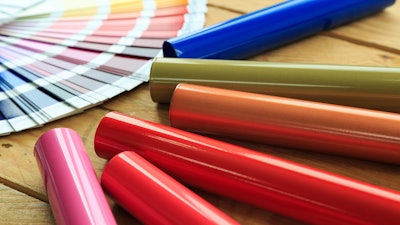
When a global producer of industrial coating resins and additives located in Southeast U.S. sought to upgrade its aging Distributed Control System (DCS), minimizing production disruption was critical.
A DCS system is a hub of a processor’s operations monitoring key variables such as flow, applied temperatures, pressure, level and material conveying/handling.
The challenge was that replacing the manufacturer’s decades-old DCS had to be accomplished quickly while accurately maintaining the specifications of its final resin products. Failure do so would equate with lost revenue due to downtime or rejected product.
Moreover, much of the documentation on the process was unavailable and the tolerances were tight enough that there was a risk of product being produced out of specification.
This scenario is not uncommon. As a DCS ages, there can be increased risks to a process manufacturer. An old or obsolete system may no longer be supported by the original supplier, spare parts may no longer be readily available and system performance issues may begin to appear.
With some systems now decades old, users often know they need to upgrade but changing over without affecting production can seem daunting.
Complicating matters, this particular manufacturing plant, one of five plants at the location, operates on an essentially 24 hour basis, 365 days a year. The plant produces industrial coating resins and additives for architectural, protective, automotive and special purpose coatings and inks.
The Challenge
Although the plant’s existing DCS was functional, replacement parts and service were not readily available. The proprietary DCS had outlived its useful life and there was risk involved in running on an obsolete system.
If the automation system equipment were to fail, there was a possibility the plant would not be able to operate for an extended time.
“For a plant of any scale running at, or near, capacity, taking down processing lines for any amount of time can be extremely expensive in terms of lost production and business impact. This plant was running continually day and night, all year long so any production downtime means the company is losing money,” said Chris Gepfert, who was involved with the upgrade project as regional sales manager at Owings Mills, Maryland based NovaTech Automation, a leading provider of distributed control systems and solutions.
Proactively upgrading the DCS, in contrast, would provide much greater reliability, process control and automation as well as additional capabilities. However, the required system migration, data transfer and integration with legacy equipment would need to be handled expertly to minimize any downtime and avoid potential quality issues.
When manufacturers utilize batch reactors, following the recipe from batch-to-batch and plant-to-plant is critical to manufacture high value-added materials reliably and cost-effectively to spec.NovaTech Automation
“The biggest challenge was replacing the existing DCS with a modern system that would produce industrial coating resins and additives to the same specifications with equal or higher quality and minimal disruption,” said Gepfert.
“If any powder were out of specification, the end user could reject it,” said Gepfert. “The specification could be a color range that would be compromised if the product were too dark, cloudy, opaque or lacked any necessary functional properties.”
Functionally, NovaTech had to program the new DCS based on how the prior system was programmed. Some re-engineering and redesign of the new system were necessary, given that process documentation was often unavailable.
At the same time, the new system would include various upgrades to improve automation and control.
The Solution
The coating manufacturer’s solution for the plant involved utilizing a flexible, reliable, modern DCS that could be quickly integrated with existing production.
When manufacturers utilize batch reactors, following the recipe from batch-to-batch and plant-to-plant is critical to manufacture high value-added materials reliably and cost-effectively to spec.
This typically involves charging the reactor, manipulating operating conditions to meet processing criteria and shutting down and emptying the reactor.
To control their reactor processes, the plant now uses the D/3 DCS from NovaTech.
In addition, NovaTech provided new applications programming, High-Performance Human-Machine Interface graphics; sophisticated S88 batch management software; and an updated real-time data historian application; and migrated the I/O from an older version to a new, modern I/O platform, along with providing startup and ongoing onsite support.
According to Gepfert, the key was implementing the full set of processes in a very robust, reliable, flexible system. It also needed to be highly automated so the plant can effectively run on its own with minimal operator interaction.
The NovaTech D/3 operator interface displays real-time process information and makes it easy for the operator to control the process, enter information and interact with sequence programs.
With this approach, the operator can modify recipe parameters, recipe procedures, production schedule, batch start rules, equipment utilization or scale batch amount at any point during recipe development and execution.
Recipe values are automatically entered into the system and all the operator needs to do is click on the reactor to use and which vessel to pull from. This is safer, more intuitive and speeds the process because the operator selects all the equipment to be used before starting the procedure.
The information can be viewed using common web browsers to display data from multiple plant sites from anywhere in the world, which facilitates coordinating production with other plants in the corporate network.
The transition to the new DCS was quick and successful and the modern system is much more reliable and efficient than the previous one.
Unlike the older proprietary DCS, now replacement parts and service are readily available, which helps to minimize potential downtime. Additionally, the plant’s technicians can easily change and program the new DCS utilizing Windows based servers, which helps to accommodate any modifications needed over time.
“After upgrading to the D/3 DCS, the plant has expanded its overall throughput by up to 50% and production efficiency has increased by 20% to 30%,” said Gepfert. “So, the plant can process product much faster today.”
The new DCS also provides greater accuracy than the older system. “The previous system’s tolerances were broader and less accurate. The new DCS provides significantly tighter tolerances and better-quality control. This helps to ensure that all product specifications are consistently met and essentially prevents the waste of producing off-spec product,” said Gepfert.
In addition, the plant’s process control and data management are significantly improved. The DCS provides more accessible and meaningful data than the previous system.
Another consideration for the coating manufacturer was the need to integrate the plant’s new DCS system with the existing enterprise systems.
Plant management sought improved data capture and the conversion of that data into useful knowledge presented in desktop key performance indicator (KPI) dashboards that can be utilized at the manufacturing execution level and/or the enterprise ERP level, according to Gepfert. He noted that the previous DCS provided much more limited, isolated information without the context needed to make important decisions.
“The new DCS system provides extensive data, analytics and historical records with overview screens, KPIs and trends displayed with graphics. With data never previously available, plant operators can not only manage but also optimize production,” said Gepfert.
The plant’s changeover to the new DCS system was achieved quickly and on budget without the excessive overcharges that sometimes occur with high-priority projects.