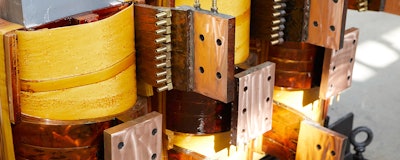
Power transformers can last anywhere from 15-30 years, but when they enter the end of their life cycle and suddenly self-destruct, plant managers are left scrambling to find a replacement. Under the gun, they often believe the best move is to source a duplicate from the exact same manufacturer. Otherwise, the fear is that the installation will slow to a crawl while contractors in the field try to make a square peg fit in a round hole, almost literally. For good reason, too, as the process of trying to match the transformer bus work and fitting it into the enclosure can drastically delay installation and keep a plant offline for far too long.
However, the availability of transformer manufacturers that specialize in customizing the bus work and footprint to match an end-user’s setup saves time and money, while greatly reducing downtime and the associated headaches. Plant engineers can benefit from a few tips before choosing based on the lowest quote.
Case in Point
The fear of switching to a different transformer manufacturer is well founded, as many engineers have been burned by the false promises from some vendors who proclaim, “Trust us, we can do it and it will fit,” with their fingers crossed. Quite often, it doesn’t. Feet that don’t match runners and bus bars that don’t line up properly often delay installations for days or weeks until everything can be cobbled together. In the meantime, production suffers.
Last summer, the CertainTeed plant in L’Anse, Michigan, encountered this exact issue. They had a turn-to-turn short in the 1000 KVA transformer running their manufacturing floor. “It ended up being a total failure, so production went down immediately,” recalls Logan Edwards, an electrical engineer for the building products producer.
CertainTeed is a North American brand of exterior and interior building products, including roofing, siding, fences, decking, railing, trim, insulation, gypsum and ceilings.
“We could not afford to halt production, so I rented a 1000 KVA generator until we could get an exact replacement for the transformer,” continues Edwards. “But the monthly rental fee for the generator was extremely expensive—approaching five figures. Plus, the fuel required to run it was costing thousands of dollars. The hard part was none of this was considered capital. It was all an operating expense. So, we needed a transformer, fast to help offset the mounting operating costs.”
Finding Like for Like, in a Hurry
In search of not only a fast and perfect fit—along with original quality of construction—plant engineers often assume that they can still get the same exact replacement from the same exact manufacturer.
“The reality is that many of the original manufacturers went out of business long ago or were bought out,” observes Alan Ober, an engineering manager at ELSCO, Cincinnati, Ohio-based transformer manufacturer. “For instance, GE Industrial, Square D, Schneider and a lot of others are either no longer in business or are part of other companies now.”
Even if a plant manager insisted on a power transformer being built to original specifications, that can take an extended amount of time, and there still is no guarantee that the unit would match exactly.
Yet, through much due diligence some plant engineers have discovered a way around the “exact replacement vs. quick replacement” dilemma in the form of vendors who specialize in repairing original transformers, or building new transformers with quality materials, in advance.
Once completed, both remanufactured and new transformers are stocked in a warehouse. When an engineer calls up for an emergency replacement, the transformer is pulled out of storage, custom bus work is machined to the exact specifications of the enclosure, and the transformer is loaded onto a truck. Some manufacturers can do all this in a matter of 24-36 hours.
Much of the credit for such a solution goes to the careful gathering of the dimensions of the transformer, and then duplicating it as precisely as possible. As a result, both the high side and low side line up as in the original installation. The same attention to dimensional detail extends to ensuring the transformer feet fit on the front-to-back runners of the existing enclosure. As a result, the transformer gets energized quickly and the plant resumes full operation with minimal downtime.
Failed Delivery
“I started looking to see who could get me a dry type transformer to replace the blown one,” continues Edwards. “The rating would be the same, but we knew it would be hard to find a custom retrofit transformer.”
Edwards gathered multiple quotes from different vendors and decided upon one who promised form-fitting bus work at a bargain price. Part of the low price stemmed from the fact that their transformer was wound with aluminum, which costs less than copper but is also less durable.
“They said, ‘Don’t worry. We’ll have it done by such-and-such time,’ adds Edwards. “So, we scheduled a specific downtime to get it installed.”
However, as is often the case, the manufacturer over promised and under delivered.
“The weekend before we were set for installation, they called to tell me that there had been some issues and it wasn’t going to happen by the scheduled date,” explains Edwards. “What a letdown.”
Not only was it a hassle for the plant to reschedule the downtime, but they were still piling up operational costs with the generator.
That’s when Edwards reached out to a transformer manufacturer that was able to rush over a transformer with custom bus work before the ‘down’ which was scheduled that week.
Measuring Up
Few manufacturers offer the customization of a transformer before shipping, and of those only a handful can turn it around within a day or two and guarantee it fits right the first time. Therefore, it is critical to ensure the vendor selected is actually capable of the carrying out the task.
The trick for any transformer manufacturer to create custom bus work that match exactly is to obtain the exact tolerances. This may seem simple, but it’s more than just H x W x L.
“If the bus is right there where it’s supposed to be, then all the installers have to do is measure the cable coming from high-side switch, cut it, terminate it, and they are done,” says Ober. “Then, you can energize it in as little as two hours after the transformer is setting on its base.”
Edwards then worked with a contractor to have it installed. “We didn’t have to shim it up, nor did we have to slot any additional holes. Everything fit perfectly.”
Dr. David Rizzo, D.P.M., is a Phoenix-based freelance writer with over 30 years of experience writing engineering documents, technical papers, and editorial content for the electric utility and power generation industry.