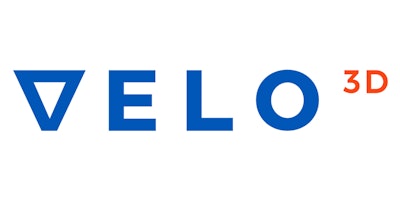
Campbell, CA — Velo3D recently announced the general release of its end-to-end metal additive manufacturing (AM) solution comprised of the Sapphire system, Flow print preparation software, and Intelligent Fusion technology. Together, the integrated solution solves some of the most difficult AM challenges including product design limitations, part-to-part consistency, process control and cost-effective manufacturing.
“Additive manufacturing has the potential to be revolutionary,” said Ashley Nichols, general manager at 3D Material Technologies (3DMT), a leading metal additive manufacturing services bureau.“Systems are getting bigger, but not delivering on the promises of metal additive manufacturing. Through a collaborative partnership, 3DMT and Velo3D are unlocking new applications, pushing the envelope of what is currently considered possible. We look forward to continued success, and to delivering on the promises of the potential of metal additive manufacturing.”
Sapphire System
The Sapphire system is a laser powder bed metal additive 3D printing system designed for high volume manufacturing. Sapphire is capable of building complex geometries including designs with overhangs that are less than five degrees and large inner diameters without supports – something previously unheard of in the AM industry. To deliver superior part-to-part consistency, Sapphire’s integrated in-situ process metrology enables first-of-its-kind closed loop melt pool control. To maximize productivity, the Sapphire system contains a module that enables automated change-over with offline unpacking.
Flow Print Preparation Software
Flow print preparation software includes support generation, process selection, slicing and simulation of complex part designs to validate execution feasibility before the build. Geometrical feature-driven processing enables low angles below five degrees. In addition, deformation correction technology enables the user to produce parts without the need for iterations, achieving a first print success rate of up to 90 percent. Flow minimizes the need for supports, reducing typical support volume by 3-5 times, which removes or reduces the laborious post processing necessary with conventional approaches.
Intelligent Fusion Technology
Enabling an end-to-end integrated workflow, Intelligent Fusion is the technology that powers Flow software and the Sapphire system. Intelligent Fusion optimizes the AM process by combining thermal process simulation, print prediction, and closed-loop control during print execution.
“Four years ago, we set out with the bold vision of creating technology that could manufacture parts with any geometry to take additive manufacturing mainstream,” said Benny Buller, founder and CEO of Velo3D. “Our approach relies on creating deep insights in physics fundamentals, enabled by research, characterizing and understanding of core mechanisms, developing intelligent process control through software simulation and in-situ metrology. Today, Velo3D is working with some of the top OEMs and service bureaus creating parts that were once considered impossible.”
Velo3D systems are currently used by original equipment manufacturers (OEMs) and manufacturing service providers.