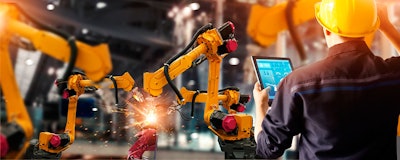
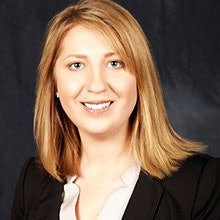
It’s an exciting time to be in manufacturing. Industry 4.0 is becoming more than just a talking point: manufacturers are beginning to realize the extent to which harnessing innovations stimulated by the IoT will transform their environments to achieve smarter business outcomes. Because of this transformation, connected infrastructure has become an integral part of the business strategy for leading manufacturers.
Navigating these changes means that safety and maintenance staff need to spend time, engineering, and plenty of resources adapting new electrical systems into their environment. To expand in an efficient and cost-effective manner, this often means thinking about safety first. When a facility—like a manufacturing plant—grows in size, and machines are added, any changes to the electrical system need to be documented and evaluated to see if this new equipment presents any new or additional hazards to workers who operate and maintain the equipment.
Today’s plant automation is characterized by connected infrastructure. From state-of-the-art production lines to robotics, the amount of equipment requiring reliable power is steadily growing. Thus, a greater burden is placed on facility and maintenance teams tasked with ensuring reliable power is available to keep equipment and processes running at optimal levels.
In any type of manufacturing environment, it’s important that both the management and the workforce understand how safety is paramount to maximizing productivity in the workplace. A qualified electrical worker not only needs to be familiar with the facility’s electrical system, but also the latest electrical safety standards and best practices. An employer is responsible for providing a safe work environment and is tasked with ensuring workers deemed “qualified electrical personnel” are properly trained and equipped to perform relevant electrical maintenance tasks that reflect the up-to-date training they have received. Electrical workers who lack the proper training and skills to do their jobs find themselves in a risky spot, and if an incident happens, the result can be unexpected downtime that disrupts productivity and wreaks havoc on the bottom line.
Thinking about electrical safety and standards compliance during the planning and implementation process for adding or modifying equipment is important and should never be an afterthought. The key to its design is to eliminate or avoid the electrical hazard altogether, and to keep the facility aligned with the latest industry standards and best practices.
Navigate the Changes in Standards
As safety standards evolve, so too must the company and its workforce. The latest release of NFPA 70E-2018 includes an update to distinguish between the processes for verifying the absence of voltage when using portable versus permanently mounted test equipment.
The permanently mounted test device can be used to verify electrical conductors and circuit parts are de-energized before the equipment is accessed, preventing exposure to electrical hazards. These permanently mounted testers must be installed at the point of work in accordance with manufacturer’s instructions, listed and labeled for the purpose of verifying the absence of voltage, and satisfy additional requirements outlined in the standard. One example of a product that meets these requirements is an Absence of Voltage Tester (AVT), listed to UL 1436. The manual verification process is complicated and includes numerous steps, including the selection of a tester, the testing of a tester, checking for voltage, and retesting the tester, before performing work. An AVT automates this process but still follows the same steps used with handheld testers, beginning with a simple activation and ending with an indicator that it is safe open the panel. The middle steps are completely automated based on the recommendations of NFPA 70E-2018, and an AVT will display information about the status of voltage inside equipment without exposure to electrical hazards.
Navigate the Changes in the Plant’s Equipment
When a business grows its facility grows. As new machines are added, the electrical capacity needs grow, and thus an increased need for overall, plant-wide electrical safety grows. While codes and standards evolve, and as equipment is added—often from multiple vendors—compatibility issues can arise. Standardizing processes and procedures can help minimize or prevent human error.
Navigate the Changes in plant Operations and Performance
The rise of Industry 4.0 in plants today is proof that automation is here and will increase the amount of electrical maintenance performed in a facility. As a general rule, workers will need to be trained to recognize electrical hazards and not interrupt or distract qualified electrical worker while servicing equipment. This will require an effective training program. In addition to meeting the training requirements set by NFPA 70E and OSHA, it’s highly recommended that training is repeated in different formats periodically in order to keep it fresh and top-of-mind. This may toggle between classroom instruction, hands-on demonstrations, and skill audits.
While Industry 4.0 brings many opportunities to the plant environment, it will also create some challenges. New equipment brings new types of hazards and risks. Being able to identify these hazards and having the tools, safety procedures, and instructions available to mitigate risk will not only be essential to ensuring the success of Industry 4.0, but critical to those working in this new environment.
Rachel Bugaris is a Business Development Manager at Panduit Corp, where her work focuses on electrical safety solutions for the workplace. She has a background in Research and Development, designing products ranging from absence of voltage testers to arc resistant equipment. Rachel participates and has held leadership positions in several IEEE committees, including the Electrical Safety Committee, Petroleum and Chemical Industry Committee, Pulp & Paper Industry Committee, and standards working groups (IEEE C37.20.7, IEEE 1683, IEEE 1584, UL 1436). Rachel has a Bachelor of Science in Mechanical Engineering from the University of Notre Dame. She is a member of IEEE and SWE. She has multiple patents and has written several technical papers on electrical safety topics.