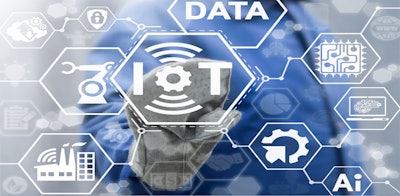
Guide to IoT’s Manufacturing
Maintenance Transformation
2
When you hear about the Internet of Things (IoT),
the first thing that comes to mind is probably
some application of technology. You may think of
smart home devices, such as digital thermostats
or Amazon’s Echo, or even more advanced
technology in the form of machine learning and
artificial intelligence could come to mind. But
what exactly is IoT, and why are we talking about
how it relates to manufacturing? IoT’s use in
manufacturing is a lot simpler than you think, and
it’s all connected with data.
What is the “Internet of Things”?
The Internet of Things is a popular buzz phrase, but
what it really refers to is devices that are connected
to each other, often via the internet, that work
together or communicate in some way. The way
that IoT is being leveraged today is related to the
increasing availability of devices with internet
access and sensors. More and more people are
switching to smartphones, the cost of internet
broadband access is going down (and it’s more
widely offered than ever in restaurants, stores and
even public spaces), and companies are starting to
see how they can leverage all of this data floating
around in devices.
One example, as we listed above, are digital
thermostats that can be controlled from the device
itself or via your smartphone. It can also refer
to something as simple as a desktop computer
sending a document to a fax machine or printer, or
even just connecting your laptop to your home Wi-
Fi. In short: IoT is all about being connected and
getting information without human intervention.
You can start to see how manufacturing could
leverage IoT. Having a computerized maintenance
management system (CMMS) readily provides
you with data and insights into your operations,
and you already have a large amount of historical
information on equipment. Taking that data and
using it – without any manual input from your
employees – is what elevates your maintenance
from reactive to proactive and lets you plan for the
future, or Industry 4.0.
Smart Manufacturing,
or Industry 4.0
In Industry 4.0, IoT takes manufacturing to the next
level. The phrase refers to the Fourth Industrial
Revolution. The First Industrial Revolution occurred
when steam and the first machines took over the
work that had been done entirely by hand, the
Second was electricity and mass production, and
the Third was the beginning of automation when
computers and robots were introduced.1
Industry 4.0 is all about interconnectivity. As
Industry Week describes it, it focuses on “creating
an environment where all available information
– from within the plant floor and from along the
supply chain – is captured in real-time, made visible
and turned into actionable insights.”2
Machines are the lifeblood of manufacturers,
and maximizing OEE is one of the most valuable
objectives. Therefore, Industry 4.0 has a huge
emphasis on leveraging new technologies to
ensure that your machines are up and running
when you need them. Smart manufacturing,
Industry 4.0, the Industrial Internet of Things (IIoT)
– there are many names that refer to it, and when it
comes to maintenance it all means that you have
an automated, continuous supply of data that will
help you reduce downtime and ensure that your
equipment is ready when you need it.
Leveraging all this data and technology available to
them in maintenance enables a way to plan into the
future. We’ve talked about preventive maintenance
(PM) and its value for manufacturers. It’s almost
impossible to plan ahead if you’re stuck in a state
of reactive maintenance and waiting to run your
equipment to failure. With a CMMS, you can begin
to plan out work orders in advance and reduce
the number of problem requests that your team
receives.
While you should still perform PM, predictive
maintenance (PdM) takes your maintenance
routine one step further by not only keeping
your work proactive but also anticipating when
something will fail or break.
200019501900185018001750
FIRST (1784)
Mechanical
production, railroads
and steam power
THE FOUR INDUSTRIAL REVOLUTIONS
SECOND (1870)
Mass production, electrical
power and the advent of
the assembly line
THIRD (1969)
Automated production,
electronics and
computers
FOURTH (NOW)
Artificial intelligence,
big data, robotics and
more to come
3
The Future of Maintenance: PdM
According to a recent survey by Plant Services, 74.5
percent of manufacturing professionals stated that
they use PdM for condition monitoring.3 Instead
of only doing preventive work to prevent future
failure, PdM analyzes historical data and real-
time information so you capture a more detailed
picture of your assets’ working lives. To capture
this information, PdM works hand in hand with
condition monitoring.
This process minimizes downtime as you can
capture information while equipment is running.
Some common types of condition monitoring
includes vibration analysis, oil analysis, acoustic
analysis and more. With IIoT, you can automate
these condition monitoring processes and many
others with the use of sensors and machine-to-
machine communication.
Machine-to-Machine
Communication
Machine-to-machine (M2M) communication is
essentially any automated process that allows two
machines to exchange data or other information
without human intervention. M2M communication
relies on sensors for condition monitoring so
that it can predict when a failure or problem may
occur. Sensors are installed directly into machinery
and can measure a variety of factors, from
temperature to vibrations.
Wireless sensors are widely available, making it
easy to take advantage of the automated PdM
process. Whether you choose to use a wireless,
RFID or Ethernet-connected sensor, as long as it’s
able to access the internet, it can send and receive
data. This automated monitoring, also called “lights
out manufacturing,” acts as your eyes and ears
when no one else is there in two ways:
1. The system catches early warning signs of a
failure and notifies a technician, even if it’s after
hours
2. The system can predict when something will fail
in the future, how much it will cost and when it
will happen so you can prepare ahead of time
While humans are still an important part of
making this process work, there’s little need for
extensive oversight because the machines do all
the monitoring for you. In fact, you’re not required
to step in until a sensor recognizes a problem
and sends a notification back to your monitoring
system thanks to automated condition monitoring.
But as with any kind of data monitoring and
collection, it’s not enough to simply have the
information if you don’t utilize it to improve your
operations and develop insights. IoT sensors extend
beyond asset condition monitoring when linked to a
well-designed CMMS to fuel your PdM plan.
4
of manufacturers use
predictive maintenance3
M2M Communication
NETWORK
CMMS
TECHNICIANS
ASSET ASSET ASSET
SENSOR SENSOR SENSOR
5
Predictive Maintenance and
Your CMMS
Whether your equipment requires maintenance
based on run hours, parts produced, vibration
analysis thresholds or temperature ranges, a
CMMS, like Dude Solutions’ Asset EssentialsTM, is
invaluable to making it all work. PdM with a CMMS
helps you in four major ways:
1 . A D V A N C E D
W O R K F L O W S
The right solution helps you configure your CMMS’ advanced workflows to trigger email
notifications, work orders or other actions to tackle any problems that are detected in real
time. This means that you don’t have to wait until the next day to discover that an error
occurred; a technician can receive the message and address it immediately, ensuring your
machines have maximum OEE.
2 . A U T O M A T E D ,
D E T A I L E D
R E P O R T I N G
Automated CMMS reporting may be scheduled to be delivered to key employees to
understand the relationship between maintenance activity and current and historical
condition data. You’ll also be able to prove the worth of your PdM efforts to management
and make data-driven decisions for optimizing your maintenance operations.
3 . A C C U R A T E
F O R E C A S T I N G
F O R B U D G E T S
By predicting when a piece of equipment will fail or reach the end of its useful life, you can
then accurately project those expenses into your budget. If, for example, you see that a
piece of equipment needs to be repaired soon based on your PdM analysis, you can also
look back at that equipment's work orders for typical repair hours and costs associated. If
you determine that it costs more to repair than to replace it, you can then justify this in a
report that uses both your condition monitoring data and maintenance history.
4 . I N F O R M A T I O N
O N T H E G O
A CMMS mobile app ensures that technicians can work directly at the plant floor without
interrupting their workflow by having to return to their desktop computers. This allows your
technicians to work on the floor and receive up-to-date information from wherever they
are. They can also attach photos and other documentation to open work orders, use QR
codes and more.
The Next Revolution
for Maintenance
Any initiative that you take on in maintenance for
manufacturing should be toward maintaining the
lifeblood of your organization: Your machines. On
top of that, a new maintenance program needs to
make your lives easier, not more difficult. With all of
the IoT capabilities out there on the market, there are
many ways that you can improve your operations.
Dude Solutions’ Asset Essentials solution works
to empower manufacturing maintenance teams
with features that are designed specifically for
their unique needs. On top of that, all of the core
functionality is available in the user-friendly mobile
app, allowing for more time spent in the field and
less at a desktop computer. The mobile app access
makes it even simpler for personnel to respond to
notifications. Plus, with detailed reporting, it’s easy
to prove the worth of initiatives to stakeholders and
to create accurate capital projections.
6
866.455.3833 / [email protected] / dudesolutions.com
A B O U T D U D E S O L U T I O N S
Dude Solutions is a leading software-as-a-service (SaaS) provider
of operations management solutions to education, government,
healthcare, senior living, manufacturing and membership-
based organizations. For nearly two decades, Dude Solutions
has inspired clients to create better work and better lives. We
combine innovative, user-friendly technology with the world’s
smartest operations engine, empowering operations leaders to
transform the most important places in our lives. Today, more than
10,000 organizations use our award-winning software to manage
maintenance, assets, energy, safety, IT, events and more. For more
information, visit dudesolutions.com.
SOURCES
1 Bernard Marr. “What Everyone Must Know About Industry 4.0.”
Forbes.
https://www.forbes.com/sites/bernardmarr/2016/06/20/what-
everyone-must-know-about-industry-4-0/#4b9699ef795f
2 Kevin O’Marah. “IoT and the Digitization of Manufacturing.”
Industry Week.
http://www.industryweek.com/manufacturing-smarter
3 “Predictive Maintenance: PdM Survey Summary 2017.” Plant
Services.
http://info.plantservices.com/ty-pdm-survey-summary-
2017?submissionGuid=1134c548-216c-4818-b53f-1a98c42de2cf