
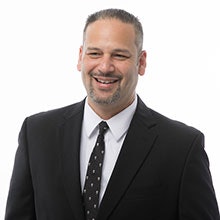
In honor of National Cut Your Energy Costs Day on Jan. 10, many consumers will add to their New Year’s Resolution list with a plan to reduce energy consumption and cost. While even small steps like lowering home thermostat temperature by one degree or covering drafty windows with plastic sheeting in the winter can make a big difference for individuals, these savings are pocket change in comparison to the massive energy savings potential that industrial facilities can see by taking their own relatively small step toward efficiency.
By simply modernizing their lighting fixtures with high-efficiency industrial LED lighting, companies can potentially cut their lighting energy consumption by as much as 80 to 90 percent over legacy systems like high-pressure sodium (HPS) and other high-intensity diode (HID) sources. With industrial lighting alone consuming some 58 terawatt hours of energy in the U.S. alone, switching to industrial LED lighting could cut that usage by 52 terawatt hours, saving enough energy to light 37 million homes.
With some 144 million industrial fixtures in use at 455,000 facilities in the U.S., switching to industrial LED fixtures could save American companies a combined total of $3.6 billion in energy cost each year. That’s in addition to the substantial savings reduced maintenance costs thanks to LED’s much longer useful life, which eliminates the frequent bulb changes common with HPS and other conventional lights for up to a decade or more.
How can switching to industrial LED fixtures have such a tremendous energy saving advantage? Here are five ways industrial LED lighting can cut energy costs today and for years down the road.
- Up to 90 percent greater efficiency per fixture. Compared to electricity-hogging conventional HID systems, industrial LED fixtures sip energy. With some of the highest-efficiency LED systems now up to 90 percent more efficient1 than equivalent output HPS lights, this dramatic reduction in energy use adds up fast when you consider that a single facility might have thousands of lights burning 24/7. Industrial lighting uses enough power to light a third of all homes in the U.S.2, which means any reduction here can have a substantial impact on overall energy use.
- Twice the light at half the energy. Because industrial LED fixtures deliver up to 60 percent more light output at the source, facilities get more lumens per watt with LEDs compared to HPS and other HID lighting. And, because LEDs can be configured to direct the light exactly where it’s needed—on the ground and other critical areas—this results in less wasted light on the walls, ceiling and other unnecessary areas, resulting in over 30 percent more delivered light. That means companies get more light where they need it, often with fewer fixtures, and more bang for their buck.
- Smart controls add 50 percent more savings. Unlike HPS fixtures, which require an extended warmup period to come up to full output, LED fixtures are instant-on, delivering full output the moment the switch is flipped. This enables industrial LED fixtures to be equipped with smart controls, such as occupancy and daylight harvesting sensors, as well as programmed dimming and other configurable lighting schematics. This dramatically reduces burn time compared to HPS lights, which are often left burning 24/7 to avoid the warmup and can further cut energy use and cost by up to 50 percent per day.
- Lower maintenance energy cost. Conventional HPS bulbs fail as often as every 24,000 hours and more frequently in high-vibration and other harsh environments, resulting in frequent change-out. This routine maintenance often requires the use of mechanical lifts, supplemental lighting and production shutdowns that can add to a facility’s energy costs. Because high-performance industrial LED fixtures can last more than 100,000 hours9, virtually eliminating lighting maintenance for up to 10 years or more, companies can avoid wasting the energy (and time and money) it takes to replace lamps.
- Reducing pollution saves more money (and the planet). The cost savings associated with switching from HPS to LED lighting extend beyond the direct energy expenses. As more companies aim to reduce their carbon footprint, lowering energy consumption can also reduce the need to purchase carbon credits to offset their emissions. Meanwhile, disposal of conventional HPS bulbs (one of which contains enough mercury to poison an entire classroom of children) requires additional hazmat handling costs, which are eliminated by converting to LEDs. On the upside of the equation, sustainable operations are also good for business, with an estimated $1.2 trillion opportunity for brands that publicize their sustainable efforts.
With hundreds of millions of industrial fixtures in place, fewer than 90 percent of which are LED system, there is a tremendous opportunity for businesses to cut their energy costs by converting to industrial LED technology. Making the switch not only delivers an immediate drop in electricity use that generates a quick payback, but because of their long-life performance, the cost-saving benefits of LED fixtures continues to add up over time.
With a wider variety of fixtures now available at a cost that’s declined 80 percent in the last five years as the technology has matured, investing in high-performance, high-efficiency industrial LED fixtures can be one of the most effective ways for companies to cut energy costs as well as improve overall plant efficiency and sustainability.
Luis Ramirez is the COO of Dialight.