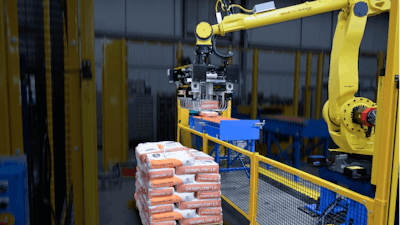
In a comparison of which industry sectors indicate the most potential for automation, recent research shows that manufacturing ranks number two (second only to accommodation and food services).
In fact, a study of manufacturing work in 46 countries, covering about 80% of the global workforce, showed that of the 749 billion working hours spent on manufacturing-related activities, a whopping 64% were automatable with currently demonstrated technology. That amounts to a savings of $2.7 trillion in global labor costs.
Compounding this immense potential for automation is the increasing pressure placed on manufacturing executives to increase profitability for their organizations. Typically, that means adopting strategies to produce quality products both faster and at a reduced cost. It’s about keeping up with consumer demand, managing competitive pricing and producing P&L outcomes that reflect sustainable growth—all with a keen eye on safety and compliance.
This is the challenge facing modern manufacturing executives, and it’s a tall order in a changing industry landscape. But it’s also what makes the potential for automation so consequential. Manufacturing executives with a major focus on the business’s bottom line are realizing the positive impacts that can be gleaned from implementing automation solutions within their processes. Even so, many struggle with the “how” of automating their manufacturing processes in ways that make the most sense for their business.
So, what does a manufacturing executive really need to know in order to adopt smart automation solutions and plan an implementation strategy that enables the company to perform better, faster, more inexpensively and with greater value to both consumers and investors? This guide provides the information and insight to support executives as they begin the process of automating their manufacturing operations. Leverage the following tips to create a path to automation that maximizes success for you and your organization.
Wauseon Machine and Manufacturing
UNDERSTANDING THE TANGIBLE BENEFITS OF AUTOMATION
The entire process begins with asking a fundamental question: What can automation actually do for the business? How this question is answered on a granular level depends on the specifics of your manufacturing business, but for the most part, it boils down to some vital competitive advantages:
Reduced Operating Costs
Automation sets the business up for a decrease in operating expenses. This decrease is largely driven by a reduction in labor, but it could also be a product of a more consistent manufacturing process, which ultimately minimizes scrap. Obviously, the less waste there is, the lower your operating costs will be.
Improved Throughput
Automation is known for improving the throughput of certain manufacturing processes. It’s about increasing the capacity utilization of your equipment. Automated solutions enable the processes to run through lunches, breaks, and shift changes, whereas human involvement necessitates equipment downtime for these occurrences. Combined with the advantage of decreased scrap, greater manufacturing availability generates greater throughput.
Profitability Growth
Particularly for companies owned by private equity firms, there’s a major focus on sustainable growth. These firms are in the business of maximizing profitability, and one of the smartest ways to do that is by automating current processes. Executives who must report to a board on how they’re going to accomplish growth plans are familiar with what it takes to garner approval. As mentioned, automation allows for reduced operating costs and increased throughput, which inarguably increases profitability.
Low-Risk ROI
When a growth plan involves designing a new product and going to market with it, there’s often a high risk of the sales volume underperforming the capital expenditure. Automation, on the other hand, is much more predictable, essentially lowering the risk of a launch that can’t meet demand.
Customization & Flexibility
Automation can be customized to the very specific needs of a manufacturing operation and designed to accommodate changes in product or process specifications down the road. This means there are no cookie-cutter requirements for ROI. In fact, there’s a distinct opportunity to achieve profitable outcomes based on a unique design and build that accounts for the individual challenges and realities of your business.
PERFORMING AN AUTOMATION AUDIT
It’s easy to get hung up on what makes a business ripe for automation, focusing too heavily on factors like size or revenue. But the truth is these characteristics don’t determine whether a manufacturing company can reap substantial profitability benefits from automating its processes.
There are small companies (under $10 million in annual revenue) that have become highly automated with immense success, just as there are large, multinational companies operating with zero automation that have tons of potential. The question is not about whether your business meets the “ideal” size or revenue, but whether automation is an obvious choice for addressing your particular processes and challenges.
This is the reason for performing an automation audit. As a manufacturing executive, have you identified areas within the business that could be improved with automation? Even if you haven’t pinpointed them yet, an experienced team of automation experts can conduct an audit to determine where automated solutions have the potential to create efficiencies, cost savings and bottom-line growth.
Of course, all of this is done in the context of your individual requirements. So, for example, if there are major opportunities to automate within your business but you have limited capital to spend, the experts would assimilate that information to create a potential multi-year plan that aligns with capital limitations, is low risk in terms of applications and aligns with your long-term strategic plans and business objectives. An audit is not about classifying your business into a predefined category of automation potential, but rather identifying what your business seeks to achieve and understanding how automation serves that bigger picture.
Wauseon Machine and Manufacturing
INVESTIGATING OPTIONS FOR A SYSTEM INTEGRATION PARTNER
As you begin or work your way through the automation audit, it’s in the company’s best interest to partner with an expert system integrator—one that has a wealth of experience in your particular area of business.
The importance of this partnership can not be overstated, given the highly complex process of designing and building an automated system suited perfectly for your manufacturing requirements. Even if you have an in-house engineer (or a team of them), it’s unlikely they possess the breadth of knowledge and skill to fully coordinate and carry out a safe and successful integration plan.
Keep in mind that this effort encompasses so much more than purchasing the actual machinery or equipment used to automate the process. Managing the complicated logistics of your entire interconnected system requires the kind of expertise that only a dedicated integration specialist—with experience in your specific line of work—can provide. If your company consists of a welding house, for instance, you wouldn’t want to rely on a company that doesn’t have experience designing automated welding solutions.
Working with an integrator that doesn’t feature the necessary experience may make the price seem more appealing, but you risk ending up with a process that doesn’t meet your requirements or a stalled implementation timeline and future complications that come with an unexpected price tag. Investigate your options thoroughly by checking out supplier directories at industrial trade organizations like the Robotic Industries Association (RIA).
INVOLVING THE RIGHT TEAM OF PEOPLE
In addition to teaming up with an experienced integration partner, it will be paramount to ensure that the process is guided internally by a well-defined leadership team. The smoothest automation integration projects are the ones that align with an internal group consisting of the following contributors:
- A P&L leader
- An operations leader
- An engineering leader
With each of these bases covered, you have the ability to detail capital and budget realities (and get the checks signed), incorporate a deep understanding of the business’s manufacturing operations and refer to the technical savvy of someone who will run the system.
Your automation integration is going to have rippling impacts on both the people on the ground and the business as a whole. That’s why it’s so important to consider each aspect of the project and assign an experienced point person to handle information gathering, communication, interaction with the integration company and supplier, and so on. You want the most critical functions involved in the planning and operating of the automated system to be represented as well as possible, and a dedicated leadership team is the ideal solution.
It’s also critical to ensure that the members of the leadership team are all aligned in their goals. In other words, is everyone on the same page with regard to capital spend, ROI requirements, operational improvements and so forth? Having the leadership team in agreement on these goals and expectations is absolutely vital to getting the project off the ground and implementing your automation system successfully.
GETTING CLEAR ON IMPLEMENTATION PLANS
With a solid integration partner and leadership team in place, it’s time to start hashing out the details of the plan. With new solutions and processes on the way, there are likely to be some necessary considerations in the way of managing downtime and accounting for process changes.
If you’re automating existing equipment, there will be a period of time when the automation needs to be installed, possibly rendering the equipment unavailable for production. The length and scope of this downtime really comes down to the specifics of the automation project. It could be anywhere from a weekend-long delay for simple implementation to over a month’s worth of designing and connecting a large, complex system.
If you’re bringing in a completely new automation system to either replace what exists or create new capacity, the period of time needed for installation is likely to be less lengthy or disruptive in nature.
As you work with the integration partner to hammer out these details, there should also be adequate discussion around issues like the automation system’s life span and flexibility for future retooling. These are elements that the experts will need to factor into the design of the machine(s). You should be aware of how factors like use, maintenance and environment will affect the life expectancy of your automated systems, and get a clear idea of how they might impact your need for parts replacements or other updates over time.
The key to planning ahead for all of these realities is understanding the customization involved in your integration plan. You’ll need to work with your leadership team and integration specialist prior to installation in order to design a scheme that makes sense for both the business and the integrator.
COMPLYING WITH APPLICABLE INDUSTRY REGULATIONS
Safety and compliance should never be an afterthought when it comes to implementing manufacturing automation. There are industry regulations and responsibilities that must be considered along the way.
OSHA requires employers to provide a safe and healthful workplace free from recognized hazards likely to cause death or serious physical harm, including general requirements for machines and related components. In the robotics world, the American National Standards Institute and the Robotic Industries Association have set forth the ANSI/RIA R15.06 Robot Safety Standard for Industrial Robots and Robot System Requirements. This is a U.S. standard issuing guidance on the proper use of the safety features embedded into robots, as well as how to safely integrate robots into factories and work areas.
Perhaps the most notable of these requirements involves conducting a task-based risk assessment of each system and tabulating ways to mitigate the identified risks. Risk assessments calculate factors like the potential severity of an injury, the operator’s exposure to the hazard and the difficulty in avoiding the hazard, with risk levels ranging from negligible to very high. It’s ultimately the responsibility of the end user to create a risk assessment and maintain it as equipment is modified, but a responsible integrator or machine builder will already have performed a risk assessment to ensure they’ve designed a safe system that matches regulations, and will supply that assessment to the end user.
PUTTING AUTOMATION TO WORK FOR YOUR BUSINESS
Manufacturing automation continues to be a game-changer for companies across a wide range of industries. As you embrace the technology and advance your processes in sophistication, the implementation effort can feel like a daunting one. If you approach the process with an informed perspective and the partnership of an experienced integration team, however, it becomes a far smoother and immensely more successful one.
When planning your integration project, do so with the understanding that there’s more to modernizing and staying competitive than this project alone. You’ll want to continue reassessing your needs regularly and adopting new forms of automation as they become congruent with your business goals.