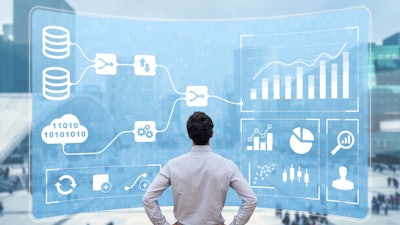
The manufacturing industry utilizes large, complex production systems which generate a huge amount of data. At the same time, the industry is highly competitive and manufacturers have to gather and utilize market data to get a good picture of future trends and remain competitive. Business analytics are the technologies and practices used on this data to gain insights into the production and management of the plant.
Here are three ways business analytics can help manufacturers in facing the modern challenges of the industry.
1. Boosting Operational Efficiency
Running your organization at the highest efficiency possible is a necessity to remain competitive in the industry. As the marketplace becomes more dynamic, manufacturers have to find ways to match the demand with production and supply chain capabilities. One way manufacturers can boost operational efficiency is by responding to these new market trends and economic challenges.
Business analytics provides insights into production as well as business operations. The comparison of current operations with historical trends, peers, and the entire market can highlight the areas needing work. This is done by creating dashboards and KPIs that improve the visibility of the operations. Based on such dashboards, management can get a fair picture of the operational efficiency of the business to make quick, informed decisions.
The information provided by business analytics is used for sales and operations planning (S&OP). A suitable S&OP process helps the business link its everyday operations with its goals and philosophy. It helps model the effects of meeting demand on supply chain management and finances. At a higher level, an S&OP turns into a tool for senior executives to manage business and customer demand while finding the most economical way to do so, which boosts operational efficiency.
2. Improve Maintenance and Quality
One of the major reasons behind unplanned downtime in the manufacturing industry is the failure of critical assets. Organizations that haven’t upgraded their production systems with Industry 4.0 technologies still lack visibility and predictability when it comes to their assets’ health and efficiency due to a lack of data. This becomes an obstacle in getting the most out of the assets and improving the efficiency of the manufacturing processes.
Predictive maintenance analytics is a maintenance scheduling method that utilizes data collected from assets across a production system to predict when an asset will be due for maintenance. This requires an IIoT infrastructure made of various sensors transmitting asset data in real-time. The EAM software has a PdM algorithm that analyzes the real-time, as well as historical data, to predict when an asset will next require maintenance. This allows for maintenance even before the quality of products is affected by wear and tear, while also avoiding too much maintenance involved with the preventive method.
A significant advantage of PdM is that the plant can rely on data for maintenance scheduling instead of guesswork. This creates a reliable schedule that can help achieve near-zero unplanned downtime to expand manufacturing margins, which is the dream of all plant managers. PdM is quickly becoming the go-to solution for manufacturers dealing with unplanned downtime problems because it gives the results and doesn’t require significant capital investment for a smart factory.
3. Optimize Inventory
Inventory includes assets like raw materials, machines, goods in production, and produced goods. An optimum inventory is a fine line between having too much stock, which would drive up storage costs, and a shortage of stocks which would delay deliveries. This is why manufacturers require an optimized inventory to ensure on-time and low-cost production.
Inventory management requires involvement from production and the business side of manufacturing as it deals with demand forecasting, delivery, and the bottom line. This means the optimum inventory has to balance costs and also have enough stock to keep producing and delivering on time. Data analytics plays a vital role in achieving this for any modern business.
With data analytics, large inventories can be made more transparent and visible to easily obtain key information about inventory. With inventory transparency, management can consider historic trends and demand forecasts to align procurement and production. An optimized inventory improves customer delivery experience by shortening the waiting periods and reducing storage costs, which help make the business competitive.
Business analytics is a necessity for any modern business and manufacturers are no exception. Apart from the ones mentioned, business analytics also strengthens day-to-day management including workforce management and planning. It is surprising that even today a large amount of data generated by production facilities goes unanalyzed.
Manufacturers cannot take the data for granted. Creating the infrastructure for data collection and analysis is the first step toward business analytics. For this, management has to take the initiative, create the infrastructure, and ensure its proper utilization to weather modern challenges while also getting the best returns on investment.
Bryan Christiansen is the founder and CEO of Limble CMMS.