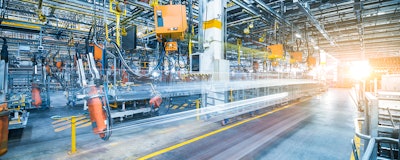
In manufacturing, shutdowns are to be avoided at all cost. Production stoppages mean lost revenue.
However, in any business that is housed in a building and uses equipment, repairs and renovations are necessary at some point.
Scheduling these activities to minimize disruption takes savvy and a decisive balance of multiple factors including preparedness on the part of staff and project teams, as well as the support of leadership.
Minimizing Downtime
Careful planning enables project teams to control shutdowns, rather than being controlled by them.
With careful tracking, teams can specifically isolate the areas affected by repairs and renovations, optimizing manufacturing line functionality through the process. Planning involves tracing every detail of various utilities. Electrically, this careful inventory can include tracing where each bus plug feeds.
In a major renovation, it is ideal to conduct work in parallel wherever possible. Be prepared in advance by installing a new bus — if the space and strata are — available and schedule repair work to minimize downtime. If the new bus is tested and ready, the project team has more flexibility when disconnecting the existing bus plugs/feeder. Check the condition of the existing bus plugs, feeders, and branch circuits to determine where existing connections can be used and where replacements are needed.
If an entirely new installment is best, minimize downtime by running an entirely new feed to make the switch faster. Installing and testing everything well in advance of startup will enable immediate connection and seamless startup.
Similar planning and consideration for mechanical, plumbing and other disciplines is handled on a case-by-case basis and decisively carried out to avoid disruption. The same principles of preparing as much as possible in advance, through savvy planning, ensures a smooth transition for all the disciplines.
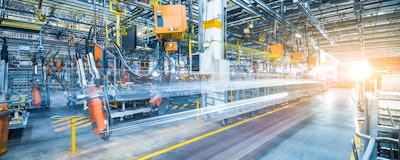
Planning Insights
Planning can be understandably rushed when project leaders and their teams are already working at capacity.
Although project planning is key, there may not be enough time to give it the needed attention. It is ideal to deploy a specific team to gather and sort the appropriate information and data, plan the project, and provide the project leaders with up-to-date, as-recorded drawings based on project objectives. By delegating that responsibility, project leaders benefit from the focus of planning specialists.
Often, project teams start with whatever as-built drawings are available and sometimes no documents at all. The next step is to gather any information possible about the equipment. This can be a challenge when proprietary processes make companies reluctant to share information. They may require confidentiality agreements to release machine nameplate information, so project teams can determine flow rates, amperages, and other operational data. Once all available information has been gathered, teams can lay out a spatial plan based on utility locations. Depending on equipment requirements, teams can lay out parameters to ensure adequate accommodations for all the planned equipment.
There is a substantial amount of paperwork required for this planning step, but once it is completed — thoroughly and correctly — teams are ready to go into the field for verification.
Taking the time to lay out a highly organized — even hourly — workday or workweek plan is critical to optimize field verification. It takes much longer to figure things out when in the field and is often difficult or impossible while a line is up and running, ultimately necessitating a shutdown. Ideally, teams try to coordinate with a planned holiday shutdown so that the work can be completed without unscheduled disruptions. When that is not possible it is paramount to conduct verification as quickly as possible. Project teams are, ultimately, service providers so production comes first, and the diagnostics and repairs completed without impacting production.
Optimizing Time In The Field
To save time, project teams are looking to stakeholders for any data they can provide from previous work that can inform the new project. Often, gathering this information is no simple task. In some cases, there is little to no data and the project team is working from baseline.
The focus of field work is verifying design intent. Teams review drawings, make determinations about accuracy, and then verify those assumptions. A day trip to verify design intent is very different from weeks spent in the field trying to recreate as-built conditions before even starting the new project. Teams must determine early on what the nature of the “field work” line item will be and plan accordingly.
The advent of 3D scans has resulted in companies keeping fewer drawings and other records because as 3D scans are a supplement and tool for verification of existing conditions. However, while 3D scans are a great reference, they are not a viable replacement for drawings and accompanying data. Some scans include information about source and load, but fail to provide nameplate information, plug, fuse, and conductor sizing, and other details that are typically included in the drawings. They also do not account for any of the underground infrastructure that often crops up unexpectedly once the project is underway. Project leaders should view 3D scans as a supplement to their existing materials, rather than a replacement.
Preparing For The Future
Even the most efficient, decisively prepared plans are subject to unexpected developments. Flexibility is key with project planning. Project stakeholders view the design as more of an intent or idea because it can easily change later. For example, a contractor may purchase something different than what was specified in the design, and the team must modify the plan to accommodate that. The project plan must be a living document with built-in flexibility.
In one example project, the team was replacing the evaporator and condenser on top of a walk-in cooler and the plan specified both pieces of equipment be fed from a motor control center (MCC). They fed the evaporator and condenser on separate circuits, 480 Volt, 3-phase, from breaker tubs in the MCC with a single connection point. The contractor ordered a different style fan — an energy-efficient design with four small fans where the number of fans running would adjust based on the cooling demand. The new design meant the fan connection was no longer a single point feed, so it didn’t fit with the design. The team used a calculation of the largest motor times 125 percent + the other three fans to determine maximum load and fed it as a single point, with individual fused switches so that they could use the tap rule from a single breaker.
Even a well-planned, well-designed project can end up with an unexpected change where a field-engineered solution is required. An experienced team quickly determines a solution, keeping construction on schedule and avoiding delays. Flexibility and expertise are key in those situations where even careful planning runs into unforeseen challenges in the field. Comprehensive plans and preparedness reduce the occurrence of such surprises, and that, coupled with the ability to creatively solve them when they do happen, keeps production running through repairs and renovations – when you don’t want to be interrupted.
Corey Zachel, PE, LEED AP BD+C, is a Section Manager and Senior Associate at SSOE Group, a global project delivery firm for architecture, engineering, and construction management. With 18 years of experience, Corey manages the production and checking of electrical construction documents.