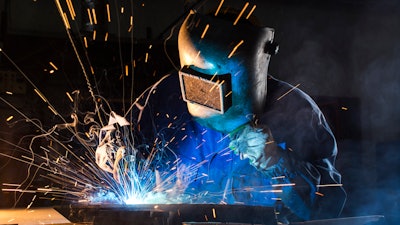
Hobart announced the grand opening of its new Customer Experience Center at its headquarters in Troy, Ohio. This approximately 9,000-square-foot space has been designed to provide customers and distributors with technical, product and customer service support.
It will allow for both on-site and virtual demonstrations of Hobart filler metals, combined with total welding solutions from other ITW Welding Group companies, including Miller Electric Mfg. LLC, Bernard, Tregaskiss and Jetline.
“Our entire industry is threatened by a shortage of qualified welders, so our focus is on developing products that ensure weldability and productivity,” said Blake Heim, commercial director at Hobart. "This facility allows us to mitigate that industry pain point by providing the highest level of support to the industry. We can offer our distributors and salesforce the knowledge they need to provide filler metals that are easier to use and drive productivity."
The Hobart Customer Experience Center consists of several dedicated spaces.
The Customer Applications Lab (CAL) features two robotic welding systems, including the new Hercules automated MIG welding system from Hobart, Miller and Tregaskiss, along with semi-automatic welding stations and submerged arc welding equipment.
It also includes pipe positioners, plasma cutters and advanced process equipment. Hobart welding engineers use the CAL to develop and test procedures to help customers improve productivity and quality.
“The CAL offers our customers a great opportunity to improve their businesses. It allows us to bring in their parts or mock them up and apply the preliminary work to advance their welding processes,” said Tre’ Heflin-King, applications engineering manager at Hobart. “Our customers are able to see the filler metal and welding equipment solutions in action before putting them into production. They can also try new technologies here.”
The Customer Experience Center also includes a classroom where distributors and ITW Welding sales team members receive training on filler metals, new welding technologies, welding best practices and more.
The classroom, along with a weld training lab, provides the basis for growing welding knowledge. The weld training lab consists of smaller power sources, plus TIG and stick welding machines, and offers the opportunity for hands-on training with new equipment and filler metals.
For customers, distributors and sales team members who are not able to visit the Customer Experience Center in person, Hobart can provide support via a virtual training lab. This lab features fully equipped welding stations and multiple cameras.