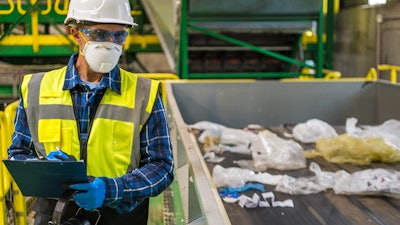
It’s difficult to overstate the sheer size and significance of the UK’s waste management sector. With a market size expected to reach nearly $109 billion by 2030, waste management is one of the nation’s largest and most vital industries.
It’s also an industry plagued by injuries, illness and negative health and safety outcomes for workers. According to the HSE, there were 1,616 reported non-fatal injuries across the waste management sector from 2022 to 2023, up from 1,555 the previous year.
When it comes to the most common types of injuries and illnesses suffered by workers in this sector, musculoskeletal disorders and accidents caused by transport operations and moving vehicles are at the top of the list. Noise-induced hearing loss (NIHL) and dust related industrial diseases are also matters of concern for workers in this sector.
In this article, we’ll highlight the key health and safety issues faced by workers in the UK’s waste management industry, and explore how a more connected approach to occupational risk management can help promote better outcomes for teams in this space.
What ‘key health hazards’ are faced by the waste management industry?
There are a number of occupational risks associated with work in waste management. Below, we review a number of industry-specific ‘key health hazards’ cited by the HSE, including musculoskeletal disorders, injuries caused by transport operations and moving vehicles, NIHL and dust-related industrial diseases.
Musculoskeletal disorders
Musculoskeletal disorders (MSDs) account for approximately one-third of all reported injuries in the waste management industry. Most of these injuries are caused by collection activities and the effects are often cumulative, meaning they worsen over time.
MSDs encompass a wide range of conditions which can vary greatly in type, severity and prognosis. MSD’s include arthritis, osteoporosis and inflammatory diseases and also commonly manifest as widespread pain conditions and connective tissue diseases and disorders.
In an occupational setting, there is clear evidence that the use of vibrating tools or equipment and the carrying out of repetitive forceful tasks can cause or contribute to MSDs. In waste management, workers often engage in tasks which involve both exposure to vibration and repetitive, forceful movement.
As a result, it’s no surprise that MSDs account for such a high volume of the injuries and illnesses sustained by waste management workers.
To learn more about what MSDs are and what their impact is, you can read this article.
Injuries caused by transport operations and moving vehicles
According to the HSE, transport operations associated with collection activities represent the most ‘significant risk of serious or fatal accidents to workers and members of the public.’
Being struck by a moving vehicle is the deadliest type of reported accident, accounting for 40% of fatalities across the sector. In fact, between 2000 and 2010, an average of six people died every year after being struck by a moving vehicle as a result of waste management activities. And as recently as 2022, that number has held steady, with the industry reporting six fatalities due to work-related accidents..
Proximity to dangerous hazards, like moving vehicles, is a nation-wide health and safety challenge. In the HSE’s most recent annual report, the most common kinds of accidents which caused fatal injuries across all surveyed industries included being struck by a moving object or vehicle and contact with moving machinery.
Of the 135 workers killed in work-related accidents, 50% of victims came into dangerous proximity of unsafe areas, moving objects, vehicles or machinery. In light of these statistics, it’s clear that workers operating in or near moving vehicles and equipment, including those in the waste management sector, remain at risk of serious injury and illness.
To learn more about the most recent HSE statistics regarding accidents at work due to dangerous proximity, you can read this brief article.
NIHL (noise-induced hearing loss)
In the waste management sector, risk from exposure to occupational noise is an issue for workers doing kerbside glass collection as well as those who operate within material recovery facilities. Much like MSDs, NIHL is often a cumulative condition that worsens over time.
This means that, by the time a worker knows that they have NIHL, the damage is irreversible.
Despite comprehensive legislation to protect workers from dangerous types and levels of noise at work, NIHL is on the rise across the UK, with thousands of new cases reported each year. In waste management, specifically, it can be challenging to balance the need for PPE, such as ear plugs and over-ear protection, with the need for teams to freely communicate, especially given noise levels near waste collection vehicles and within waste management facilities.
To learn more about a modern approach to noise monitoring and management, just check out this article.
Dust-related industrial diseases
Dust is a particularly difficult workplace health and safety issue to tackle, because it’s microscopic and it’s everywhere.
Silica dust, in particular, is a dangerous kind of dust that’s found in common minerals such as stone, rock, sand, gravel and clay. This kind of dust, among others, is nearly impossible to avoid in most recycling facilities, where it’s created from any number of activities, including shredding, crushing and sorting.
These activities create fine particles of potentially dangerous dust that can become airborne and settle on surfaces throughout the facility. If not properly managed, this dust can accumulate and pose a hazard to workers, as well as equipment.
Moreover, dust impacts everyone differently, and it’s difficult to predict with any kind of certainty how a person will respond once they’ve interacted with dust. For this reason, effectively monitoring and managing the risk from exposure to dust at work continues to pose challenges for teams across the UK, including within the waste management sector.
To read more about preventing occupational lung diseases, you can read this article.
Managing multiple sources of risk with one modern ecosystem
With health hazards at play from multiple sources, it can be challenging to know where to start when it comes to creating a safer environment for workers, especially when workers are mobile, as is often the case in waste management. The best way forward is one that enables organisations to seamlessly monitor and manage multiple sources of risk from one cloud-based ecosystem.
At Reactec, we’re pioneers in connected working. We’ve spent decades perfecting an ecosystem of workplace wearable technology, powered by an advanced Analytics platform, that makes it possible for teams to securely, reliably assess and address their workers’ exposure to occupational risk, even if they’re working alone, off-site, or as a member of a mobile team.
Through personalized monitoring of individual workers’ exposure to risk from vibration, dangerous proximity, noise and dust, R-Link - Reactec’s third-generation workplace wearable technology - supports data driven decision making that’s proven to help employers take control of their workplace risk environments.
For teams operating in the waste management industry, this means being able to overlay data from multiple sources of risk to identify trends and patterns and reveal areas of concern before they grow into bigger, less manageable issues. With the insight provided by Reactec Analytics, teams can take simple but effective action - like upskilling employees or replacing ill performing equipment - to proactively solve problems and support better outcomes for workers.
The waste management sector is a massive and important sector that underpins the smooth day-to-day operations of the nation. The workers in this space are vital to the UKs public and private infrastructure, and protecting their health and safety is critical. Teams working in this sector must adopt an approach to risk management that reflects the importance of the work that they do.