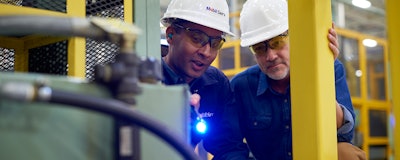
In today’s highly competitive business environment, industrial operators need their equipment running reliably to minimize downtime, maximize productivity and enhance profits.
However, most industrial equipment operates in conditions that over time can lead to a range of equipment performance challenges — including corrosion, which is a particularly significant challenge. In fact, NACE International estimates the global cost of corrosion to be $2.5 trillion, which equates to approximately 3.4 percent of global Gross Domestic Product.
The corrosion challenge should come as no surprise. Exposure to water, extreme temperatures, gases and other corrosive materials are regularly present in industrial operating environments, and these conditions can accelerate rust and corrosion formation.
One of the fundamental ways to mitigate corrosion is through proper lubrication. The right lubricants can help keep equipment components clean and protected against harmful materials, and certain lubrication-related services can help operators keep a pulse on how their equipment is performing in real time.
With that in mind, let’s take a closer look at corrosion and how the right lubrication strategy can help keep your equipment running strong.
How Corrosion Forms
Corrosion occurs when metal componentry deteriorates as a result of chemical interactions with the natural environment. There are many different types of corrosion, all defined by the nature and extent of the metal degradation.
For the purposes of this article, we will focus more on the top causes of corrosion so that we can better understand the role of lubrication.
The top three causes of corrosion are water, microbial activity and the lack of sustaining corrosion inhibition.
Water: Water is present in many industrial applications. For example, water is used as a cooling mechanism in the steel industry, while any equipment that operates in outdoor environments will naturally be exposed to water in the form of rain or seawater. If not properly managed, a build-up of water can lead to increased corrosion and the potential for greater microbial activity.
Microbial activity: Microorganisms are ever-present in the natural environment, and they are found in water, air and dirt. Keeping equipment clean and free of contaminants is the best way to mitigate microbial activity.
Lack of sustaining corrosion inhibition: Corrosion inhibitors are specific compounds used in coatings and lubricants to help counteract corrosive materials. If operators use products that do not have sufficient corrosion inhibition properties, their equipment will be more susceptible to the natural environment, including corrosive chemical reactions with water and microbial agents.
Lubrication As A Strategy To Mitigate Corrosion
Lubricants are the lifeblood of any industrial machine, protecting components against wear, contamination, and other performance challenges — including corrosion.
Operators should look for lubricants that are formulated with the right mix of advanced base oils and a robust additive package. For corrosion protection, the lubricant should have the right corrosion inhibitors to guard against humidity, water contamination and high temperatures.
But, just having corrosion inhibitors is not necessarily enough. The formulation should have just the right amount. Too little of an amount, and the lubricant will not deliver enough protection. Too much additive, and the rest of the formulation could be impacted.
This raises another important point. It’s important to select lubricants with a balanced formulation, because the anti-corrosion benefits should not come with any sacrifice in overall lubricant performance. In addition to corrosion resistance, the lubricant should be able to deliver the right viscosity, wear resistance, and oxidation stability, among other characteristics, to perform as needed in a given application. A lubricant’s performance across these characteristics is influenced by the types and ratios of base oils and additives used.
Work closely with your lubricant supplier to understand the formulation of your industrial lubricants and select lubricants that are formulated to perform well across a range of parameters, including corrosion resistance.
Invest In Services
To ensure that the lubricant is performing as needed, operators should invest in services such as routine used oil analysis (UOA) and contamination control inspections, which provide insights into real-time lubricant and equipment performance.
UOA can identify the presence of metal wear, oxidation and contamination, all issues that could degrade lubricant condition and negatively influence its corrosion inhibition properties. Importantly, operators can measure UOA results over time to identify trends in these characteristics that may indicate action needs to be taken. For example, an increase in the presence of metal wear particles could indicate that corrosion is taking place.
For a more robust assessment, operators can work with their lubricant suppliers to conduct contamination control inspections, which involves used oil analysis in combination with a manual inspection of critical equipment systems to identify abnormal operating conditions resulting from potential contamination (which, again, can eventually cause corrosion).
When proceeding with this approach, it’s best to establish an inspection schedule to help identify units in immediate need of corrective actions as well as systems with excessive oil makeup requirements. Lubricant suppliers and other maintenance partners can help recommend actions to address the source of contamination and implement recommended corrective actions.
While lubrication will not necessarily prevent corrosion on its own, it is nonetheless a key factor that can help protect your equipment against this key challenge. As outlined here, operators must have the right lubrication strategy – including the right product technologies and associated services — to ensure their lubricants are delivering maximum protection.
Alan Suan started his career with Mobil Oil in 1989 as an environmental engineer. He has held various sales and technical positions with focus in Industrial, Marine and Aviation lubrication. Currently he is a North America Commercial Lubricants Advisor for ExxonMobil, working closely with colleagues from his Mobil Serv Engineering Support Services team to advance customers mobility, productivity and sustainability ambitions.