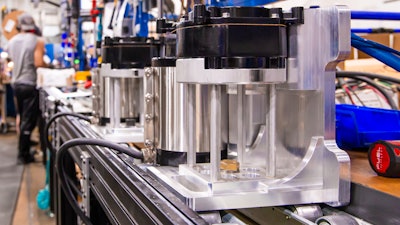
Manufacturers that have successfully implemented automation strategies have generally been better positioned to weather the economic storms of the past couple of years, making them more resilient to supply chain disruptions and labor shortages and better able to reliably meet customer needs and respond to volatile demand and new market opportunities.
Challenges and Opportunities for Mid-Sized Manufacturers
Typically, small and medium-sized enterprises (SME) have been slower to implement manufacturing automation, but those that have done so have achieved more success. Only 26% of SME companies say they are using automation across the organization or have fully automated processes in at least one function or business unit, compared to 41% of larger organizations, according to McKinsey & Company. However, the survey found that 65% of respondents at smaller companies report success with automation, compared with 55% at large organizations.
The lower adoption rate, but higher success rate, of automation at SME manufacturers is attributed to several factors. As a function of their smaller size, they tend to naturally take a more comprehensive view, considering the entire organization under the scope of automation efforts. And while this can make them more strategic in their approach, their more limited financial resources often make them more deliberate, tactical and prudent in the selective investment in the automation initiatives that will have the most impact and best ROI.
At Bison Gear and Engineering, a manufacturer of gearmotors and other power transmission equipment in St. Charles, Illinois, we believe we represent one of the success stories that exemplify the particular challenges and opportunities that automation presents for mid-sized manufacturers.
FANUC robot performing gear blank finishing operation.Bison Gear and Engineering
Automation Serves the Goals of Lean Manufacturing
Our automation strategy is a component of our Lean Manufacturing system of continual improvement that focuses on eliminating waste throughout the entire value stream to deliver products with shorter lead times and fewer defects using less human effort, inventory and costs.
In the early 90s, Bison deployed a formalized Total Quality Management (TQM) program that included practical training for all office and union employees. This program evolved in 1999 to a Lean Manufacturing strategy using the tools of Lean such as 5-S, Kaizen Blitzes, Kanban and Single Minute Exchange of Dies (SMED). Using Lean Manufacturing concepts, we re-engineered manufacturing processes where components were made in batches, into one-piece-flow cellular manufacturing processes.
This methodology provides the context for our investment in automation and other state-of-the-art technology. Automation is not an end in itself, but rather a means to achieve our Lean Manufacturing continuous improvement goals.
The other key principle in our automation strategy is the view that automation is a means of enhancing human productivity, rather than a way to replace manual labor.
The Challenge of Automating High-Mix, Low-Volume Production
When it comes to automation strategy, our most fundamental challenge at Bison is our product mix. We produce a broad range of gearmotors and PMDC motors with various features and characteristics, and the product mix, the order quantities and the priorities are constantly changing. Our production volume is more than 375,000 units annually, with production runs per order often about 25-50 units.
In manufacturing, the higher the product mix and the lower the volume for each production run, the more complicated the process and the more difficult it is to implement automation. For production lines requiring frequent and significant changeovers for different products, it is hard to design automated solutions that can be as flexible as a human operator.
In terms of the challenges of implementing automation, manufacturers are typically segmented into three categories, with Bison falling into the middle category:
- Mass Manufacturing — Characterized by very large production runs, little or no variability, short cycle times, long lead times, stable product requirements and no urgent orders, mass manufacturing is well-suited to extensive or complete automation.
- High-mix, low-volume (HMLV) manufacturing — Also known as Variable Batch Production, high-mix, low-volume (HMLV) manufacturing is subject to changing and sometimes sporadic customer demand, making the production environment more complicated and more difficult to automate. Automation solutions are often introduced incrementally and targeted to specific steps in the production process where they can have greatest impact.
- Custom production — In manufacturing facilities that produce “one-off” products and very small batches, automation is primarily implemented to assist workers in applications such as material handling systems and “cobots” (robots that assist human operators).
At Bison, we fall squarely in the middle category, but like other HMLV manufacturers, we have implemented automation solutions that are found in the other two categories: we implemented fully automated processes that mass manufacturers use when it makes sense, and we use systems that assist human operators when possible and practical.
Full Automation where it makes sense
At our facility, the component parts tend to have more commonality than the final assembled motor, and therefore much of the machine automation that we have implemented is upstream at the part generation level.
For example, the process of turning slugs of steel into a finished gear blank is relatively straightforward to automate. The geometry is similar from part to part, except for variations in the bore size and outside diameter and a few other characteristics.
We have therefore installed a Fanuc robot in a “lights-out” manufacturing cell that can be run without any human interaction from raw materials to inspected finished parts. The old process required two full-time operators per shift and now one operator keeps an eye on the system while tending to other machines.
By reducing the labor requirements of this process, we have been able to expand capacity elsewhere. By incorporating a Renishaw comparator, we have automated the inspection process for improved quality and proactive maintenance. The system continually monitors system accuracy and performance and automatically adjusts parameters when cutters wear or bores begin to drift.
Assisting Workers where possible
At the other end of the automation spectrum, we have implemented many automation solutions to assist workers with manual labor in the production processes that are best performed by a person. We have performed analysis on the ergonomics of each process to improve safety and performance.
One example is an assembly line we built for our heaviest product, a 35-pound motor when fully assembled. Previously, each operator in a batch processing arrangement needed to lift each piece twice, handling approximately 30 pieces per hour and 200-250 pieces per shift. Now a single-piece workflow process eliminates all lifting.
Each piece moves along rollers and all the tooling and equipment is positioned to perform tasks without any lifting of the part. The process is safer and causes less fatigue. As a result, we have increased productivity because throughput no longer declines and the end of each shift.
We have implemented many other material handling solutions throughout our facility to make our entire operation more productive and safer. We have also automated parts inventory, shifting from a traditional stockroom approach to an efficient inventory system that is more localized to where it is consumed. Two vertical inventory towers bring a tray of parts to each workstation that is customized for what the operator needs to use for that day or for a particular job.
The Power of Automation
Small and medium-sized companies with a high product mix can take advantage of the transformative impact of automation.
Customers benefit from the increased production efficiency that results in shorter lead times and improved quality. The reduction in labor requirements means domestic products can be offered at prices that are competitive with imports, thereby obviating the transportation delays and other hassles of sourcing overseas.
Employees benefit from a safer work environment, with less risk of injury and fatigue. Automation as part of Lean Manufacturing work cell arrangement fosters teamwork and improves employee engagement and satisfaction.
And Bison has benefitted as a company from our automation strategy. Our highly efficient manufacturing has enabled us to be responsive and reliable suppliers to our customers, even during the supply chain disruptions and labor shortages of the pandemic, and positions us well with the capacity, resilience and flexibility to continue to grow in the future.