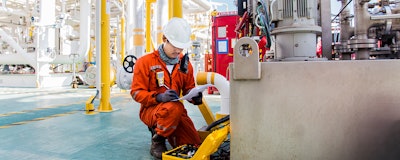
When driving a car uphill, the driver acts as a controller. They adjust the power to the motor based on the change of speed, pushing harder on the gas pedal to maintain constant speed. Servo drives act in the same way.
What is a Servo Drive?
A servo drive is an electronic amplifier used to power electric servomechanisms. A servomechanism is any automated system that uses error-sensing negative feedback to correct the action of the mechanism, a CNC tool, for example. It receives feedback on discrepancies from the desired speed or position the tool should be working to and reacts accordingly.
The servo drive monitors the feedback signal from the servomechanism and continually adjusts for deviation from expected behavior. The servo drive receives a command signal from an encoder, amplifies the signal based on this command, and transmits electric current to a servo motor that is proportional to the need.
For example, if the drive receives signal from an encoder that’s speed has decreased, it will transmit more electric current and turn the motor faster to counteract this.
When the shaft of the motor is at the desired position, power supplied to the motor is stopped. If the motor is near the desired position, it will turn slowly and if it is far from the desired position, it will turn quickly. Clever stuff, right? This is called proportional control. It means the motor will only run as hard as necessary, making it an energy efficient piece of kit.
Some servo motors rely on a specific drive model or brand, however, many drives are now universal with a wide range of motors.
What Are Servo Systems Used For?
Servo systems are all around us. In daily life, they are found in camera auto focus systems, printers and automatic doors. In industry, they are used in factory automation, CNC machines and robots. It is these industrial applications that require high levels of control, repetition and precision, meaning servo systems often trump traditional DC or AC motors because of the intelligent motor feedback they provide.
In woodworking, servo systems control woodturning mechanisms, also known as lathes, which are used to shape table legs and drill holes necessary for assembling those products later in the process. If the holes are not in the exact position, it could spell disaster for the entire table construction, and result in waste material.
What Are the Common Causes of Servo Motor Failure?
Bearing failure is a common issue and can lead to a whole host of problems in the servo motor. This failure can be caused by many variables, such as misalignment, contamination or incorrect lubrication. If bearing failure is not detected early, the bearing will continue to deteriorate and cause other components to fail. As a solution, regular vibration analysis can be used to trend bearing condition and prevent catastrophic failure.
Similarly, just like on a car, the brake pads in a servo motor are prone to wear. The rate of wear depends on environmental conditions and how hard the break has had to work in its lifetime. It is better to forecast brake pad replacement ahead of time, and schedule proactive brake pad replacement before problems arise.
Demagnetization of permanent magnets can also occur if a servo motor is overloaded. If the magnets lose strength, the servo motor will not be able to handle large loads. This can be caused if a robot arm is programmed to pick up a load that places a high starting current on the motor. To prevent this, make sure servo motors are designed to handle the loads they are used for.
Replacement Options
Eventually, parts in a servo system will need replacing. This could be the drive, motor or controller. Many brands supply servo drives for industrial automation, such as Allen Bradley, Fanuc and Mitsubishi. However, these companies will not manufacture the same parts forever. As products develop, some lines are inevitably discontinued, making it difficult to replace these internal servo motor components.
In the worst-case scenario, the entire system will require overhauling. However, it doesn’t need to be this costly and drastic. Specialist, obsolete parts suppliers, such as EU Automation, stock many new or reconditioned parts included in industrial servo systems — including those that are no longer manufacturered by the original equipment manufacturer (OEM).
When choosing a reputable supplier, these reconditioned parts will have been cleaned, serviced and upgraded to optimum working order before they are put back on the market.
Just like driving a car uphill requires intelligence to respond to environmental change and maintain speed, so does the operation of factory automation equipment. With benefits in precision, efficiency and repetition, servo systems are hugely important — but their parts won’t last forever.
Make sure you know where your next servo parts are coming from by establishing a relationship with an industrial parts supplier.
Jonathan Wilkins is the marketing director of industrial parts supplier EU Automation.