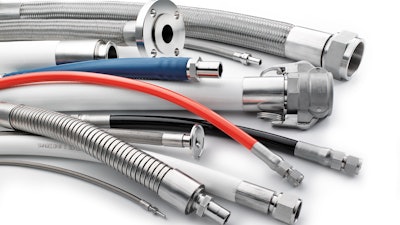
Properly maintaining an industrial fluid system requires technicians to have as much knowledge at their disposal as possible. Information such as what types of liquids or gases are being transferred, the normal operating temperature or pressure of the fluids or if they are potentially hazardous is critical to know before maintenance can be performed.
In addition, knowing how long a component, such as a hose, has been in service, what it is made of and what it will take to replace it also allows technicians to diagnose and solve system problems more effectively (Figure 1).
If that information is not readily available, more effort and time will be required to examine system schematics to find the answers to these questions (Figure 2).
Figure 2. Without effective tagging, it may require more time to determine whether a hose needs to be serviced, increasing downtime and reducing profit potential.Swagelok Company
Shutting down a system for examination means unnecessary downtime and reduced profit potential. So how can plant managers eliminate the need for these problematic shutdowns?
Fortunately, preventing such service interruptions can easily be done by tagging all parts of your fluid system – even the potentially less important ones. Finding the right component supplier who can provide both the tags themselves and guidance on what information should be included on them is important.
By tagging the hoses, valves and other components of your fluid system, you can make effective maintenance and improved system uptime reachable goals at your plant.
Getting Ahead of Routine Maintenance
While most plant operators tag the mission-critical fluid system components such as pumps, they do not always tag every item (Figure 3).
Figure 3. While most plant operators tag the mission-critical fluid system components such as pumps, they do not always tag every item – and they should.Swagelok Company
Clearly printed hose and valve tags can reduce the amount of confusion for the maintenance team, leading to faster identification of potential problems and allowing for proactive, rather than reactive, maintenance.
Before tags can be added, however, it is important to do a full plant audit to identify what components make up the system. An audit can provide you with information about the type of hose or valve, part number, process fluid, pressure and temperature ratings, vendor name and contact information. The audit also allows technicians to plan to service components before major problems occur.
Putting this information on tags will allow maintenance technicians to make more informed decisions about what action is necessary or whether any action needs to be taken at all. If there are no tags, then technicians may be left to their own intuitions about whether a component is in proper working order.
In situations in which there are time-specific maintenance requirements for components such as hoses, intuition will not be good enough. Allowing technicians to replace components before they fail saves the plant time and money.
Plus, adding informational tags to the components will allow them to make quicker decisions about whether a part needs to be replaced.
Furthermore, effective tagging can alert technicians to site-specific issues or faults that may not occur regularly in the system. Tags can be used to record these issues so that technicians can quickly see whether the system has had particular issues in the past.
Fully understanding where issues have occurred can provide some insights into what may happen in the future and give technicians the ability to service system components in a timely manner.
Providing the Proper Information Improves Efficiency
Though tags are cost-effective and improve efficiency by providing technicians with important maintenance information at the source, they are only as good as the information included on them.
Minimally, tags should contain the part number, date of manufacture and the trace identification number, which ties the product back to the original order (Figure 4).
Figure 4. Though tags are cost-effective and improve efficiency by providing technicians with the important maintenance information at the source, they are only as good as the information provided. Minimally, tags should contain the part number, date of manufacture, and the trace identification number, which ties the product back to the original order.Swagelok Company
If space is available, it is often useful to include system media, operating pressure and temperature as well.
When it comes to procuring the proper tags, it is beneficial to work with the right supplier. Not only do some manufacturers include all of the proper information as standard on each component, but they will also frequently offer different tag styles to customize for your particular application, down to the specific industry.
Tag styles often range from simple metal tags to color-coded tags. They can be supplied wrapped around a hose near the end connections. You can also color-code handles, tubes and pipes throughout your plant so workers can immediately identify what types of fluids or gases are flowing through them, reducing the possibility of miscalculations.
When it comes to tags, type and size matter. Typically, tags allow for approximately five lines of text with roughly 25 characters allowed per line, including spaces.
In addition, tags can be coated in silicone to minimize entrapment areas and make them easier to clean. The more information you include on the tag, the more quickly and effectively technicians will be able to service their systems.
Tags Tell the Tale
Providing the proper information on the tags for your systems clearly facilitates easier maintenance and can prevent unnecessary downtime and lost profit potential. Shutdowns become shorter and your plant can operate at full capacity more often.
Work with your component supplier to develop a more effective tagging system in your facility. It can expedite maintenance, improve system safety and minimize downtime – while improving your plant’s overall performance (Figure 5).
Figure 5. Work with your component supplier to develop a more effective tagging system in your facility. It can expedite maintenance, improve system safety, and minimize downtime – plus improve your plant’s overall performance.Swagelok Company
---
Brian Aplin is Field Engineering Supervisor – Americas for Swagelok Company.