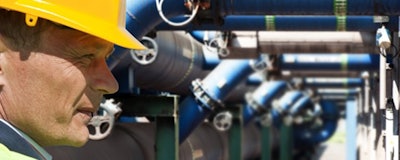
Performing regular maintenance on industrial piping can be the difference between business as usual and a catastrophic, headline-making disaster. However, industrial piping maintenance causes changes in a closed system, which comes with its own, less newsworthy but equally dangerous set of hazards. Improperly maintaining a closed system of industrial pipes can be just as dangerous as a catastrophic failure.
What Is Industrial Piping?
An industrial piping system is a network of pipes used to transfer liquid, gas, or solids with near zero loss of the quality or properties of the material being transferred. The most common materials moved in an industrial piping system are water, fuel, ammonia, and compressed gases such as air, oxygen, and nitrogen. Industrial piping systems are found in oil refineries, chemical production facilities, power plants, and in smaller facilities such as fabrication and machine shops. Industrial piping systems do not include those in commercial buildings or long distance pipelines.
What Is a Closed System?
A closed system is a physical system that does not exchange material with or interact with its surroundings and is not subject to any force whose source is external to the system. In less verbose terms, a closed system is one where you know all the variables and can control them. In terms of industrial piping, this means a closed system is one where you can account for the changes that might happen in pressure, volume, flow direction, and temperature. In general, the integrity of the pipes is another accounted-for variable in this closed system; they are always assumed to be functioning unless proven otherwise.
It is the opening of this closed system that can cause a life-threatening hazard if proper precautions are not taken. The opening of valves, ignition of pumps, or operation of equipment that is not isolated from the rest of the system are examples of significant sources of hazards.
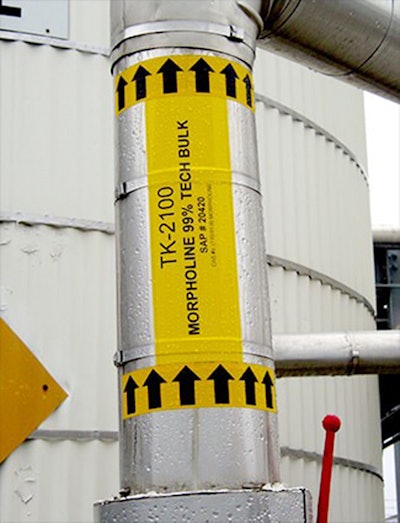
Keeping Workers Safe When Maintaining Industrial Piping Equipment
Neglected industrial piping equipment is, more often than not, responsible for the catastrophes you end up seeing on the news. Maintaining, assessing, and inspecting the equipment is the main way to keep your business out of the headlines, but doing so safely is vital for the sake of your employees. When they shut off a valve, redirect a pipe’s flow, or deactivate a pump, they are injecting a new variable into the closed system. This can cause great harm if the proper precautions are not taken.
The following are examples of actual accidents involving industrial piping systems:
- In 2006, a worker was removing a pipe cap from an eight-inch pipe that was pressurized with 80-pounds of air. The worker was not aware the pipe was pressurized. As it was loosened, the metal pipe cap blew off the end of the pipe, striking and killing the worker.
- On Feb. 29, 2012, four people were using a cutting torch to demolish an out-of-service petroleum pipe. The pipe had not been purged in over a year. It contained vapors that resulted in an explosion and flash fire. All four workers were scalded, burned, and taken to the hospital. Two were released after 24 hours; the other two remained hospitalized for an extended period of time.
- Two workers were operating a sodium turn state purification system. When attempting to pump a Sodium Hydrosulfide solution into a tank, one of the workers accidentally opened the valve to another tank that contained an acidic solution. When the two chemicals mixed, they produced hydrogen sulfide gas. The worker died from exposure to hydrogen sulfide gas.
- In another fatality involving hydrogen sulfide gas, a worker accidentally drained the contents of a knockout drum to an oily water sewer, rather than to a closed system. This produced hydrogen sulfide gas resulting in the fatality. The draining procedure required the use of the closed system, however, the valve to the sewer was not closed and locked out before he started draining the knockout drum.
- Workers were draining refrigerant oil from collection traps on an anhydrous ammonia refrigeration system. The workers were using hand tools to open the valves and drain off the oil when they were heavily exposed to anhydrous ammonia resulting in two fatalities.
- A worker was killed as he was disconnecting a pipe from an ammonia valve. The pipe had not been properly isolated and locked out, and it still contained ammonia under pressure. As the pipe was disconnected, the liquid ammonia was released and struck the worker's face and body.
- Equipment, such as heaters used in an industrial piping system, can also be a source of hazards if proper lockout procedures are not followed. An accident occurred when a worker was changing an O-ring in a line heater. He had closed the valve upstream of the heater but, contrary to the required procedure, had not closed the downstream valve. As he was loosening it, the end blew off the pipe, which struck and killed the worker. The average pressure in this system at the time was 8,500 psi.
- Not all industrial piping system injuries result from human error. On Sept. 27, 2010, a worker was returning an eight-inch steam header back into service after planned maintenance. The worker, along with three coworkers, was walking along the steam header catwalk checking the valve positions. A two-inch, 90 degree elbow suddenly failed resulting in 1,000 psi, 500 to 650 degree Fahrenheit steam discharging onto the first worker. He was hospitalized for second and third-degree burns over 80 percent of his body.
The Common Denominator in Industrial Piping System Accidents
Reading through these examples, it becomes very clear that the one thing missing in each situation is comprehensive system knowledge. “If only they had known” could be the lament of every safety manager who has to deal with a closed system piping accident. Making certain every worker in your facility who deals with industrial pipes knows the meaning of a label's color and taught everything they need to know about the system in question is quite a tall order, but it is one that should be pursued.
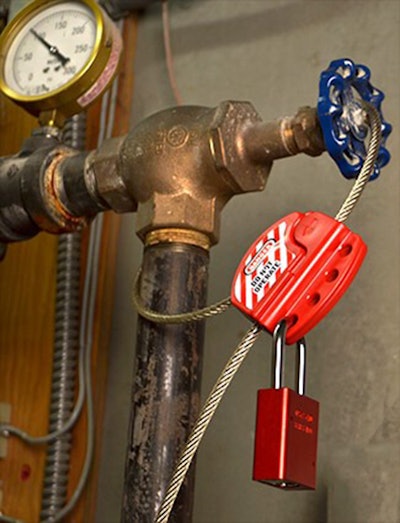
To keep workers safe when they work to maintain a closed system of industrial pipes, the following processes should be undertaken:
- Construct a process hazard analysis to address the hazards of the maintenance process, and then using engineering and other control measures to ensure worker safety. The analysis should include a complete evaluation and assessment of the industrial piping systems that are a part of the process.
- Establish written lockout/tagout (LO/TO) procedures, supply the required equipment, and make certain it is used. This is required by law under OSHA’s “control of hazardous energy” rules found in 29 CFR 1910.147.
- Ensure that all pipes and valves are properly and clearly labeled, including any necessary warning messages. Informative labels and signs should be used to remind workers about required shutdown, LO/TO, and general safety procedures.
- Create specific written lockout/tagout procedures, verify that those procedures are clear, and test the procedures to ensure they provide complete instructions for the safe performance of the work activities.
- Be sure that all employees, including contract employees and vendors, are trained in the required procedures and safe work practices, and that they understand and adhere to current operating procedures. Additionally, make certain they know where all required safety equipment can be found in the facility. This includes anything from face shields to respirators and other PPE.
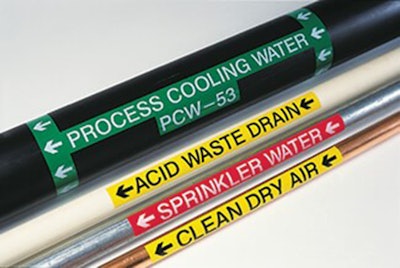
The Key to Safe Maintenance on a Closed System of Industrial Pipes Is Information
Keeping employees informed about the system they are working on is the best way to keep them safe. “If only they had known” haunts the consciences of safety managers who have dealt with catastrophe, and helping your own employees know what they need to will help keep them safe.
All employees should receive regular training in the safety procedures related to their job. In addition, they should know about other aspects of the industrial piping systems they are working on. For example, maintenance workers should have some familiarity with the operation of the processes. Following the training, an evaluation of the effectiveness of the training should be done by observing people as they work, and additional on-the-job or formal training classes should be provided as needed.
Pipe marker labels and valve tags can be used to provide critical information about pipe contents, the direction of flow, and the type of hazard presented. They may also include information such as temperature and pressure. Valve tags identify the valve, and can indicate how many valves each section of pipe has, which lets the worker know how many he or she needs to isolate before beginning work. Other components of an industrial piping system such as flanges, vents, drains, and instrument connections should also be labeled for easy identification. When workers are fully informed, they are safer, and can do a better job when maintaining a closed system of industrial pipes.
Lucas Wiseman writes for Graphic Products, makers of the DuraLabel line of industrial label and sign printers.