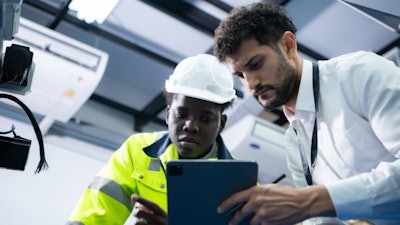
The top 5 areas where you can reduce operational risk are:
- Health and safety
- Quality
- Efficiency
- Compliance
- Brand reputation
With the right data insights, you can improve these areas of performance for better output, better outcomes, and better opportunities for growth in the future.
Improving Health and Safety Outcomes
Perhaps the greatest area of operational risk is health and safety. That’s because employee safety incidents are more important and alarming than any other indicator of operational performance.
Recurring issues within the EHS department often indicate that there are cultural issues within the facility that you need to address. Complacency is one of the biggest killers of performance. If you don’t listen to what the data is telling you, your chances of having a severe EHS incident skyrocket.
EHS Performance Data
Here are some of the top data sources you should rely on to improve EHS outcomes within your manufacturing facility:
- Incident and injury rates
- Employee and contractor training compliance
- Near miss reports
- Lost time incidents
- Safety audit outcomes (pass/fail rate)
If you haven't had an incident in a while, don’t take it as a sign that all is well. In fact, it may mean that your team isn’t being proactive about safety by reporting issues in real time. Where possible, use data like near miss reports to reduce safety risks before incidents happen, not after.
Eliminating the Risk of Quality Errors
Ineffective quality management leads to all sorts of operational risks. They include things like product recalls, costly rework, raw material waste, and production shutdowns or slowdowns.
Some of the top data points you can collect to reduce these risks include:
- Defects per million opportunities (DPMO)
- Process rework rate
- Kickout rate
- Scrap volume
Aside from these KPIs, you should also thoroughly document all quality inspections and audits. This is why every manufacturer should have both a quality management and change management process in place. By analyzing your outputs and carefully implementing changes to the variables in your process, you can quickly reduce risks of quality-related recalls and PR disasters.
Preventing Operational Downtime
In manufacturing, planned downtime is necessary to ensure the integrity and efficiency of the operation. But unexpected shutdowns and prolonged downtime events can have a major impact on the bottom line. That’s why there’s a constant struggle between productivity, quality, and safety. How much risk for the sake of output is too much?
That’s where your productivity data comes into play. You want to analyze information like your throughput rate and lost time incident rate to accurately predict how much downtime to include in your production forecast.
Another qualitative source of data is facility maintenance logs. Use the information within these logs to understand answers to questions like:
- What is the overall health of our facility equipment?
- How often do we need to shut down certain equipment/machines to keep them functioning at the highest level?
- What is the average time it takes to repair or replace specific equipment?
- What time of day, month, or year are machines likely to need maintenance?
Documenting manufacturing equipment maintenance is a great opportunity to reduce operational risk of unplanned downtime and lost productivity.
Managing Compliance Risks
Health, safety, and quality issues all increase your risk of noncompliance with OSHA, FDA, EPA, ISO, etc., regulatory requirements.
Training is a major regulatory requirement of most agencies. You need to keep detailed, accurate training records that demonstrate your team’s compliance with job qualifications. Using a learning management system (LMS) to keep track of training assignments and deadlines is an easy way to make sure you don’t miss important requirements.
It’s also a good idea to document all your compliance audits—both internal and external—so you can follow up on corrective actions. If you don’t track action items after an audit or inspection, you’re at greater risk of a compliance citation in the future.
Avoiding Risks to Brand Reputation
As a manufacturer, you likely don’t interact directly with customers, but you still have a major impact on your company’s performance in the market. There are three main areas where manufacturing can negatively affect brand perception: product quality, consumer safety, and employee satisfaction.
Quality of Goods and Services
Regardless of how efficient your processes are, producing low-quality goods and services is a sure way to weaken your market share. The better your outputs, the more likely people are to continue buying from your brand.
To ensure the quality of your offerings, though, you need data from the people and businesses downstream. Try reviewing support tickets to find ways to improve your outputs and reduce the risk of losing customers. Or ask distributors for data on inventory turnover for your products. This information can help you find risks within certain product lines or services that don’t meet market expectations.
Consumer Health and Safety
Another major factor to consider is the health and safety of buyers, surrounding communities, and anyone else downstream of your manufacturing process. Major process safety incidents can have catastrophic consequences for brand longevity.
Use the data from your environmental impact assessments, product recalls, supplier audits, and more to protect against these risks.
Employee Satisfaction
The experience of your employees is also critical to overall brand reputation. While it’s true that you can’t make anyone feel valued or appreciated, there are a lot of things you can do to increase your chances. Here are some ideas of data-driven processes to gauge employee satisfaction:
- Conduct employee perception surveys
- Document 1:1 meetings
- Collecting internal feedback about company policies.
Bottom line: If you want to reduce operational risks related to brand perception, you need to gather qualitative data on the experience of your employees and customers.
Best Practices for Data Management
Your decisions are only as good as the data you use to make them. That’s why having strict standards for data management is essential for long-term success. Here are some of the best practices for collecting and managing manufacturing data:
- Use EHS software to assign and track action items like audits, inspections, incidents, and investigations.
- Complete a monthly audit of your maintenance and training logs to ensure you don’t miss any deadlines.
- Use the same syntax to name reports and files so they’re easy to find.
- Download a backup of critical operational data regularly to prevent losing anything.
- Set maximum thresholds for KPIs so you can find and fix concerns before they cause larger problems.
- Use a standard format for your reports so they’re easier to compare with each other.
In manufacturing, there are so many different types of information you could collect, so it’s important to focus on the KPIs that address the needs of your specific facility. A standard method of formatting and organizing data makes it easier to reduce operational risks—even if the data itself needs improvement.
The more effort you put into data management and analysis, the less likely you are to suffer major setbacks related to safety, quality, or productivity. Just make sure that your process is user-friendly and sustainable, so that it provides lasting benefits.