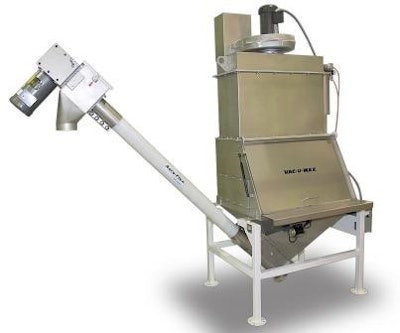
A quick Google search for images of flexible screw conveyors produces a screen full of seemingly identical images: a shaftless auger, typically inside of a plastic tube, driven by a motor that spins the auger, moving material from an inlet to an outlet. The overall design concept of flexible screw conveyors is relatively straightforward. However, the simplicity of their design can be somewhat deceiving. Much like a pneumatic conveying system, the efficiency of flexible screw conveyors is highly dependent on initial design, specialized knowledge of material characteristics, and proper calculation of conveyor flow to preserve the life of the auger. To avoid costly downtime, choosing a flexible screw conveyor engineered to meet conditions at the plant, rather than a generic off-the-shelf unit, can save thousands of dollars in the future.
Flexible screw conveyors are useful in any market where you would want to convey a bulk dry powder at high rates, including foods, pharmaceuticals, chemicals, or plastics, and are ideal for transferring powders from bulk bag unloaders, bag dump stations, and feed hoppers to blenders, grinders, or filling machines.
Using the age-old Archimedean principle, the conveyor meters product to the receiving hopper at a set rate. Ideal for low to medium transfer volumes with flood feed, the unit allows product flow to be stopped and started without the need to purge the line. Product acts as a bearing for the auger section and it is therefore recommended that the machine is left full of product between batches.
Flexible conveyors utilize a stainless steel or a carbon steel one-piece helix (spiral in shape, similar to an extended slinky that does not compress). The helix is enclosed within a stationary ultra-high molecular weight polyethylene tubing for transferring material from its feed hopper to the discharge point up to 40 ft. away.
The most common sizes of tubing are 3-, 4-, and 6-in. The thinner the tube, the more flexible the conveyor for making gradual curves to discharge heights or to flex around objects. However, thinner tubes can also make material harder to feed into the system depending on its characteristics.
Conveyor size is determined by RPMs and how many cubic feet of material users want to convey per minute, and that number is then converted to lb/hr based on the bulk density of the material to determine the horsepower needed to power the conveyor; 90 percent of the time no more than 2hp is needed.
Working with a manufacturer that provides engineered systems eliminates major troubleshooting headaches because manufacturers design and test equipment simulating conditions and equipment at the installation facility, confirming material flowability and proper convey rate for the product before the conveyor is shipped. Some conveyor manufacturers offer written performance guarantees ensuring equipment will work as promised.
Occasionally, testing in the lab under ideal conditions isnβt so ideal once in the field, but the customer is still covered with a performance guarantee and sometimes that means rebuilding an entire conveyor and adding another tough application solution to the manufacturerβs repertoire.
One tough application involved resin flakes that conveyed in-house but not in the field. The product was harsh and tacky to the touch. Once back in the testing facility, engineers discovered that the resin flakes were digging into the plastic tubing. The solution was to replace the plastic tubing with stainless steel tubing, as well as increase the horsepower on the motor, satisfying the customer.
Bulk materials properties such as bulk density, particle size and shape, as well as knowing whether the material is abrasive, fragile, dusty, cohesive, or hygroscopic, significantly affect equipment design and performance. Flexible screw manufacturers that engineer systems anticipate bulk material behavior and design robust systems using the heaviest duty augers suited to task and the highest quality gear heads available.
To ensure equipment is not compromised in the field causing down time and loss for organizations, engineered systems are modeled using sophisticated programs that calculate stress on spirals and material conveying thresholds, preserving the life of the auger, sometimes in excess of five years.
Correctly anticipating bulk material behavior based on previous experience and testing configurations specific to usersβ needs produce solutions that computer programs wouldnβt put together. An example of this is where a facility wanted to handle massive amounts of hemp seeds and included seven screw conveyors, one of which climbed an 85-degree angle with a 25-ft discharge height, moving 7000 lb. of seeds per hour.
Although the basic design of flexible screw conveyors may look nearly identical, engineered flexible screw conveyors generally carry warranties of at least two years, include specific documentation and drawings, and include test results demonstrating optimum operating conditions. Although engineered systems may cost a tad more on the front end, increased uptime and savings over time could equal the cost of an entire system.