To safeguard safety, work equipment must be inspected each year. This also applies to hydraulic cylinders (jacks). In general, these cylinders are inspected using a static test. “It’s irresponsible”, says Robert Dekkers, Service Manager at Holmatro.
The Holmatro Testteam Does The Test
Holmatro has made a new video to show that hydraulic equipment must be tested properly by a qualified service technician. In this video, the Holmatro Testteam demonstrates the difference between static and dynamic testing. This latest video is part of the company’s general safety campaign. In this campaign, the Holmatro Testteam mimic the risks of working with high-pressure hydraulic equipment and clearly explain this in a light-hearted manner.
Damage Is Not Always Detected Using A Static Test
Safety, efficiency and long service life... These factors are of paramount importance to Dutch hydraulics specialist Holmatro. As a manufacturer of hydraulic equipment, we know how important professional maintenance is. And, not only to ensure the equipment works optimally, but also to ensure the safety of the people who use it.
“In static tests, the cylinder is put under pressure at a certain number of levels," Robert explains. "There can be damage between or outside these levels that is not detected and yet the cylinder can still be approved as safe. Let’s say that a day after the test, the cylinder is put under 700 bars of pressure. There is nothing to worry about when the cylinder is put under pressure as long as the seal around the plunger does not come into contact with the damaged part of the cylinder. But can you imagine what happens if it does? It can cause huge amounts of damage, not just to the load, but certainly to the user. It's simply a form of Russian roulette.”
Services For High-Pressure Hydraulics On The Rise
More and more companies recognize the need to perform an annual inspection of work equipment. This also involves the inspection of high-pressure hydraulic equipment. And when demand increases, you can be sure the number of suppliers will increase. That's good news if these suppliers have the proper basic knowledge about hydraulics and also use the appropriate test resources. It’s only then that a user can trust equipment to work safely.
Inspecting the exterior of a hydraulic cylinder is not enough when assessing whether the cylinder is still safe to use. This is certainly the case when this type of industrial equipment is not always handled with care. The cylinder must be put under pressure to detect whether there is internal damage. This is usually done using a static test. However, this has been proven to be an unreliable test.
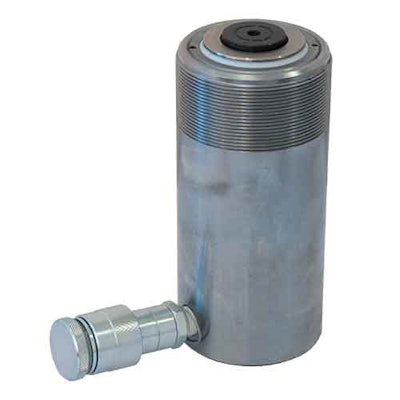
Assuring Equipment Is Safe Using Dynamic Test
Holmatro has worked for decades with dynamic hydraulic test frames. During dynamic testing, the cylinder is pressurized over the entire stroke of the cylinder. Every part of the cylinder stroke is tested. This type of test ensures that scratches and damage on the inside of the cylinder are detected.
“After the dynamic test has completed, you will know for sure that you are working with a safe hydraulic tool. And, that’s true regardless of the stroke length percentage used," Robert said.” Dynamic testing goes beyond testing cylinders over the entire stroke length. The maximum usable situation (105 percent of the capacity) for the equipment is also simulated and any overpressure safety of the system is checked. This form of testing always detects hidden damage and the user is assured that the equipment is safe and reliable.