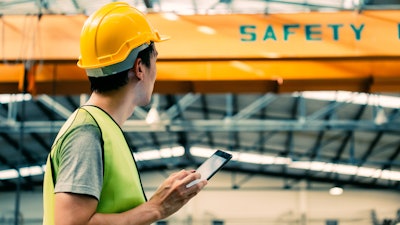
As manufacturers focus on managing controllable expenses and preventing losses in all aspects of their operations, effective safety processes and programs can have a significant positive impact. Notably, they can reduce workplace injuries, workers’ compensation costs and liability claims, as well as the likelihood of potential related litigation. Safety initiatives also can help drive improvements in production and quality, resulting in additional cost savings in other areas.
Here are some key insights to help manufacturing executives and operations managers strengthen their safety practices:
Safety starts at the top: Understanding leadership’s role
The single most important workplace characteristic that determines the extent to which any organization can achieve strong safety performance is how well leadership creates an environment where safety is fully integrated into all aspects of daily work.
This starts with establishing a strong and engaging vision of safety for the enterprise, expressed in a concise and well-written statement signed by the company’s senior executive and communicated to all employees and company stakeholders. In addition to being displayed prominently on the company’s website, the message should be included in the organization’s annual report and reinforced in all key company communications.
Employees should fully understand and embrace the organization’s requirement that the only acceptable way to work is safely and that everyone has a shared responsibility to identify, report and remove any barriers to safe work practices.
iStock
Creating a strong safety culture
Culture is sometimes defined as what people do when no one is watching. Imagine that all your managers, supervisors, and leaders left the operation for a full week to attend a strategic planning meeting.
With no members of management in the operation, how does that look from a safety perspective? Do employees continue to work productively and safely, wearing the appropriate PPE and following all safety practices? Or, is the week filled with at-risk behaviors and dangerous events?
In either case, that scenario provides a true representation of your safety culture. Effective leaders continually strive to reinforce safe behaviors, coach unsafe behaviors and establish an environment where working safely is the easiest decision. This type of relentless effort creates an optimal manifestation of a strong safety culture.
Building ownership of safety using robust metrics
Starting from the top-down and continuing throughout all levels of the organization, performance appraisals should include workplace safety evaluated based on process-leading indicators. Essentially, any performance measures must be process-oriented, under the direct control of the individual and not outcome-based.
Thus, if management is only evaluated on the number of injuries, reduction in workers’ compensation costs, or decline in lost workdays, there may be pressure to hide injuries or discourage reporting or treatment. This practice can be devastating to safety culture; it inhibits the identification and remediation of risk due to a lack of reporting.
On the other hand, process-oriented goals may include: establishing a viable behavior-based safety process; completing a certain number of risk-reducing projects; creating a formalized safety management system; and ensuring effective corrective actions resulting from incident investigations are completed in a timely manner.
Achieving employee engagement
Engaging full-time employees – as well as part-time, temporary and seasonal workers – is instrumental to an effective safety process. Complete and comprehensive employee engagement in workplace safety, is widely considered the “holy grail” of safety. Fundamentally, it means having employees who will always report hazards, unsafe conditions, and will give feedback to coworkers about safety.
These are employees who do not “do safety” and then get to work; they are employees who work safely all the time and fully integrate safety into their daily routines. Employee engagement can be facilitated by supervisors who show leadership by taking ownership for their own actions, the actions of others, and focus their attention on making the workplace a safe and more secure environment.
Having employees who take workplace safety personally and are motivated and willing to be actively involved in the safety process provides the enterprise with an excellent foundation on which to build a superior safety culture.
Examples of effective employee engagement in safety include: having highly functioning employee-driven safety committees; utilizing cross-functional accident and incident review boards; and establishing employee-comprised risk-assessment teams. In addition, supervisors must provide appreciative and positive feedback when employees follow safe work practices in addition to providing coaching on a timely basis when employees engage in unsafe activities.
Implementing a Safety Management System (SMS)
Make sure that any metrics used to measure safety performance are optimally designed for the organization. This includes a focus on process-oriented leading indicators that have known predictive value to reduce loss, risk, and improve overall performance.
The elements of a SMS include, but are not limited to:
- safety policies and procedures
- incident investigation protocols
- safety audits and inspections
- corrective action tracking and development
- safety committee activities
- job safety analysis
- risk assessment
- risk reduction efforts
- safety training and education, and
- pre-job planning
Many of these elements should be developed through collaboration between management and employees. In addition, the effectiveness of the metrics at positively influencing outcomes should be established. Metrics, which are measured but not validated, may not prove useful.
Metrics for each component of safety should be defined, levels of successful implementation established, tracked regularly and shared internally. For instance, if all employees in the receiving department are to complete annual forklift safety training, the expectation should be that by the established due date, all of the training will be completed.
Furthermore, validating that the training results in safe behaviors after it has been administered is key to success, continued improvement and sustainability. In this manner, the SMS can significantly improve the existing safety culture and help reduce injuries and accidents.
iStock
Applying ergonomic solutions
As more distribution facilities are upgraded to incorporate robotics, automation, and lean management principles, numerous workplace hazards are typically eliminated; however, others are most certainly created. Whenever new equipment is introduced, risk assessments should be conducted by safety and ergonomics professionals to evaluate any potential impacts on safety.
At the same time, as the workforce ages, workstations, equipment, processes, and procedures may need to be modified to reduce the potential for injuries. New approaches, such as the use of wearable technology, are helping facilitate more effective hazard assessments and drive advances in safety.
Reinforcing core values
As mentioned, a priority for wholesalers and distributors involves ensuring that safety is not simply a priority for employees, but rather a core value shared by all stakeholders in the organization. For example, employees’ ability to report risk – and willingness to do so – is a vital source of information for supervisors and operations managers with regard to any existing and potential hazards.
On the other hand, if employees won’t report such conditions or issues for fear of reprisal, then they will likely be less engaged in workplace safety. Accordingly, removing blame from workplace safety is paramount for any companies striving to strengthen their safety cultures. To enhance the entire process of reporting and investigation, supervisors must ensure that employees are comfortable reporting all injuries, no matter how minor. They must also make certain that investigations into injuries do not focus on assigning blame or accountability.
Establishing a robust safety process is a challenge even in the best of times and in the most productive environments. By following these established practices organizations will be able to leverage their strengths, identify and address exposures, and create highly engaging safety cultures.
Goulart
Christopher Goulart is Senior Consultant – Casualty Risk Control at Aon Risk Solutions.