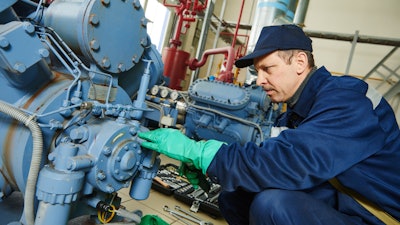
The Internet of Things (IoT) and associated technologies such as sensors have disrupted the manufacturing industry. Add to that the rapidly evolving ability to consolidate, connect, and distribute real-time data across the enterprise, and we are starting to look differently at how we can best manage the assets that drive our business and profitability.
These developments have also inspired the evolution of the Maintenance Maturity Model, the framework for how asset-intensive industries can achieve optimum maintenance efficiency. In manufacturing, achieving more sophisticated levels of asset management starts with a more intelligent and data-driven understanding of potential equipment failure, as well as carefully laid plans for prediction and prevention.
The Maintenance Maturity Model includes five levels of maintenance maturity:
- Reactive. This means run to failure or repairing the asset after it malfunctions. Prior to technology innovation, it was (and still is) a common practice.
- Preventive. Attempts to prevent failure by maintaining machines at pre-scheduled time intervals are the next step in maintenance maturity. However, it is inefficient, costly, and creates unnecessary downtime.
- Condition-based. This stage provides alerts around a single point of failure, but does not reflect the health of assets as a whole.
- Predictive. Predicting asset failure has become easier with the advent of algorithms, and technology such as machine learning.
- Prescriptive. This level not only identifies issues before they happen, but lays out the processes and people necessary to avoid asset malfunction.
Achieving prescriptive maintenance is the goal, and for good reason. Moving from preventive to predictive or prescriptive maintenance has been shown to save 50 percent in maintenance labor and MRO materials costs. It also sets the stage for a successful, long-term enterprise asset management (EAM) strategy that helps manufacturers find new, innovative ways to compete in a very competitive, budget-conscious, and demanding marketplace.
iStock
Just getting started
While the industry recognizes the importance of achieving greater levels of EAM sophistication, a CapGemini report states that in the manufacturing industry, only 12 percent of companies are leveraging the potential of digital technologies. Yet these technologies are the catalysts of opportunity to achieve predictive and prescriptive asset maintenance.
The key to a successful, long-term EAM strategy that helps manufacturers remain competitive is a modern EAM system that not only collects data, but provides smart analytics to ensure:
- Reliability in terms of product quality and delivery
- Streamlined processes and efficiencies across inspections and maintenance scheduling, parts and materials tracking, and supply and parts use
- More predictable cash flow, based on analysis of asset risk and condition
- Demand forecasting based on data-driven, “what if” scenarios
- Accurate prioritization of major capital investments
- Regulatory and code compliance with ADA, OSHA, EPA and other safety regulations
Not all assets are created equal
While it’s true that the industry has more accurate and timely asset data than at any other time in history, it would be easy to let these rapidly growing volumes of information overwhelm us. That’s why I always offer the advice to look at each asset individually. In other words, while the Maintenance Maturity Model provides aspirational steps toward a utopian EAM culture, moving up the model is not an all-or-nothing endeavor.
Instead, businesses can expect to move through and around the model, depending on asset priority and strategic direction. It starts with looking at the most mission-critical assets, from the manufacturing equipment, to the product transportation, to the energy and power source that keeps the facility running.
The Maintenance Maturity Model is an important tool in helping businesses look for ways to create efficiencies, save costs, and ensure a constant and predictable stream of product to the marketplace. Yet it only provides a roadmap. True change starts with a mindset and culture that looks at maintenance and management holistically. Moving assets up the model is also made easier by implementing industry-specific EAM software and systems that capitalize on the smart digital innovations we experience and use in all other aspects of our lives.
Kevin Price is technical product evangelist & product strategist at Infor.