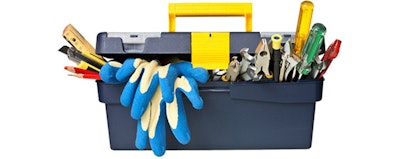
Minor to major changes in the maintenance department have the potential to improve operations throughout an organization. When assets are maintained according to manufacturer’s instructions and historical performance, there is typically less downtime and more productivity among staff. This means the financial incentives for managers to improve processes are usually on target. Predictive maintenance, as part of cloud CMMS to perform repairs and inspections, is the gold standard of facility upkeep and a worthwhile goal for teams today. But what happens when these programs need a refresh?
Staying on the Right Track
When a program isn’t producing the desired results, it’s best to not let it go on one day longer than it has to. To this end, Plant Services provided valuable advice for companies that have tried predictive maintenance (PdM) in the past but are having trouble getting it right. Making quick and decisive changes based on an accurate diagnosis of current problems can provide a much-needed reboot and deliver the kind of value teams were promised when they began moving towards a PdM strategy originally.
The first step in starting fresh and getting results from a strategy is determining why it hasn’t improved performance so far. The source explained that this often has to do with integration failures or a disconnect between personnel. The technology behind predictive maintenance – CMMS, asset condition monitoring systems, and related sensors – have become more reliable in recent years, delivering valid results when supported properly. Without strong user adoption, however, even the most heavily automated system can fail.
So, what’s the recipe for a strong PdM strategy? Wonderful Co. Director of Reliability Bob Kazar told Plant Services that leaders need to get behind programs from the start. When management doesn’t fully support initiatives meant to boost maintenance, those plans will have trouble gaining traction. Kazar also explained that leaders need to keep effective teams in place. He described one situation where a team was cut down to a single employee. As the worker was unable to keep up with the demands, they fell behind and the company’s predictive capabilities weakened.
Getting a PdM system to excel is a matter of following through on initial excitement and guiding every step, from technical implementation to employee training to everyday operations, all with the right solutions in place. Marshall Institute Oil and Gas Services President Tracy Strawn explained to the magazine that companies begin their journey to PdM in good faith and with the best intentions, then let things slip along the way. Many cases – more than half, in Strawn’s experience – end up this way.
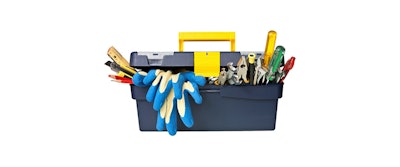
Staying on Top of Maintenance
A modern CMMS and its accompanying mobile app, particularly solutions designed for a simple and effective user experience, is the nexus of any good upkeep strategy. Predictive operations would simply cease to work without such a system in place. Leaders who rely on these solutions to ensure their departments are functioning up to high standards gain the greatest benefits. The use of a CMMS to generate accurate and timely reports can help leaders ease into predictive operations. Through access to the right data, managers can, over time, perfect the maintenance strategy for each asset and piece of equipment.
When facility and maintenance managers remain involved and supportive of PdM strategies, these plans can deliver ROI that outstrips other kinds of upkeep. Reducing and avoiding unplanned downtime wherever possible is the name of the game in efficient operations, and using big data to keep wear and tear at bay is a way to make this happen.
This blog was originally posted on Smartware's Bigfoot CMMS blog here.