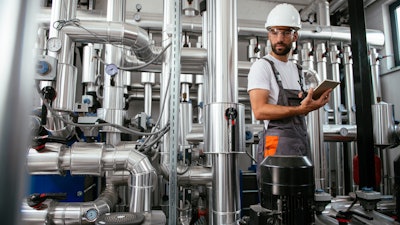
A leaking pump is a common and frustrating problem that maintenance engineers face. When pumps leak, it causes unnecessary downtime and costly repairs or replacements as operators work to fix the problem. The most common cause of pump downtime is seal failure. While pump seals are meant to keep pumps from leaking, several design and operational errors often lead to their breakdown or premature failure:
- Excessive forces.
- Harsh environments.
- Operational misuse.
- Poor design choice.
With proper seal design, correct pump usage, and regular maintenance and upkeep, maintenance teams and manufacturing engineers can reduce the seal failures, keeping their systems up and profitable. This article explains the costs of seal failures, why they occur, and how to prevent them.
The Consequences of Pump Seal Failures
A small leak caused by a pump seal failure can quickly turn into a big problem from all the downtime and repair costs. As this occurs again and again, those costs will often exceed the initial cost of the pump itself. Pump seal failures can also lead to regulatory compliance issues if things get bad enough, causing companies to incur hefty fines from regulatory agencies.
There are also the day-to-day environmental hazards that seal failures create. When product leaks onto the floor, it can cause workers to slip and injure themselves. Because leaks cause product to spill out of the pump, they can also create a path for contaminants to enter the process stream. This is a major hazard for applications in food manufacturing, where strict sanitary conditions must be always met.
How Do Pump Seals Fail?
There is not a single reason why pump seal failures occur. A number of different issues can cause leaks, many of which are avoidable when you specify the right pump design and use the pump properly. Here are the seven main reasons why seals might be failing:
- Running the Pump Dry. Most pump seals require some type of fluid to lubricate the materials around the shaft during operation. If you run the pump dry and there are no fluids available for lubrication, it will cause excess heat and friction. Mechanical seals cannot handle running a pump dry and will break down rather quickly if no product is there to cool the seal.
- Overly Gritty or Abrasive Product. Gritty or abrasive product will wear down a seal if the seal design and material were not chosen appropriately. While seals inevitably wear down over time due to contact friction between the shaft and the seal, extra abrasion from a product or process fluid will cause the seal to wear down much faster and significantly reduce seal life.
- Chemical or Physical Incompatibilities. Severe chemical or physical loading can reduce the life of a pump seal and potentially lead to rapid degeneration and malfunction. The harsher the chemicals or forces acting upon the pump, the faster a seal will fail.
Excessive Shock and Vibration
If a pump experiences too much shock and vibration, it can cause significant axial and radial play of the shaft. This will then lead to misalignment and a greater rate of pump leakage, reducing a seal’s lifetime.
- Operator Error. If a pump is installed incorrectly, the shaft may become misaligned, causing pump seal failure similar to the result of excessive vibration. Other operator errors include over-tightening the fasteners, leaving contaminants or residue on the seal face, and incorrectly mounting the seals.
- Harsh Environments. Uncontrolled heat or drastic temperature shifts can wear down a seal. Having to deal with significant pressure drops or spikes or the regular caustic washdowns can also increase the wearing process.
Any changes in operations parameters can theoretically lead to increased pump seal wear if not accounted for. Adjusting seal chamber pressure, speed, shaft seal dimensions, the pumped medium, and the temperature around the pump can all result in damage to the seal.
Incorrect Pump Design or Seal Choice
If a pump is not designed correctly or engineers choose the wrong seal material, seal failure may be imminent. This a major cause of pump seal failure, though it is also one of the most avoidable issues if adequate time is spent upfront to determine the appropriate pump and seal combination.
While pump seal failures are a common problem, there are many steps that maintenance staff can take to eliminate the common risk factors presented above. Here are the top ways to avoid pump seal failure:
- Specify the Right Style of Pump. Proper pump selection starts with sizing the pump correctly. This will help to prevent misalignment issues, as well as ensure that the pump is equipped to handle the pressures and other forces that it will face during operation. Buying teams will also want to choose the right type of seal for the application at hand. The goal is to choose a seal that can meet all operational requirements. Specifiers should consult with pump manufacturers to ensure that they select the right pump design. Pump manufacturers have experience across many different applications, and they can deliver tailored advice to your specific task. As an example, if you need to take the pump apart frequently for cleaning, hard face seals will be too brittle of an option.
- Avoid Installation Errors. Once the buying team has selected the right pump and seal combination, seals must be installed correctly in order to ensure proper performance. Use the right tools and equipment to avoid damaging the pump. Operators must also make sure to keep everything in alignment.
- Use the Pump Correctly. The day-to-day use of a pump will be one of the biggest determinants if a seal will last its lifetime or fail early. Operators will want to make sure that they do not run the pump dry. Instead, they should shut down the pump when there is no product running through it. If the pump is shaking and vibrating, this is a sign that seals are getting wearing and leakage is imminent.
- Perform Maintenance Regularly. Given labor shortages and cost pressures, it is commonplace for certain industries and applications to neglect pump maintenance. To ensure pump seals are not consistently failing, maintenance teams should fix any issues sooner than later, then address the problem when it is a simple repair versus having to shut everything down and buy new equipment.
For example, many production applications often run with a shaft seal leak. While this can be overlooked at first, that small leak can compromise the O-ring shaft seal, which penetrates other areas of the product. Now, instead of a somewhat simple fix, manufacturers will need to replace entire sets of equipment, shutting down production while they do so. Manager should remember, they are not just losing capital from the cost of the replacement, but also from all the productivity they lose when not making product.
Because pump maintenance can vary greatly based on specific operations, buying teams will want to talk with the pump manufacturer to figure out the parameters of the application and determine a maintenance schedule. Their pump experts will ask all the right questions so that managers can reduce the risk of seal failure to keep pumps and operations running smoothly.
With proper seal design, correct pump usage, and regular maintenance, manufacturers can minimize the chance of a failure, keep their systems operating and profitable, and prevent unnecessary and costly downtime.
Calle Danielsson is a sales engineer with Unibloc Pump, a manufacturer focused on sanitary pumps for food and beverage, pharmaceutical, bakery and confection, meat and poultry, brewery and transportation environments. He specializes in helping customers select the ideal pump for an application.