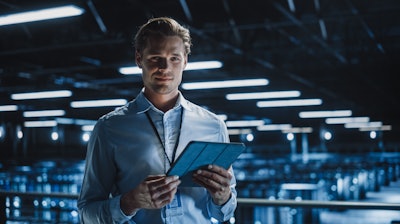
Manufacturing has witnessed a significant shift towards digital maintenance management, marking a departure from traditional methods. This transformation has led to enhanced precision in tracking maintenance activities, utilizing technological advancements for improved operational efficiency. Digitalization offers a panoramic view of maintenance needs, reducing dependence on manual processes and leading to strategic maintenance planning.
This article aims to highlight the roles of efficiency, cost-effectiveness and improved communication brought by digitization in maintenance management. Reducing costs and elevating the quality and speed of maintenance activities, digitization offers significant advantages.
Automated and Data-Driven Maintenance Processes
Data stands at the forefront of scheduling maintenance, enabling precise and timely interventions. Predictive maintenance, informed by digital systems analyzing equipment performance data, helps avert breakdowns. A proactive rather than reactive approach, facilitated by data, optimizes the lifespan and performance of machinery.
Streamlining work order processing with minimal manual intervention is a hallmark of digital systems. These systems automate the creation, allocation and tracking of work orders, ensuring efficient management of maintenance tasks. Automation reduces errors and delays, leading to a more organized and responsive maintenance process.
When connected with email, the CMMS system significantly reduces maintenance personnel's need for frequent logins. Mechanics and technicians can efficiently receive and respond to work orders via email, reducing paperwork and streamlining the maintenance process while maintaining a high level of precision and timeliness in interventions.
Key data types influencing maintenance strategies
Within the automated and data-driven maintenance processes, many data types play a crucial role in effective management. Here are key data types that significantly influence the efficiency and effectiveness of maintenance strategies:
- Equipment usage data: Understanding the frequency and manner of equipment use is vital for anticipating wear and tear. Such data aids in preempting breakdowns through timely maintenance, ensuring continuous operation and prolonging equipment life.
- Performance metrics: Keeping a close watch on efficiency levels and output quality is integral for early detection of potential issues. The timely analysis of these metrics allows for adjustments that ensure optimal equipment performance and minimize failure risks.
- Environmental conditions: Factoring in external elements such as temperature and humidity is crucial, as they can significantly impact equipment performance. Adjusting maintenance strategies in response to these conditions helps maintain equipment effectiveness.
- Maintenance history: A record of past maintenance activities offers invaluable insights for future planning. Analyzing this historical data helps identify patterns or recurring issues, leading to more focused and effective maintenance efforts.
- Error reports and feedback: Gathering and scrutinizing error reports and operator feedback is essential for continual improvement. This direct feedback provides insights into equipment performance and highlights areas needing attention, aiding in refining maintenance protocols.
A strategic approach to data analysis and application in maintenance management can lead to significant operational benefits, including reduced costs, heightened equipment efficiency and a more seamless production workflow. This data-centric method epitomizes the future of maintenance management, where informed decisions drive optimal outcomes.
Enhanced Equipment Monitoring and IoT Integration
The integration of IoT devices has revolutionized the live tracking of equipment health. These devices continuously gather and transmit data on equipment performance, alerting maintenance teams to potential issues in advance. Such proactive monitoring prevents unplanned downtime and enhances the longevity of machinery.
Preventive maintenance actions to avoid unplanned downtime are also made more feasible by digital systems. Analyzing data from sensors and usage patterns, these systems schedule maintenance tasks ahead of potential failures. Proactive maintenance not only saves resources but also ensures a continuous production flow.
Maintained Compliance and Safety through Digital Record-Keeping
Digital systems play a key role in helping businesses maintain regulatory compliance in maintenance management. Organized and accessible record-keeping platforms ensure that maintenance activities are both documented and auditable. This type of digital documentation is essential for adhering to industry standards and regulations, mitigating risks of non-compliance penalties.
Digital documentation can also help foster a safe work environment. It guarantees that safety procedures and maintenance activities are recorded and easily accessible, promoting adherence to safety protocols. Comprehensive record-keeping enhances accountability and transparency, contributing to a safer and more compliant workplace.
Achieved Cost-Effectiveness and ROI in Maintenance Management
Digitization plays a crucial role in reducing maintenance costs by streamlining processes and preventing equipment failures. Predictive maintenance, enabled by digital tools, identifies potential issues before they require costly repairs or cause downtime. Efficient management of maintenance resources through digitization leads to notable cost savings and an enhanced return on investment.
More effective machine maintenance is a direct result of digitalization. It allows for a systematic, data-driven approach, providing detailed insights into equipment performance. Targeted maintenance interventions made possible by this precision extend machinery life and ensure peak operational efficiency.
Ensuring Centralized Data and Enhanced Decision Making
Centralizing all maintenance data, CMMS digitalization markedly improves accessibility and accuracy over manual methods. The centralization ensures that maintenance records are current and readily available, enhancing the overall management of maintenance activities.
Informed decision-making regarding maintenance schedules, equipment investments and procedural enhancements are all facilitated by the centralization of maintenance data. Managers can make strategic decisions based on accurate information, optimizing resource allocation and operational efficiency.
A clear and accurate view of maintenance costs, offered via digitalization, aids in effective budgeting and cost reduction. Detailed insights into resource expenditure allow businesses to identify cost-saving areas and allocate their maintenance budget more efficiently.
Team performance is also efficiently tracked using a CMMS, providing valuable insights into productivity and areas for improvement. Such tracking enables managers to assess maintenance team effectiveness, identify training needs and implement strategies to enhance overall performance and efficiency.
The Critical Role of Digitization in Maintenance Management
Digitizing maintenance management, a process greatly facilitated by sophisticated plant maintenance software, has brought about transformative benefits in the manufacturing sector. These benefits include enhanced efficiency, cost savings and improved compliance. The ongoing evolution of digital technologies is expected to further refine and innovate maintenance management, solidifying its critical role in the industry.
Integrating data analysis, automated processes and IoT devices into maintenance plans is completely reshaping traditional maintenance. It's a shift towards being more proactive and efficient. As the manufacturing industry evolves, adopting digital solutions becomes essential, not just a nice-to-have — it's about preparing for today's demands and tomorrow's challenges and opportunities.
---
Sanjay Murthi works for SMGlobal.