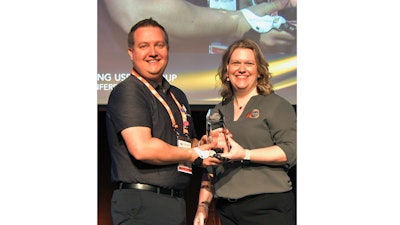
The Additive Manufacturing Users Group (AMUG) announced the winners of its annual Technical Competition, which recognizes excellence in additive manufacturing applications and finishing techniques. A panel of industry veterans selected entries from Point Designs LLC and BuildParts by CIDEAS, Inc. as Advanced Concepts and Advanced Finishing winners. AMUG Members selected the entry by Eaton for the Members' Choice Award.
The Technical Competition took place at the annual AMUG Conference in Chicago, Illinois. Nine judges scrutinized every detail of the competition entries to select Advanced Finishing and Advanced Concepts winners.
The winning entries in the 2024 AMUG Technical Competition (from left) are Coin-op Rides (Advanced Finishing), Shoulder Disarticulation Prosthesis (Advanced Concepts) and Luminaire (Members’ Choice).Additive Manufacturing Users Group (AMUG)
Chris Baschuk, Director of Clinical Services at Point Design LLC, submitted the winning entry in the Advanced Concepts category, "Lightweight Revolution: Ventilated Multi-material Shoulder Disarticulation Prosthesis." Manufactured with HP's Multi Jet Fusion, in rigid PA 12 and flexible TPU, the patient-specific device balances functionality with user comfort by leveraging the distinctive capabilities of additive manufacturing.
Baschuk noted that the prosthesis reduces bulkiness, weight and fabrication complexity associated with conventional approaches. Additionally, advanced design features, such as hexagonal lattices for breathability, heat dissipation and electronics integration, improve the patient's experience.
"This project epitomizes the potential of additive manufacturing in prosthetic development, offering a highly personalized, functional and comfortable solution for individuals with shoulder disarticulation amputations, setting a new standard in the field," Baschuk said.
"Using additive manufacturing for prosthetics is not new, but the methodology and attention to detail used in this entry are incredible," the judges said. "The forethought to incorporate lightweighting and DFAM to provide users comfort is impressive. The embedded electronics for movement were astounding and would improve the user's quality of life. This is a great additive manufacturing application to improve the human condition and an outstanding entry."
(Left) Mike Littrell of BuildParts by CIDEAS, Inc. receiving the first-place award from Bonnie Meyer for the Advanced Finishing category of AMUG’s 2024 Technical Competition.Additive Manufacturing Users Group (AMUG)
Mike Littrell, President of BuildParts by CIDEAS, Inc. and a previous Technical Competition winner, took the top spot in the Advanced Finishing category with his entry, titled "Coin-Operated Rides."
The scale models included a "Race to the Moon" rocket scooter and a futuristic spacecraft from a 1950s point of view. Littrell noted that each model contained 99% printed parts and that three additive manufacturing technologies were used: DLP (Digital Light Projection), FDM (Fused Deposition Modeling) and SLA (Stereolithography). To educate AMUG Members, Littrell displayed the scale models in three states: fully finished, sanded/primed and as-printed.
Outfitted with lights, clear lenses and a clear windscreen for the rocket scooter, the scale models were brought to life with 2K automotive-grade paint for a durable, long-lasting finish.
In the assessments by the judges, one stated, "Utilizing the right additive manufacturing technology for each part makes this a success. Many years of expertise showed in the quality of this submission. It's also a real-world example of finishing techniques."
Through voting by AMUG's Members, Eaton received the Members' Choice award.
Sam Mills, Engineering Specialist for Eaton, submitted "Fully AM Luminaire," a project by the Eaton team that included additive manufacturing and material science experts. In his entry, Mills cited team members John Hana (Senior Engineer), Mansura Islam (Senior Additive Engineer), Sabina Kumar (Lead Engineer), Riyanka Ribble (Engineering Specialist) and Chris Ring (Lighting Expert and Manager).
Members’ Choice winner, Sam Mills of Eaton (right), receiving his award from Bonnie Meyer in the 2024 AMUG Technical Competition.Additive Manufacturing Users Group (AMUG)
"The luminaire platform is the only known custom solution that leverages multiple additive manufacturing technologies, making it a pioneering solution in the lighting field," Mills said. "It demonstrated the value of AM to manufacture the entire lighting solution." The results are impressive, and the efficiency of 150 lumens/Watt is a testament to the quality of the overall product.
The luminaire, which was entered in the Advanced Concepts category, contains additively manufactured parts for 90% of the components. Employing design for additive manufacturing (DFAM) techniques, the luminaire achieves Department of Energy (DOE) manufacturing goals for reshoring, SKU reduction and efficiency. Mills stated, "By using DFAM tools for part integration, we cut the assembly time in half and virtually eliminate the need for product-specific tooling."
The judges' comments on Mill's entry noted that the solution is not cost-effective, but the AMUG Members chose to focus on the innovations and sophistication in applying additive manufacturing and DFAM.
"Excellent use of AM technologies, DFAM and lightweighting with engineering to achieve energy efficiency and ease of installation," judges said. "It isn't cost-effective, but the government contract was focused on other factors. I think the goal was achieved."
For Advanced Finishing, Ed Graham of Prototek took second place for "The Pumpkin King." Third place was awarded to Olaf Diegel of the University of Auckland for "Darth Vader Reborn."
In Advanced Concepts, second place was awarded to Rick Pressley of Renaissance Services, Inc. for "Cooled Integrally Vaned Stator with 'Cast-In Cooling Holes.'" Sam Mills, the Members' Choice award winner, took third place in the Advanced Concepts category.
Chris Baschuk, Mike Littrell and Sam Mills, or their designated representatives, will receive complimentary admission to the 2025 AMUG Conference so that they can elaborate, from the stage, on the project details and processes used.
The Technical Competition judging panel was comprised of nine AMUG DINOs. These judges were Paul Bates, Bob Diaz, Sheku Kamara, Bruce LeMaster, John Schaefer, Harold Sears, Ed Tackett, Pat Warner and Mark Wynn.