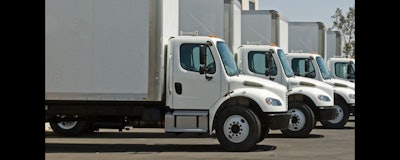
If you run any type of business, your fleet is often the most important thing you own. Unfortunately, trucks, trailers, and other items that make up your fleet are all susceptible to corrosion caused by rain, and even snow and salt if you live in an area that experiences wintry weather conditions. Why is it so important for you to prevent corrosion during your regular fleet maintenance, and what can you do to ensure you are protecting your fleet from corrosion?
What Causes Corrosion?
If you work outdoors, corrosion is always a risk — but what causes corrosion? It involves a lengthy chemical formula, but to break it down into simpler terms:
- First, water bonds with carbon dioxide in the air, forming weak carbonic acid.
- Second, this carbonic acid slowly dissolves metal like iron, causing the water to separate into hydrogen and oxygen in the process.
- The free oxygen molecules bond with the dissolved iron molecules, creating iron oxide, or, as it’s better known — rust.
This process is exacerbated by the addition of other corrosive materials, like salt, which often coats icy roads.
What Vehicles Are Vulnerable To Corrosion?
What sorts of vehicles are vulnerable to corrosion? In general, any fleet components that are kept or used outdoors can become susceptible to corrosion — but some are more vulnerable than others.
Fleet vehicles are usually painted and coated with a clear coat which helps to prevent corrosion as long as the paint is maintained. The undercarriage of these vehicles isn’t coated, though, and can be susceptible to corrosion.
Trailers, heavy equipment and other things that are not painted or coated can also corrode if they’re not maintained correctly.
The effects of corrosion can vary depending on what parts are allowed to corrode, and where the corrosion lies. If allowed to continue unchecked, it can cause parts to fail and potentially make it difficult or even impossible to run your business until the corroded parts have been repaired or replaced.
In light of this, what can you do to protect your fleet from corrosion?
Wash And Dry Your Fleet Regularly
This might sound counterintuitive, but regularly washing your fleet can help prevent corrosion, especially if you live in an area where salted roads are common.
For trucks and other painted vehicles, a good wax coating or ceramic clear coat can also help prevent corrosion. If washing your fleet regularly isn’t an option, consider investing in an undercoating treatment for your fleet — it works much like a clear coat for the undercarriage of your fleet vehicles.
Invest In Corrosion-Resistant Materials
Iron and steel are common building materials for things like trailers and fleet vehicles — but they are also the most susceptible to corrosion. Upgrading your fleet trailers or other equipment to be made of corrosion-resistant materials can help to reduce the impact of corrosion on your fleet. Look for materials like:
- Galvanized steel — This steel is coated with galvanizing zinc to prevent corrosion and is generally considered one of the best anti-corrosion materials. The only time corrosion becomes a problem for galvanized steel is when it is being welded — the galvanizing zinc prevents a good weld, so it has to be removed on the weld points.
- Aluminum — Aluminum is much lighter than steel and is highly resistant to corrosion. It makes a good material for things like trailers.
- Fiberglass — While not as heavy-duty as steel or aluminum, fiberglass is nearly impervious to the traditional problems caused by corrosion.
While these materials might not work for all applications, you should consider investing in corrosion-resistant materials, especially if you work in an area that’s prone to rain or snow.
Coat Existing Equipment With Anti-Corrosion Coatings
If replacing at-risk equipment with corrosion resistant materials isn’t an option, either because of functionality or because of budget restraints, coat any at-risk materials with an anti-corrosion paint or material. The options available to you will vary depending on the type of equipment, but could include:
- Grease — While not a permanent solution, grease can be used in moving parts to facilitate movement and prevent corrosion.
- Paint — A variety of different paints can help prevent corrosion. The paint on your fleet vehicles is a good example of this application.
- Epoxy coatings — These one- or two-part coatings can be used on a variety of applications. They can be made of plastics, resins or even polymer plastics.
- Zinc — Similar to the zinc used to galvanize steel, it can make a coating for existing equipment.
- Ceramic — While not the best option for high-impact applications, ceramic epoxy coatings can help prevent corrosion.
Corrosion prevention is essential to run a successful fleet. Allowing corrosion to continue unchecked could potentially cripple your fleet, costing hundreds or thousands of dollars to repair, not to mention the money lost while your fleet is out of commission. Take time to maintain your fleet and it will serve you well — neglect it and it will fail you.
Preventing corrosion doesn’t have to be expensive or time-consuming. Being aware of the threat corrosion presents to your fleet helps — it’s up to you to keep your fleet running by reducing the risk as much as you can. Be aware, take steps to prevent corrosion and you’re well on your way to running a smooth and functioning fleet.
Megan Ray Nichols is a freelance science writer.