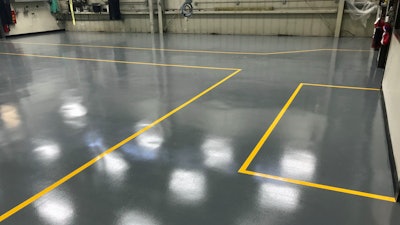
Picking the right floor coating for your industrial facility can be a challenge. Epoxies are tried and true, but have some well-known shortcomings. Newer coatings like polyaspartics, polyurethanes, and polyureas sound promising, but they come with their own pros and cons
So how do you decide?
The truth is, there’s no “one size fits all” answer to this question. The best floor coating for you is going to depend on your specific circumstances:
- Do you have a high traffic facility?
- Is it climate-controlled?
- What corrosives are going to be present?
- Can you afford to shut down for a week while your coating cures?
READ MORE: High Solids Coatings: A Solution to VOC Regulations for Facility Managers
Once you answer these questions, the picture becomes a little clearer.
Read on for our definitive guide to commercial floor coatings, and the situations in which each one excels — or falls short.
Epoxy coatings
Epoxy coatings are one of the most common heavy duty floor coatings, and it’s easy to see why; they’re durable and extremely resistant to everything from acids to oils.
But they’re not without certain disadvantages. Epoxies tend to be brittle, which can make them vulnerable to extreme temperatures, and shifting in the substrate. They’re also vulnerable to certain substances, like lactic acid, or UV radiation, which can both degrade the appearance of an epoxy floor coating. They also tend to be very slick, so you’ll want to use an anti-slip additive if you’re applying your epoxy as flooring.
Application is another potential drawback, as an epoxy coating can take up to a week to fully dry. If you need a quick turnaround, epoxies are probably not for you. Still, it’s a versatile coating that’s great if you’re using it in a climate-controlled environment, and need a high degree of chemical resistance.
Self-leveling epoxies are also an exciting (albeit more expensive) option for certain projects.
Polyurethane coatings
Polyurethane coatings give you a lot of the durability and resistance of an epoxy, along with greater flexibility and faster curing.
Polyurethane coatings can flex and bend, so if you’re using it on, say, a parking garage in a climate that sees huge swings in temperature, it’s much less likely than a conventional epoxy to crack as the substrate expands and contracts.
They’re also very resistant to substances like lactic acid, which makes them ideal for dairy or food preparation facilities.
Polyurethane has another advantage over epoxies: These coatings have significantly lower viscosity than epoxies, which means you don’t necessarily need high-powered equipment to get the job done.
As we touched on above, application and curing is faster than with an epoxy, but polyurethane application comes with its own unique challenges. Polyurethane is very sensitive to humidity during application, and the conditions during curing have to be tightly controlled, or the coating could be ruined. For that reason, many experts recommend that you get experts to apply your polyurethane coating, rather than attempt a DIY job.
Polyurea coatings
Polyurea is a type of polyurethane coating that’s become increasingly popular, thanks to its quick application, excellent durability, and superior moisture resistance.
One of polyurea’s biggest advantages over a conventional polyurethane or epoxy coating is that it’s flexible, so if the material it’s bonded to expands or contracts (due to temperature changes, for example), polyurea can flex and bend with the material instead of cracking.
Polyurea coatings also boast best-in-class UV resistance, and won’t fade at all if they’re exposed to sunlight; they also have an unmatched resistance to moisture.
These characteristics have made polyurea one of the most popular coatings for garage floors, as well as in water systems, where they’re often used in pipelines. If you’re looking for something really tough, or something that’s specifically resistant to moisture or UV light, polyurea is the way to go.
Polyaspartic coatings
One of the newest and most promising entrants in the industrial coatings field is the polyaspartic coating. Polyaspartics are similar to polyurethane coatings, but have a few crucial differences.
One of the biggest advantages of a polyaspartic coating is that it goes on in a single coat, rather than the multiple coats required by epoxies and polyurethanes. That saves time and money, since it requires less material. And they cure very fast too— you can safely reenter a space within hours of application.
They’re also incredibly durable; they’re resistant to scratches, stains, and chemicals, and won’t degrade if exposed to sunlight or moisture. And because most polyaspartics are 100% solids, they emit little to no VOCs, meaning they’re environmentally friendly.
If polyaspartic coatings have any drawbacks, it’s that early polyaspartic coatings didn’t have great adhesion. After a few well-publicized system failures were chalked up to polyaspartics with poor adhesion, the coating was dogged by a bad reputation. However, the technology has come a long way since those days, and contemporary polyaspartics have adhesion that’s as good as any coating on the market.
Tommy O’Shaughnessy
Tommy O’Shaughnessy is the owner of Industrial Paint and Protection Magazine, an outlet dedicated to helping facility managers, engineers, and contractors understand the world of industrial coatings.