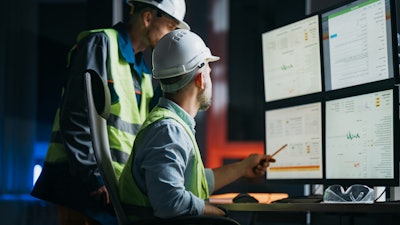
In 1886, the world’s first functional automobile, the Benz Patent-Motorwagen, was unveiled. The two-seater with three wire-spoked wheels was engineered with a light chassis and a maximum speed of about 16km/h.
About 25 Patent-Motorwagen vehicles were built between 1886 and 1893, requiring critical human skills and intensive manual labor to manufacture. The Benz Patent-Motorwagen was ahead of its time and marked the beginning of a revolution that would radically transform manufacturing across industries.
This metamorphosis has led to the current era of Industry 4.0 – or digital transformation of manufacturing – in which the integration of intelligent machines, real-time workflows and artificial intelligence has redefined manufacturing operations.
Digital transformation has further advanced the rise of the previously unimaginable connected factory. While the human component remains essential to optimize workflows, in just over a century, production systems have evolved from completely artisanal to fully connected factories that drive unprecedented efficiency, innovation, scalability and agility.
The new Zebra Manufacturing Vision Study found that 92% of manufacturing leaders surveyed agree digital transformation is a strategic priority for their organizations and 89% plan to increase tech investments this year underscoring its importance.
As we further immerse ourselves in the Industry 4.0 revolution, we are seeing technologies such as AI and the Internet of Things (IoT) transforming entire sectors, driving new levels of efficiency. Six in 10 (61%) of manufacturers in Zebra’s study expect AI to drive growth by 2029, up from 41% in 2024.
This surge in AI adoption combined with digital transformation efforts reflects manufacturers’ intent to leverage new technologies that enhance visibility and quality throughout their operations.
The market – and benefits – for digital transformation in the manufacturing sector are big. Recent research estimates Digital Transformation in the Manufacturing Market will be 367.6 billion in 2024 and is expected to reach $876.1 billion by 2029.
Top benefits for digital transformation as ranked by leaders surveyed in Zebra’s study are optimizing the workforce by enhancing productivity through automation, improving throughput to increase revenue, enhancing agility and boosting inventory management and material movement.
Digital transformation has reinvented the entire value chain, from warehousing and distribution to marketing models. It has enabled manufacturers to meet today’s expectations of efficiency, speed and customization, creating a new chapter in the history of production and commerce worldwide.
As a result, the manufacturing sector must constantly progress and work in new ways with technology. Manufacturers are focused on training teams and adopting emerging technologies to forge a workforce as advanced as the technology it uses, adept and ready for an ever-changing floor.
For example, manufacturers in Zebra’s study plan to evolve their workforce and implement more digital tools. Solutions cited include augmented reality/virtual reality (70%), computer vision (64%), wearables (61%), workforce management software (56%), mobile computers (55%) and tablets (50%).
Likewise, the management and analysis of large volumes of data represent a significant challenge but are crucial to guarantee efficiency and quality.
Manufacturers surveyed in the Zebra study pinpoint real-time visibility as key to maintaining quality yet only 16% say they have real-time visibility into manufacturing production.
Aiming to enhance visibility and quality, nearly 100% of decision-makers surveyed plan to implement fixed industrial scanners (99%), autonomous mobile robots (99%), machine vision (98%) and RFID (97%) by 2029. Adopting these advanced technologies will bring valuable real-time insights to significantly improve data-driven decision-making.
These solutions also enhance efficient management, freeing employees from repetitive tasks to focus on more meaningful work and helping to ensure the quality of production processes. In this environment, the balance between technological innovation and human development becomes the pillar to build a solid and sustainable business future.
The strategic shift to automation and augmentation on the factory floor is driven by several benefits according to Zebra’s Manufacturing Vision Study. Seven in 10 decision-makers cite the ability to focus associates on “high value” customer-centric tasks to optimize labor, while six in 10 cite meeting service level agreements (SLA) and more flexibility to physical space or the plant floor footprint.
Manufacturing transformation is real. However, digitization transcends simply implementing new technologies. It's about taking a deep dive into the dynamics of each industry.
A comprehensive understanding will ultimately distinguish the organizations that will thrive in the long term, marking a transformation journey based on both vision and innovation.
Digital transformation invites us to lead a revolution that promises a more prosperous and sustainable future. Just as the first car established a new paradigm, today we can work in new ways and embrace change to create a future where innovation is synonymous with shared progress.
---
Enrique Herrera is the Industry Principal of Manufacturing at Zebra Technologies. With over 15 years of experience in the manufacturing and technology space, he is an expert in business transformation solutions, specializing in industrial operations. Herrera is a thought-leading speaker on topics such as the Industrial Internet of Things (IIoT), Industry 4.0, digital twins and modern data analytics and serves as a trusted advisor for large industrial enterprises.