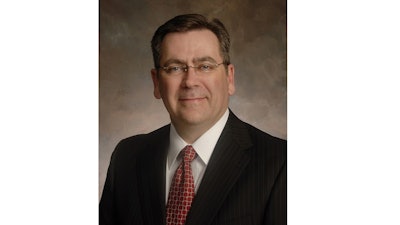
Looking around most factories these days, you will see more and more automation throughout the plant. Automation on the plant floor is and will continue to be necessary for a number of reasons.
First and foremost, manufacturers need to improve productivity and throughput to remain competitive in the global markets they serve. Automated equipment provides the opportunity to do things faster and safer in many applications. I've talked with many customers that have commented after installing an automated production line that the "robots don't get sick, don't take breaks and don't get hurt!" The result is improved productivity based on the speed of the equipment and reduced operational expense from fewer accidents and safety issues. Payback on automation equipment is usually within 24 months when considering productivity and safety gains.
Second is the reality that all manufacturers are being faced with today, which is the lack of skilled labor in the workforce today and coming into the workforce in the future. Without workers, alternative methods of getting the job done have to be employed. Enter automation and robotics. New developments of collaborative robotics now provide opportunities for employees to work side by-side with robotic equipment that is safe to interact with and does not have to be housed inside a cage or protective structure.
Motion Industries' automation specialists work with many customers looking to improve safety while also increasing productivity by identifying applications on the plant floor that are perfect candidates for automation.
Randy Breaux is the CEO of Motion.