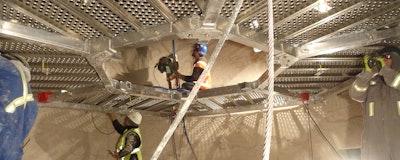
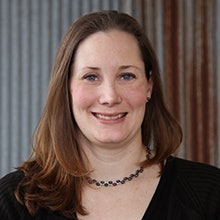
No matter the industry, annual maintenance can leave a sour taste, a feeling Amalgamated Sugar knows all too well. The largest beet processing factory in North America, its Mini-Cassia Factory in Paul, Idaho processes 18,000 tons of sugar beets and granulates 2,800,000 pounds of sugar per day. That’s enough sugar for nearly 530 million chocolate bars. So, when it comes time for annual inspections and routine maintenance, the company tries to keep it short and sweet.
Refining sugar is a highly involved process that requires a range of specialized equipment. Thankfully, as the facility has grown, so have the options to help make maintenance more efficient. The plant still slows production and shuts down certain sectors during the spring to make sure everything gets the attention it needs, but management has been able to find products that make this non-operational time much less bitter.
When the factory upgraded to a new 800-ton vertical lime kiln, it decided to look for an upgraded maintenance solution that would increase efficiency and decrease downtime. The search was met with sweet success.
New Kiln, New Solutions
In 2012, Amalgamated Sugar completed work on its new Eberhardt Lime Shaft Kiln KR8.0. The 260-foot vertical lime kiln replaced two older kilns, a Union Carbide and a Belgian, with a combined capacity of 500 tons. The two kilns had four compartments each and were operated individually. The system did not have a consistent control scheme for tandem operation, promoting excessive complexity and troubleshooting. The Union Carbide gas kiln was fueled by natural gas and had the tendency to lose flame and create an explosive environment if not appropriately managed. Employees had to manually open flanged air ports to insert propane burner lances in order to ignite the gas pockets and re-light the gas feed for kiln operation. The Belgian kiln was a mix-feed kiln fueled with coal stone. If the mix-feed blend was not managed appropriately, the operation would form clinkers that would promote channeling of unburnt rock, decreasing system performance and increasing the risk of employee injury or equipment damage. The ash and soot deposits would also carry through the gas system, leaving behind a film that coated the gaseous systems and promoted equipment malfunctions that increased maintenance spending.
The process of making sugar is a complex combination of heating and purifying. Lime kilns are an important ingredient in this process. Limestone is heated to 1,832 degrees F (1,000 degrees C) in the kiln. This heating process releases carbon dioxide and reduces the calcium carbonate to calcium oxide. The burned lime is mixed with sweet water to form milk of lime. Milk of lime and CO2 are then used to purify the raw beet juice.
“The new kiln has increased our product output by 160 percent,” said Dayna Anderson, Amalgamated Sugar lead lime kiln mechanic. “It allows us to move more product and has also required less maintenance than the old system.”
Like all kilns, the one at Amalgamated Sugar’s facility requires annual inspection and service to ensure safety and efficiency. With the previous setup, it took every minute of the factory’s three-month downtime to inspect and service the kilns. Amalgamated Sugar was forced to rely on a complex scaffolding system that took several days to erect. Because of time constraints and the amount of time it took to complete service, crews were never able to service all of the old kilns’ chambers in one maintenance cycle.
“Even though our crews worked in the kilns for two to three months, they were only able to tackle one chamber with major repairs each year,” Anderson said. “Then we’d rotate the next year. The new kiln is four times the size of our old kilns, so we knew we needed to find a safer, more efficient way to perform maintenance.”
The new kiln came with its own maintenance challenges. The only access point was a 54-inch-high by 36-inch-wide door 80 feet above grade that required a crane to reach with materials and tools. Crews also had a larger continuous area to inspect and service.
“The cooking section is about 60 feet tall, but we work with higher margins around the area,” Anderson said. “The crew focuses on an 80-foot section that equates to 6,600 square feet of working brick surface area. We look for any broken brick, uneven wear and clinker, any rock or metal that can melt and stick to the kiln. The bricks are nine inches deep, and if a section measures less than 5 inches deep due to wear, it’s replaced.”
Even with the new system, the kiln has to cool completely before crews can get in to work on maintenance, and the cooling process takes at least a month. Still, Amalgamated Sugar management knew there had to be a solution that would safely increase efficiency and minimize downtime for annual maintenance.
Amalgamated Sugar found the answer to its maintenance conundrum with a custom-made EZ Lift Suspended Platform from Bricking Solutions, a provider of kiln refractory installation equipment. The 22-foot diameter platform, constructed of high-strength 6061-T6 aluminum, offers a net load capacity of 6,000 pounds (2,722 kilograms). The platform, suspended by six 1,500-pound-capacity hoists, carries a four-person team, tools and materials up and down the 80-foot work area.
“We carry buckets, bricks, hand tools, brick insulation (wool) and all the other materials we need for hours of uninterrupted work,” Anderson said. “Before the platform, we had to make multiple trips for these items. The platform provides a safe, sturdy work environment where multiple people can tackle a lot more surface area per hour than in the past. The EZ Lift Suspended Platform has allowed for improved maintenance activities in a shorter timeframe with its security and convenience.”
The suspended platform offers a modular design with easy assembly. Each piece weighs less than 45 pounds and effortlessly fits through the kiln’s small door. Initial assembly took a day and included some one-time welding, but now Amalgamated Sugar’s crew can assemble the entire rig in just a few hours.
“The suspended platform gives us the safety and maneuverability we need to get annual maintenance done quickly,” Anderson said. “We can now get all the maintenance work completed in eight weeks. That’s a huge improvement over what we used to do.”
Sweet Success
The 360-degree accessibility provided by the suspended platform means crews can quickly complete more thorough inspections, diminishing downtime. Time saved erecting complex scaffolding systems can be applied to maintenance. The open design also means workers have easy access to the entire work surface. In the past, scaffolding frequently obscured small flaws causing them to be overlooked. The suspended platform incorporates mechanically extendable outriggers for positioning and stabilizing while still leaving room for crews to inspect every inch of work surface.
In addition to the increased safety provided by a thorough inspection, the suspended platform makes routine maintenance safer for the work crew. The platform boasts one of the highest safety ratings in the industry and meets OSHA, ANSI, CSA and EN safety standards. Maintenance repairs are also much safer and more efficient because the necessary materials and equipment are stored right on the platform, eliminating the danger associated with manually moving materials up and down scaffolding systems.
With annual maintenance completed thoroughly and efficiently, the platform quickly breaks down for easy storage in the Mini-Cassia factory break area where it will stay until next year. Amalgamated Sugar has been using the suspended platform for five years.
“In that time, we’ve only found one small dent,” Anderson said. “For the work we put it through every year, that’s impressive durability.”
So impressive that Amalgamated Sugar has partnered with Bricking Solutions for a second suspended platform. Like the original platform for the Eberhardt Lime Shaft Kiln, the new suspended platform was custom designed for cleaning and maintenance on the interior of a vertical silo—this time for new sugar storage silos for Amalgamated Sugar’s Paul, Indiana facility. The new platform is rectangular in shape but curved along one side, allowing it to move along the interior of the 60-foot diameter silo. It is 20 feet wide by 24 feet deep with a capacity of 2,000 pounds and uses four air hoists rated for use in the silo’s combustible environment. All components had to fit through a three-foot by three-foot door, and be light enough to be carried by hand. Similar to the original platform, the new suspended platform features a modular design with pin-together, repeatable components that do not require tools after the initial assembly to maximize efficiency. It is also equipped with sturdy fall guards and toe boards around the perimeter for increased safety.
After decades of ladders and scaffolding, Amalgamated Sugar officials are excited to have found a safe, durable solution that increases the efficiency of kiln maintenance. The custom-designed platform improves ROI by diminishing downtime, while providing a comfortable work area for the whole crew. All in all, it makes for a sweet deal.
Arielle Windham is a writer for the cement and refractory industries.