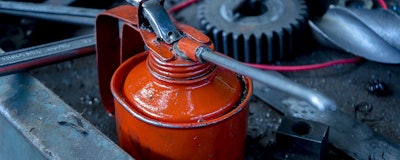
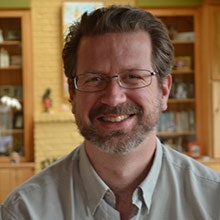
Lubrication is one of those things that often falls by the wayside... until something starts screeching or smoking, that is. Too many plant managers and maintenance personnel have the attitude that the best way to lubricate something is to just slap on the cheapest stuff they can find and check back in a few weeks. Believe it or not, this thinking may be bringing you dangerously close to the bottom line in ways you haven’t thought of... such as needless expenses on equipment maintenance and replacement, downtime, and energy costs you thought were unavoidable.
This is not just a piece about how to save money on lubrication (although that is one of the tips we’ll share). It’s actually about how to save money on a bigger scale, by taking a good, hard look at your plant-wide lubrication practices. A well-planned lubrication regime can have a strong positive impact on your business in ways you may not have thought of.
1) Stop Cheaping Out
Lubricant is an essential business expense, and as in everything else in life, you get what you pay for. Cheap lubricant has a number of flaws. It runs out in high temperatures, seizes up in cold, and breaks down under pressure. It’s easily washed off, which is especially damaging in places like poultry production plants, or in processes that involve a lot of water, such as pressboard manufacturing. In such scenarios, it means a time-consuming daily relubrication program. It also creates the potential for rapidly-forming rust and wear in chains and bearings, among other places.
A good-quality lubricant should be up to the challenges of your industry, and it should last a long time. You shouldn’t have to treat it gently or worry that it won’t do its job. It should just work. Best of all is a lubricant that both lubricates and protects. A high-performance lubricant may cost more than the cheap stuff, but it will repay you for your investment many times over.
2) Remove Duplicates and Replace with Multi-Use Lubricants
Take a look at your lubricant cabinet. How many products do you have in there that do the same thing? Line them up next to each other and cast a critical eye over them. Get rid of the ones that you haven’t used in the last six months. Then take another look at the survivors.
How many of your lubes perform different functions that could be provided by a single product? For example, lubricants exist that are both dielectric and food-safe. You don’t need to buy two different products to get these features.
3) Make Math Your Friend
Following up on Tip No. 2, if you do want to change lubes but aren’t ready to commit to a plant-wide shift, try using a new product on just one line or machine. Use a spreadsheet to keep track of how much maintenance and downtime that area requires after switching, and don’t forget to include how much you spent on lubing that area. Did your number of bearing replacements drop? Do you have to relubricate less often? If so, your decision to switch is an easy one.
4) Use Lubricants Appropriate for the Application
Your original equipment manufacturer (OEM) recommendation is always your safest bet, but what do you do if that product is no longer available? What if there is no recommendation? In that case, consult a qualified lubricant specialist to recommend a product that will suit your application.
For example, should you be using a dry lube on that long-pitch chain? (No, you shouldn’t.) Should you be using mineral oil in your food production area just because it’s food-safe? (Absolutely not.) It’s probably worth it to have your lubes assessed anyway, especially if it’s been a few years. New products come on the market all the time, and it takes minimal effort to stay current.
5) Use Automatic Dispensers
Once you’ve identified that you are in fact using the right lubricant for the application, check to find out if you can implement an automatic lube dispenser on that machine. Automatic dispensers can end up saving you many hours of labor, and many dollars in wasted lubricant or damaged parts (which happens when over-lubricating) or downtime and repair (from under-lubricating).
One area where automatic lubrication is really desirable is HVAC. Read Tip No. 6 to learn why.
6) HVAC: Who’s in Charge?
Your plant’s HVAC system is probably your least-noticed equipment, for two reasons: it’s usually up on the roof, which means out of sight, out of mind; and it’s usually not the province of the production manager, because it doesn’t actually produce anything.
Here’s why that’s a bad thing: HVAC is subject to big temperature swings, which is hard on lubricant. Unless you don’t mind venturing out onto the roof in blazing heat or driving snow, it’s probably being neglected. HVAC systems are excellent candidates for automatic lubrication. That way, you only have to go up there every six months, which saves money on labor, and your equipment will last longer. You’ll also see savings in energy costs.
7) Make Sure Maintenance is on Board
Smart people know that there are two kinds of people you absolutely need on your side in life: secretaries and maintenance personnel. These are the people who keep things running on a daily basis, performing the thousand and one small tasks that no one else sees. It’s crucial that maintenance understands your lubrication goals and strategies and is trained on how to implement them. Have a talk with your team to explain your new lubrication philosophy. Make sure they know your goals, your proposed schedule, and your rationale for any changes you’re making. It won’t be a hard sell once they see how it helps make their jobs easier.
William Kowalski is the Director of Online Operations at Interflon USA. He can be reached at [email protected].