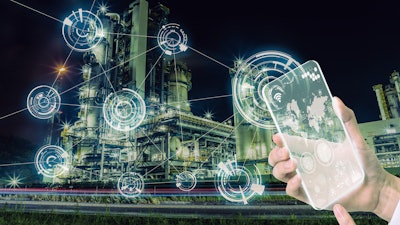
Digital transformation is advancing technologies within organizations, driving innovation, streamlining and optimizing operations, and improving business agility. Technology is also enabling employees to work more efficiently and in areas that are more fulfilling and valuable, with many repetitive or mundane tasks being automated. In this article, we explore modern Human Machine Interface (HMI) software and how the tools enabled by that software are empowering designers and operators.
Seamless Collaboration
When a software or application design team is designing a system, whether they are in-house or working within an OEM, it is common to have multiple designers working on various parts of the same project simultaneously. It is therefore important for those designers to be able to collaborate easily, flexibly, securely, and transparently, regardless of location. Whether working in the design environment in an office or at home, they need consistent quality access and user experience.
Real-time project visibility is also critical in the design phase, especially with multiple people on the design side touching a project. Lack of visibility can make it difficult to track progress. Who made the changes? When? And why? Without this information, there is the risk of repeating work or inadvertently overriding changes someone else made, which can cause project delays and waste valuable design resources and budget.
This is where the collaboration tools within modern HMI software can make design easier for teams. They provide comprehensive project visibility in a collaborative environment and connect designers to timely, useful information needed to make fast and smart decisions. HMI access to cloud or web-based tools in a centrally or cloud-based location enables teams to design and deploy an application remotely and make changes or updates within the production environment when needed.
Centralized Repository Integration
With multiple developers able to augment, develop and test each other's work, either in real-time or in sequence, code management and version control are vital elements of the design process. It is here that a centralized project repository, such as GitHub, is key. Working within an HMI interface, design tools and code can be integrated directly into that centralized repository. So, when designers are working with others on applications, this integration enables multiple users to make changes and easily merge their changes into the master version. Potential duplication of efforts can be flagged and resolved internally.
With everything integrated within the centralized environment to provide a visualization of the overall project status, teams can see the entire change history of an application version control - showing who made changes, when and why, along with different versions of pieces and parts, along with the whole overall application.
The collaborative environment created through HMI tools also enables OEMs to work with customers to build applications, share ideas or code snippets, troubleshoot solutions, and evaluate objects and demo applications via a shared centralized repository.
Another area where the HMI design tool empowers designers is creating reusable code libraries stored in the centralized code repository. That code can be reused easily by other people within an organization and can be tweaked and used in other applications. The benefit of having this readily accessible code repository is that the code is trusted and proven in the field. So, designers can utilize code modules that they know will work. They can simply drag and drop them right into the code blocks and build the application's differentiator code around that.
Empowering Operators
Once a project has been developed, deployed to the field, and is running on the plant floor, it moves into the jurisdiction of operators. They are now the key stakeholders running that application, so if an alarm or some other problem occurs, they need the means to notify the right people. If the maintenance engineers, for example, are not on-site, remote assistance is crucial for operational continuity.
With HMI tools, operators are empowered through remote access for maintenance. Accessing these tools enables issues to be flagged, and notifications sent to the maintenance engineer to contact the operator. It may be that the issue can be resolved via the built-in chat tool, with the operator relaying what they are seeing and maintenance responding with suggested options to resolve the issue.
However, resolution may require escalation, so remote access to the HMI tools is crucial in letting the maintenance engineer see what the operator sees on the screen. Together they can work through and identify what the problem is, make changes if a change is needed, and deploy that change remotely. That maintenance change to an application that is running is saved into the cloud repository, so teams know that they are running an updated version of the application.
For OEMs, the ability to connect with customers via the HMI tool delivers business value in terms of remote support and issue resolution. This saves time and of course, the money it takes to travel to a site. The net benefit of this to both OEM and the customer is that the quicker problems can be triaged and solved, the more uptime there is, which enhances business continuity.
A modern HMI can empower an organization’s workforce by removing barriers to valuable information and providing access to data and applications independent of location. Applications can be designed collaboratively and transparently, with development coordinated and stored in a shared, centralized repository. The clarity the HMI provides optimizes and speeds the development cycle as all stakeholders have up-to-date status, with updates and changes clearly defined, avoiding redundant and duplicate work.
On the operational side, HMI tools enable operators to see and respond to production issues quickly. Instead of monitoring screens to know when alarms happen, operators can be remotely notified and take immediate action themselves, or escalate for remote maintenance support and resolution.
The big-picture benefits for enterprises are optimization of design, operational and maintenance resources, faster design cycles, improved time to market, and faster issue resolution, which can drive improved revenues, operational excellence, and customer satisfaction.