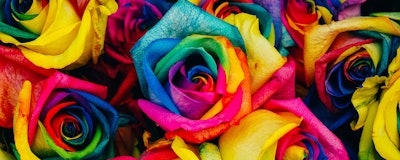

In manufacturing there are many places for color to go wrong—during specification, formulation, manufacturing, assembly, quality control, or (unfortunately) all of the above. What happens when you measure color at each step in the process and it meets the physical standard within a specified tolerance yet your final color is out of tolerance?
Even small differences in process steps can quickly add up to the dreaded “error stack,” moving your final product further away from accurate color. In many ways this is similar to the snowball effect where something of small significance builds upon itself, becoming larger and larger.
When you add up seemingly small color differences across an entire production workflow the result is often inaccurate color. As any manufacturer knows (regardless of what industry you serve), this leads to waste, rework, added costs and possibly lost revenue.
How can you stop the color error stack from happening?
Ensure everyone is using the same standard. While this may seem simple, its critical to verify that everyone – the brand specifier, supplier, plant operator and quality control team—is using the same color standard. This needs to be done at the beginning, as new people or suppliers are added and periodically throughout the project.
Ensure your instruments are in good working order. When it comes to measuring and verifying color, its important to ensure that all instruments are certified and have been maintained for optimal performance and consistency. Color measurement instruments also need to be calibrated on a regular basis as readings can drift over time due to age, wear or environmental conditions. Most color measurement instruments have a built-in timer that you can set to monitor the interval between calibrations and/or allow you to calibrate manually. You can also use a combination of software and color standards (tiles) to calibrate instruments and ensure optimal performance.
Document all measurement procedures. Documenting and establishing standard operating procedures for manufacturing and quality control is essential. This helps ensure that, regardless of location or operator, the same process is followed. When if comes to color measurements, its critical to document and monitor the following items:
- Instrument Geometry, such as sphere or 45:0
- Illuminant and Observer
- Aperture size
- Color Space (LAB, LCH, etc.)
- Tolerance
- Modes (for a sphere, SCI or SCE? For a 45:0, which M mode are you using?)
- Location of measurement and orientation
- Number of averaged measurements
- Sample presentation
- Backing material
- The environment, including temperature and humidity
- Age of the sample
Always test your incoming raw materials. Your suppliers can have color issues too. It’s important to ensure that the color of your raw materials (inks, pigments, coatings, paper, textiles, plastics, etc.) is accurate. This is especially true if you are working with organic or natural materials like cotton, leather and food as the color can vary significantly. Set tolerances around raw materials and test them when they come in. If the raw material’s color is off, so will your final product. Manufacturers can either make adjustments in formulation/production to ensure accurate color or reject the material before production begins.
Track process variables in production. When it comes to the production of color, there are many process variables that can impact color—supplier, raw materials, operator, line, temperature, humidity and many more. Manufacturers need to identify and assess which process variables have the biggest impact on color consistency and track this information across production for each sample measured.
Use data and analytics to identify color drift in production. Once companies have identified the variable data they want to track, quality control professionals or plant managers can leverage that data to better understand where color drift occurs in your process. Color quality control software (that syncs with measurement devices) makes it easy to graphically see the color variation of a series of measurement samples. This software can plot whether failing colors are too light, too dark, too red, etc. Equally important the software can be used to sort, group and analyze process variables. This makes it easier to identify patterns and the cause of color variation in production. For example, companies can produce a set of samples using the same material and run it under a variety of different settings. The data may show that a temperature increase or decreased dwell time is causing the color to shift.
Conclusion
Understanding and controlling the small color differences that occur both before you begin production and once you start manufacturing can help you avoid the color error stack and keep your processes delivering accurate and consistent color production. Its important to work with specifiers, suppliers and other third-party partners to ensure everyone is using the same color standards and operating procedures. Monitoring and analyzing color throughout production will ensure it stays on track from beginning to end and batch to batch.
Tim Mouw manages the Applications Engineering and Technical Support Team for X-Rite in the Americas. He oversees a team of 20 technical support specialists that help customers improve color quality control processes. Over the past two decades, Tim has taught over 300 courses on color science across the globe.