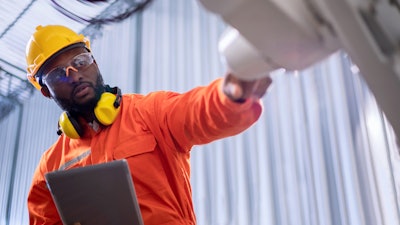
As production operations continue to grapple with the need to streamline processes and reduce overhead costs amid economic uncertainty, an increased need for transparency and predictability surrounding maintenance management has become evident.
Info-Tech Research Group has published new research, Operational Efficiency Through Predictive Maintenance, to provide support and guidance for the industry. As many operations organizations lack visibility throughout the production process, there is a demand for the enablement of better technology support to reduce downtime, avoid run-to-failure and mitigate the ripple effects of catastrophic outages when equipment or assets go down. The firm's resource will support operations leaders in their endeavors to improve maintenance planning.
The new resource explains that predictive maintenance uses data analysis tools and procedures to enable proactive management of technology, foreseeing issues before they arise. Enabling this maintenance management method also prevents unscheduled reactive maintenance and incurring costs for excessive amounts of preventive maintenance.
Info-Tech provides a breakdown of the tools to employ in the data collection and analytics of predictive maintenance in the resource, highlighting that the key to success lies within using the right tools to capture the correct real-time conditions and provide predictive monitoring data. The suggested tools are outlined below:
- Infrared thermography includes cameras that detect heat spots and provide a thermal image warning
- Acoustic monitoring uses sonic and ultrasonic levels of monitoring for sounds of liquid and air leaks
- Motor condition relies on real-time early condition monitoring for defects
- Eddy inductive current condition involves monitoring for eddy currents in conductors, which cannot be touched. Monitoring must be precise because the current may be moving at a rapid pace
- Vibration analysis offers pattern readings that can signify early onset imbalances
- Temperature monitoring refers to holistic tolerance-based temperature management
- Oil and grease analysis monitors for viscosity and foreign contaminants as well as leaks
- Internet of things (IoT), extended internet of things (xIoT), industrial internet of things (IIoT) and supervisory control and data acquisition (SCADA) are systems that provide data from a wide variety of proprietary meters
- Computerized maintenance management systems (CMMs) are used to track and service assets
As operations organizations work to make the most of their data to increase production operations' uptime, reduce maintenance costs and identify hazardous situations before they occur, Info-Tech advises operations leaders that the more established and historical maintenance management techniques cannot be replaced by predictive maintenance in all situations.
While conventional run-to-failure and preventive programs must still be used in some capacity, the firm's research shows that the implementation of predictive maintenance alongside IIoT will help organizations optimize their data to provide a host of organizational benefits, including saving both time and money, increased safety and improved workflows.