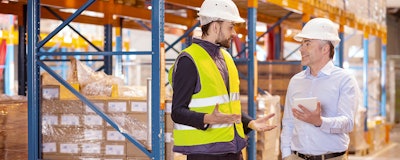
The fear that technology will replace a job or worker has existed for centuries. The infamous example of Luddites breaking textile machinery to preserve their jobs may have occurred in the 19th century, but many in the 21st century still react to change with defensiveness and concern.
This is only natural. Humans are hardwired to scrutinize new information. There are several techniques that help ease transitions—introduce something new with something familiar, for example, or have a leader demonstrate his commitment to the technology by using it first. But the best way we’ve found to transition employees to new technology is to demonstrate to them how the tech will keep them safe.
In so many ways, automation and wearables accomplish that goal and more. Our MARK 2, for example, allows for improved attention and focus on tasks, as it is handsfree. It also avoids repetitive stress injuries from pulling on a scangun thousands of times throughout a day.
In other examples, vests connected to forklifts can also alert the drivers when someone is in proximity, reducing the number of possible accidents. And using tools to help place packages reduces the risk of a pallet collapsing, as they can place packages in less precarious positions.
The examples go on, as new wearables and technologies are coming out regularly to improve worker safety and productivity. Human-centric design satisfies both of these needs, and puts the employee at the heart of the process; instead of being a person to be replaced, he or she is someone to be empowered.
Moreover, the benefits of focusing on safety stretch far beyond the introduction of new technologies. In a now-famous story of ALCOA, the aluminum manufacturer, focusing on safety created a tremendous benefit for the company itself. As workers began to feel that their safety came first, they cared more deeply about the company and turned in a better product as a result. Problems, once identified, would immediately be slated for improvements—and as the company began to reinvest in its workers, their habits changed and improved. After just a couple of years, ALCOA began to deliver record profits and revenues. The workers lifted the company, which benefited from the change.
Today, many companies feel pressure to innovate. They see the rise of technology companies and the ability for technology to improve bottom lines and profits, but many workers would perceive such arguments as insensitive to their needs and obligations.
Rather, the best way to get buy-in from men and women on a factory floor is to demonstrate the benefits directly to your employees—that these technologies make good on the promise that they’ll go home from work in the same conditions they arrived.
Charlie Grieco recently joined ProGlove, as Vice President of Sales and North American Operations.