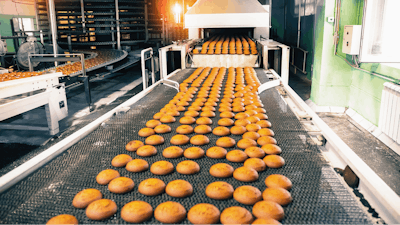
A bottleneck in production can cause significant delays and impede progress. These obstructions can cause severe delays and disrupt workflow, resulting in decreased productivity and quality. Did you know that almost 40 percent of industrial resources go to waste due to bottlenecks? In production, they create a $12 trillion loss to the global economy.
Often, manufacturers can resolve common production bottlenecks by identifying and addressing the root of the problem. To combat this, it is crucial to understand what these hindrances are and how to prevent them. There are a variety of production bottlenecks that can occur, and the following are some of the most common:
1. Inadequate Maintenance Planning
This can occur when there is a lack of communication between departments, insufficient resources, or unrealistic deadlines. These events can lead to disruptions in the manufacturing process and cause delays. An example of this would be poor communication between the engineering department and the production department, resulting in a lack of information about the manufacturing process.
How to Prevent Inadequate Maintenance Planning: It is crucial to have clear communication between all departments involved in the manufacturing process. To ensure better maintenance planning, there should be a clear understanding of the available resources and what is needed to complete the task. All departments should also be aware of their objectives and roles.
In addition, deadlines should be realistic and achievable. Time and dates for milestones should be reasonable, feasible, and consider any potential disruptions.
2. Inefficient Processes
An inefficient process is often the result of poor training, a lack of standardization, or outdated equipment. An example of an inefficient process would be a production line that is constantly breaking down because the machines are not regularly serviced and repaired. This can lead to costly downtime and delays in production.
How to Prevent Inefficient Processes:
- Automate as much of the process as possible. Automation can help to eliminate errors and improve efficiency.
- Provide adequate training to all employees involved in the process. Good training will ensure that everyone knows how to operate the equipment and perform their tasks properly.
- Create and enforce standardized procedures. A standardized system will help to eliminate errors and inconsistencies in the process.
- Make sure that all equipment is well-maintained and up-to-date. Well-maintained equipment will reduce the chances of breakdowns and improve overall efficiency.
3. Lack of Skilled Labor
Lack of skilled labor can occur when there is a shortage of qualified workers, or when employees are not adequately trained. This can cause production to grind as employees cannot complete tasks. An example of this occurred in 2020 when a shortage of skilled labor in the UK construction industry occurred. The lack of skilled workers led to delays and cost overruns on numerous projects.
How to Prevent Skilled Labor Shortages: There are a few ways to prevent this issue. One is to provide training for employees, so they have the skills needed to perform their jobs. Training such as quality control, process improvement, and machinery operation are some of the training employees would have to undergo to help solve this bottleneck. Another solution is to hire temporary skilled workers or use contract labor when there is an increase in demand. The temporary workers will ensure you have enough skilled labor available to meet production needs.
4. Poor Quality Control
Poor quality control can happen when products do not meet the required standards, such as being in the right shape, size, color, or have too many defects. This commonly happens due to a lack of testing, inadequate inspection, or defective materials. This can lead to production stoppages and delays as products need to be reworked or scrapped.
How to Prevent Poor Quality Control: Below are a few ways to prevent poor quality control:
- Make sure to test products thoroughly before they go into production. This includes prototype testing, materials testing, and performance testing.
- Inspect products at every stage of production. Inspection at every step helps to identify and fix any issues early.
- Use high-quality materials that meet all the required standards. Quality materials will help reduce the number of defects in the final product.
- Have a robust quality control system to catch errors or defects. A standard quality control system will help to ensure that only perfect products leave the factory.
- Train employees on proper quality control procedures and follow them correctly. This will help reduce mistakes and improve the overall quality of the products.
5. Limited Capacity
Limited capacity can occur due to insufficient space, equipment, or resources. For example, if a factory does not have enough space to store finished products, this can cause a bottleneck. Additionally, if there is not enough equipment to meet demand, this can also lead to delays.
How to Prevent Limited Capacity: There are a few ways to prevent limited capacity bottlenecks:
- Improve utilization. One way to do this is by ensuring that all employees are adequately trained on how to use the available equipment. Additionally, you can try to streamline processes to reduce waste and increase efficiency.
- Increase capacity - If you have the resources, you can increase your production capacity by adding more space, equipment or resources.
- Outsource - Another option is to outsource some of your production to another company. This can help to relieve some of the pressure on your own company.
- Prioritize - Prioritize your production to produce essential items first. Prioritizing will help ensure that you meet your deadlines.
These are a few common bottlenecks that can occur in production. Once you understand whatโs causing the production mishaps, it's easier to find the solution. Preventing bottlenecks will help improve your product quality and keep your production process running smoothly. You should also stay up to date on the latest technology and trends to be proactive in preventing bottlenecks.
Bryan Christiansen is the founder and CEO of Limble CMMS.