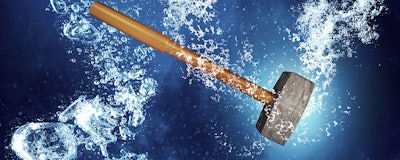
What Is “Water Hammer” And Why Does It Matter?
We’ve all heard it — that bang in the pipes when we turn off the shower or faucet suddenly. Sometimes multiple bangs shudder through the pipe as the water bounces back and forth. The same phenomenon can happen in large commercial or industrial fluid systems.
Water hammer, also called fluid hammer or hydraulic shock, is a wave or surge caused when a fluid in motion is forced to stop suddenly. In process applications this happens when a fast-acting valve closes a pipe while the water upstream is still moving. The water hits the closed valve and bounces back, creating a pressure spike in the system upstream.
How bad is it? Pressure spikes have been measured as high as 15 times higher than the normal water pressure in the pipeline. This exceeds typical UL rating safety factors and can damage equipment not designed to withstand pressures that high.
Water hammer is a problem for applications using water from public utilities that usually comes in with a pressure rating of 70-100 psi. Applications range anywhere from small dental offices to large manufacturing facilities. Water hammer is also a problem in mobile equipment that carries water, like concrete mixers or street sweepers. Industrial processes that use pressurized water can also be seriously impacted by water hammer.
Repeated over-pressurization and vibration can cause damage ranging from premature wear to catastrophic failure of pipes, tubing, fittings, regulators, pumps, floats, gauges and anything else upstream from the closure point as well as the unpleasant noise it creates.
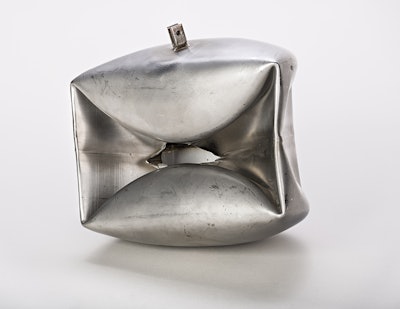
Typical Solutions And Their Shortcomings
Engineers, designers and maintenance professionals have come up with various ways to reduce the problems caused by water hammer. One obvious solution is to use a regulator upstream of the valve to lower the pressure rating and reduce the maximum pressure of the surge. However, the addition of a regulator will drop the flow rate, possibly reducing performance and productivity in the system.
There are several mechanical methods to reduce the impact of water hammer. One is to install check valves upstream to control the distance the pressure spike travels. Another is to use accumulators; pressurized vessels that divert the excess fluid until the pressure spike abates. Large systems sometimes incorporate water towers to accommodate the surge. Alternatively, a shock absorber, also called a water hammer arrestor, can be installed upstream to absorb the shock of the pressure spike.
Adding components like these increases cost and complexity as well as introducing additional potential failure points into a system.
Another tactic is to modify the whole system design. Inserting elbows and loops into piping may slow the velocity of the water hammer surge. Unfortunately, this also increases the space required for the piping and, again, increases complexity and the chance for error.
Instead, A Better Valve
The simplest approach is to attack this problem at its source — the valve. After all, it is the rapid closing of the valve that sends the fluid surging back upstream. But rapid closing is required for safe and effective operation in systems that typically use these 2-way valves. The question is how can operators get the speed they need without creating a large water hammer effect?
The answer lies in the way the valve closes. Valves that close smoothly and gently can prevent pressure spikes while still maintaining closing speed.
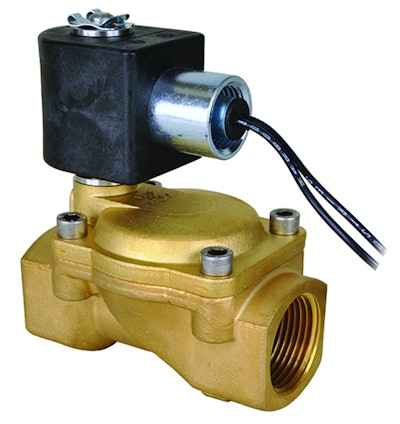
Not all solenoid valves can do this. Comparative tests of four widely used solenoid valves show a wide variation in their ability to prevent water hammer. All were 2-way, normally closed, pilot operated valves with ½” NPT threads and ½” orifices and each closed in 250 ms or less. In other words, the valves were directly comparable. Each was tested on a pipe with inlet water pressure of 4 bar (87 psi), within the range of 70-100 psi typical of public waterline pressure. The power was shut off so the valves would move to the closed position and then the pressure upstream was measured every 100 milliseconds.
Two valves hit peaks of 1440 psi, roughly 100 bar, and one hit 1101 psi or about 75 bar. Two of the three valves created not just one but two pressure spikes before the pressure returned to 87 psi. In contrast, the best performing valve reached a single peak of only 265 psi or 18 bar, less than 20 percent of the two valves with the highest spikes. The graph below tells the story quite clearly.
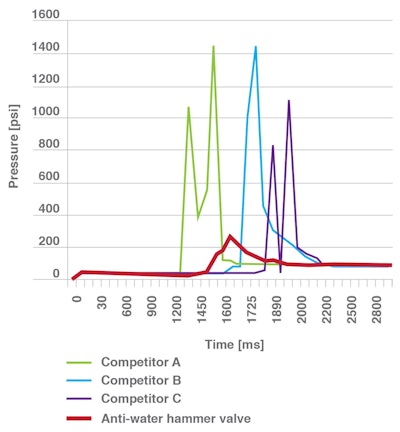
In the field
The beauty of using a valve to solve the water hammer problem is that it is simple to implement. Besides specifying the right valve, no design changes or extra equipment are required.
The benefits of reduced water hammer effect are not limited to new equipment. Anti-water hammer valves can also be used as a maintenance upgrade. While it is common practice to replace worn valves with new ones from the same manufacturer, the case for reducing water hammer is often strong enough to make plant operators and maintenance professionals consider a direct replacement.
Whether designing new systems or improving existing ones, preventing pressure spikes is a simple way to prolong service life, maintain system safety and reduce noise. Choosing the right valve is the simplest, most cost-effective way to reduce pressure spikes due to water hammer.
Johanna Baril is Strategic Marketing Manager at IMI Precision Engineering.