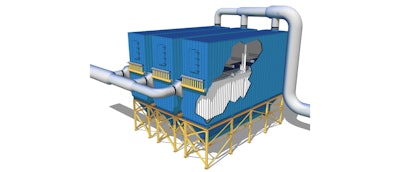
How do large and waste-heavy industries comply with environmental regulations and still stay in the black? The solutions to this complex technical challenge begin with an understanding of where each type of waste stream must go and how it can be profitably re-used if possible. At most industrial sites, waste streams include wastewater, solid wastes and air emissions.
A new proposed state-of-the-art facility that would utilize large rotary kilns to manufacture a ceramic product needed to be able to meet regulatory requirements to become a reality. The design team at SSOE — a global engineering, procurement and construction management firm — addressed all three of the problematic waste streams. In doing so, it eliminated industrial wastewater discharges and reduced the production and disposal of solid waste during the manufacturing process. But the biggest win was in its solution for air emissions, without which the proposed project could not have moved forward.
Air Emissions Abatement
The production lines in this plant emit sulfur dioxide (SO2), nitrogen oxide (NO2), acid gases and particulate matter (dust or PM). Technical issues with the clay material used to make the ceramic product, until recently, have prevented the reduction of these emissions using traditional emissions control technology in this industry.
For the new facility, the manufacturer needed permits for four production lines, each of which had to satisfy strict air emission maximums. Traditional technology would entail three separate emission control devices, one for each type of emission. Traditionally, the air stream would have to be cooled for the SO2 step and re-heated with typically a natural gas boiler before the NO2 control device due to reaction temperature requirements.
The SSOE team looked for out-of-the-box solutions and discovered a Catalytic Baghouse System, a technology used for emission abatement from coal-fired boilers and incinerators. This technology already had 400 installations in other parts of the world and allows for the treatment of dust, NO2, SO2 and acid gases in one unit without reheating the process gases. It was significantly less expensive than the traditional solution. With this technology, the air emitted at the end of the process was so clean that the designers installed a heat recovery unit to preheat another part of the process. This solution saved $1.65 million/year (in 2011 dollars) by preheating another part of the process. It saved another $2.035 million by eliminating the heat-up step required by traditional technology. The net savings was $3.685 million/year, not to mention the elimination of fines that competing firms were still being forced to remit to the EPA for not meeting emissions standards.
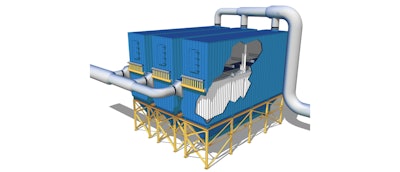
The SSOE team did not have to address controlling greenhouse gases with any control or abatement technology. Instead, the team reduced greenhouse gases emissions by reducing the amount of fuel that was needed to preheat another part of the process, eliminating the reheat step of traditional abatement technology.
Developing the solution involved evaluating the technical and economic feasibility of the technology by a number of disciplines. Through a collaboration of mechanical, process and structural engineers as well as various vendors supplying components of this technology, SSOE determined how to transfer the technology to a different industry in a way that was — after considerable explanation — accepted by the owner and EPA.
Eliminating Industrial Waste Water Discharges
At the new ceramic product plant the design and engineering team collaborated with the operations team to develop a water conservation plan as part of the process of applying for a water withdrawal permit. Without an acceptable plan, no water permits would be issued.
The first phase was to build a well on the site to provide process water for manufacturing. The cost of this (non-potable) water was the cost of the well. Potable water, needed for fire and life safety purposes, would be purchased from the city.
In the second phase the team designed a recycling system that could re-use more than 99 percent of the waste water produced by the manufacturing lines. All the industrial processes that use water were equipped with water lines that return and dispense recycled water. In addition, storm water — collected in catchments adjacent to chemical storage tanks — flows into the gray water system for use in the manufacturing process.
The re-use of waste water greatly reduces the discharge fees and discharge requirements that would otherwise be required by the local city waste water treatment plant. The water conservation plan monitors withdrawal rates from the well, which requires permits. Re-using water also reduces the draw on the local aquifer and therefore eases the impact on neighboring properties — which is appreciated especially when the surrounding region is experiencing a severe drought, as it is today.
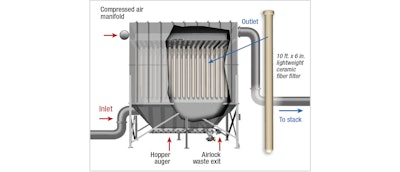
The final phase of the water conservation plan calls for inspections for water leaks in the system and repairs. Some process water is driven into the air from the kilns, and less than one percent of the wastewater must be discarded after being used to clean out the gray water system and a truck tire washing area. Such cleaning tasks normally occur only once a year.
Simply stated, the water conservation plan eliminates waste water discharges. In doing this the plan also eliminates the complex process of applying for permits to discharge waste water. Finally, it frees the operational phase from responsibilities to perform ongoing waste water sampling, analysis and reporting.
Reducing Solid Waste
The manufacturing process in this case study produces several solid waste streams that can be recycled. The production lines collect the dust produced as the raw materials are being processed. The manufacturing line also collects wastes from other raw materials and recycles them back into the production line. Reducing solid waste not only reduces the operating costs connected to disposing of solid waste, it also reduces the liability issues related to ground contamination.
After the dust has been reprocessed a certain number of times, it can no longer be recycled into the product that is manufactured at the local facility. However, it can be exported to cement plants, which can incorporate the dust as a raw material for their products. The plant’s sales department is currently working to identify other potential customers. Recycling spent dust is estimated to cut disposal costs by $40,000 per year, a savings that may eventually increase to $60,000 per year in solid waste disposal fees for other recycled materials. At the same facility another solid waste stream undergoes dewatering. The water from this process is recycled into the gray water system. Although the resulting material may have to be discarded, the sales group is also investigating the possibility of using it as a component in mine reclamation.
Until recently it has been a struggle for large manufacturing plants to make the transition to environmentally friendly territory. Today, through the close collaboration of design, engineering and operational groups, such plants can operate well within permit limits by conserving significant amounts of water, reducing the production of solid waste and controlling emissions of other pollutants.
Anna Koperczak is a senior environmental specialist at SSOE Group, a global engineering, procurement, and construction management (EPCM) firm. She can be reached in SSOE’s Toledo, OH office at 419.255.3830 or at [email protected]