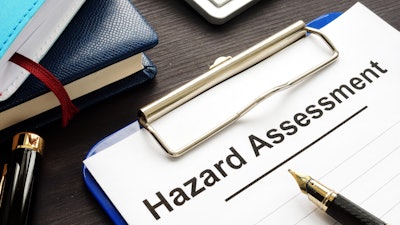
Compliance and safety officers all over the United States performed 33,401 inspections for the fiscal year (FY) 2019. In the past year, OSHA has also provided safety and health training to a record number of workers, over one million.
“OSHA’s efforts – rulemaking, enforcement, compliance assistance and training – are tools to accomplish our mission of safety and health for every worker,” Loren Sweatt, OSHA principal deputy assistant secretary of labor, said in a statement. “I am proud of the diligent, hard work of all OSHA personnel who contributed to a memorable year of protecting our nation’s workers.”
And this is a trend that will likely continue. The FY 2020 budget shows an additional $3.8 million in funding for compliance and safety officers, with plans to add 26 more inspectors in the next year.
Part One: About OSHA Inspections
OSHA is a relatively small federal agency for overseeing the health and safety of 130 million workers. With more than eight million worksites around the country and roughly 1,000 compliance officers, the likelihood of a surprise OSHA inspection may be slim, but experts say being prepared goes a long way.
Most employers are not given advanced notice when a compliance officer shows up for an inspection. In an effort to focus inspection resources on the most hazardous workplaces, OSHA schedules inspections prioritizing:
- Imminent danger situations: Jobsites where immediate death or serious harm is likely is OSHA’s top priority.
- Severe injuries & illnesses: When a severe injury or illness occurs, employers are required to report it, usually prompting an OSHA inspection.
- Worker complaints: With more than twenty whistleblower protection laws, OSHA takes employee complaints very seriously.
- Referrals: Federal, state, or local organizations may contact OSHA urging an inspection or investigation.
- Targeted inspections: OSHA often targets high-hazard or high-risk industries, like manufacturing, or individual workplaces that have had high rates of injuries or illness.
- Follow-up inspections: In certain situations, OSHA will return to a workplace to check for abatement of violations cited in the previous investigation.
iStock
An OSHA inspection has five fundamental components:
- Presentation of credentials: Employers should always ask to verify credentials of the certified safety and health official (CSHO); there have actually been cases of scammers posing as OSHA inspectors and requesting payments for fines – something OSHA would never do.
- Opening conference: During the opening conference, the inspector will explain why the workplace was selected to be issued and describe the scope of the inspection.
- Walkthrough: The CSHO won’t tour the entire facility but will visit the areas identified within the scope to inspect potential hazards to take notes and pictures. Additionally, inspectors will review injury and illness records, check for the official OSHA poster, and may even point out hazards that could be corrected immediately.
- Employee interviews: An OSHA inspector pulls aside a random selection of employees for brief interviews covering basic topics such as what safety training he or she received, concerns, etc.
- Closing conference: Inspections will typically last just a single workday but can stretch over multiple visits depending on the number of violations identified and the size of the facility. After the inspection, the compliance officer will hold a closing conference, typically by phone, to discuss findings, possible violations and citations, and any courses of action for the employer to take.
Part Two: Staying Prepared
You probably won’t know when a compliance and safety officer will come knocking, but you can be prepared. Even if your workplace doesn’t get inspected for the next five years, utilizing these methods will reduce injury and illness rates, lower related costs (like workers’ compensation), engage employees, and increase the overall productivity of the facility.
Implement a Safety & Health Program
OSHA advocates strongly for businesses of all sizes in any industries to establish a safety and health program, one of the most valuable practices an employer can add to their workplace. In addition to providing resources and offering tools, the agency outlines seven core elements to any effective safety program: management leadership, worker participation, hazard identification & assessment, hazard prevention & control, education & training, program evaluation & improvement, and communication & coordination for multiemployer worksites.
iStock
Complete Hazard Assessments
Find the hazards before the compliance officer does by conducting regular hazard assessments of your facility. OSHA recommends six specific action items to performing a hazard identification and assessment:
- Gather information: Collect operating manuals, Safety Data Sheets, inspection records, incident investigation records, injury and illness documents, and even input from employees.
- Inspect the workplace for safety hazards: Like a compliance officer, take a tour of your facility to look for any safety hazards. Inspect equipment and use checklists to identify common hazards such as electrical hazards, fire protection, general housekeeping, etc.
- Identify health hazards: Health hazards aren’t as apparent as safety hazards usually requiring additional testing or observation. Review safety data sheets, identify physical and biological hazards, conduct exposure assessments when possible, and review related medical cases.
- Conduct incident investigations: Create a procedure for thoroughly investigating all workplace injuries, illnesses, and near misses. Be sure to document exactly what happened and work to identify the root cause of the incident. What exactly led to the failure?
- Look for hazards related to emergency planning/nonroutine situations: Identify and eliminate any hazards that may be associated with emergency scenarios or infrequent situations (like a hazardous spill or nonroutine maintenance).
- Evaluate & implement hazards controls: Use all of the info gathered from the previous steps to evaluate and prioritize what needs to be addressed immediately.
Stay up to date with regulations
Keep up with changing regulations and get resources by connecting with industry experts, joining trade associations, attending related training sessions, and regularly checking the Department of Labor and OSHA websites. Additionally, consider appointing a safety and compliance officer – this individual can be in charge of ensuring compliance or at the very least check up on any changes.
Keep your Records Accurate
Safety and compliance officers will review injury and illness records during the walkthrough to determine the focus of the inspection. In order to avoid a penalty, most employers are required to maintain records of serious work-related injuries and illnesses at the worksite for at least five years, posting an annual summary every year from February through April.
Several OSHA standards mandate certain safety programs, such as confined space entry, an emergency action plan, a fire prevention plan, a fall protection program, a lockout/tagout program, a hazard communication program, spill response plans, etc. The CSHO will ask to review any required written programs and related documents like Safety Data Sheets or PPE hazard assessments.
OSHA conducts thousands of inspections every year, and continues to be an important leader in training workers on health and safety practices. Certified safety and health officials often don’t provide advanced notice before an inspection, but there are steps any facility may take to be prepared and stay prepared. Completing your Jesse Allred
Jesse Allred is a blog writer for Creative Safety Supply, providers of visual safety and Lean manufacturing resources. She enjoys sharing information and advice for facilities to achieve efficiency and keep employees safe. For more information, visit creativesafetysupply.com.