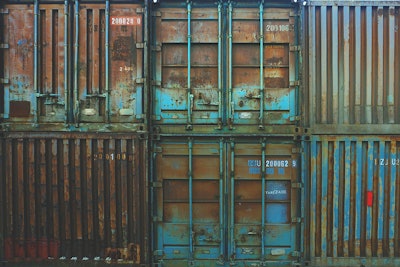
From New York to Kansas, America’s infrastructure is aging. Bridges are in need of major repair, roads are unsafe, and pipelines are becoming unusable. One of the major causes of this disrepair has to do with material corrosion. The situation is worsening and is impacting everything from health and safety to operational performance, putting company resources, employee safety and facilities at risk. Simply put, corrosion affects everything. From material waste and plant shut-downs to contaminations, increased maintenance and risk of safety hazards and much more. It is therefore no surprise that the cost of corrosion to the US economy has been estimated at $2.5tn and accounts for 3.4 percent of GDP. The American Society of Civil Engineers (ASCE) has said the US will need to invest $4.59 trillion by 2025 to improve the nation's infrastructure, including addressing the issue of corrosion.
Currently, engineers spend a large portion of their time inspecting, preventing and managing corroded infrastructure. This is underlined by the fact that, according to the leading engineering database Knovel, corrosion is the most searched-for term amongst oil and gas engineers, and one of the top ten search terms amid chemistry professionals overall.
Opening Up Pandora’s Box
Identifying corrosion can be a challenge. Although in some cases it is obvious, more often, corrosion is discovered after the damage has been done. This can mean that engineers can waste time on unnecessary inspections, or, not catch the damage fast enough to mitigate it. For example, in a recent study by scientists from the Swiss Federal Institute of Technology (ETH) in Zurich to understand corrosion in reinforced-concrete bridges, the team discovered that the concrete samples being tested were too small. As a result, they were unable to accurately measure the level of decay. Such uncertainty could have fatal consequences if left unaddressed — if you don’t find corrosion, it will find you.
But the problem of unearthing corrosion is only the beginning. Once it has been discovered, many factors must be taken into account before the engineer can identify the root cause; from heat, to humidity, to salinity. Often corrosion does not have one single cause, but occurs due to a multitude of interacting factors. This can leave engineers in a challenging position. For example, if they find a corroding tank, they need to work out if it’s a result of the chemical stored inside or from external factors such as the tank overheating due to it being in direct sunlight, or, potentially, a combination of both factors. In such cases, two fixes would be required, but without the right data, it’s impossible to know.
Waving Or drowning?
To decide how to best deal with corrosion, engineers need to not only know the type of corrosion they are dealing with, but also the typical corrosion rate for any material they are using. NASA spends $276bn a year on the best anti-corrosion materials, an amount that is isn’t a possibility for the majority of businesses dealing with corrosion. However, if corrosion is managed and treated correctly, companies can save billions of dollars. Therefore, access to the right data, insights and answers becomes critical. Firms need to make sure they have the correct data at their disposal, understanding both the costs and side effects that any potential corrosion inhibitors may have, to make the best, most resource and cost-effective decisions.
But accessing this data is only the first step; engineers need that data in a digestible, easy-to-use format. Engineers need digital tools that allow them to sort and filter this data quickly, help them understand the trade-offs in each situation can help engineers reduce the rate of corrosion and save valuable resources both in the immediate future and longer-term. These digital tools also provide engineers with the very latest research on material innovation, ensuring they are best equipped to deal with corrosion.
Taking A Proactive Approach To Corrosion
Corrosion has a significant impact on infrastructure; it can endanger the safety of a workforce and the public, cause damage to company resources, and drain the time of engineers. We often see organisations reacting to corrosion after the event, undertaking ‘damage control’ to reduce the impact of an issue that could have been mitigated in earlier stages of the development process. For example, Hyundai recently discovered the effect of this problem after they had to recall 30,000 cars in order to fix bonnets at risk of flying open due to rusty latch cables.
Instead of adopting a reactionary approach, companies should look to provide engineers with access to critical data that is easy to use and apply. The subject of corrosion control management is so vast and there are no ideal stand-alone standards that cover all eventualities, so it is imperative that engineers manage corrosion related issues using well-resourced information to discover the optimal solution in each instance. It’s clear that tackling corrosion before it becomes a serious problem, or potentially puts lives at risk, is a wise investment.
Sumita Singh, Managing Director of Reference Solutions, Elsevier’s R&D Solutions.