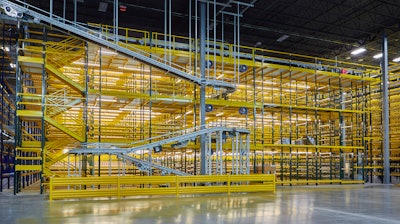
With continued e-commerce growth, now more than ever, companies must continually re-evaluate their inventory needs, so they can reliably fulfill orders quickly and efficiently. In this effort, automation is a crucial element in material handling efficiency that is becoming the standard in modern logistics.
“Today, every company that has warehousing or distribution has either implemented some type of automation or is considering it. The largest companies are incorporating ASRS [automated storage and retrieval systems], autonomous robotic devices and AGVs. Smaller companies are using a scaled-down approach such as shuttles or conveyors to increase their operational efficiency,” said Bryan Gauger, president of Cisco-Eagle, a full-service, material handling systems integrator that provides warehouse design, equipment and project management services.
These automated systems pick products, totes or pallets from increasingly voluminous, precise storage locations and move them to designated areas for shipping and fulfillment. In contrast to labor-intensive, manual material handling, automation can significantly improve productivity, accuracy and consistency while reducing operational costs.
However, it is essential to understand how indispensable a role the racking plays in enabling warehouse automation, says Gauger.
“In any automated warehouse system, the rack is foundational. It is the base of the system, where all inventory is stored and retrieved, so it plays an integral role in the automated system’s overall reliability, productivity and efficiency,” said Gauger.
He adds that the rack structure must provide a controlled environment in which every storage location is uniquely identified, tracked and integrated with the automated warehouse system.
The trend toward increased warehouse storage density, along with automation, is only intensifying the need for greater precision and tighter tolerances. High-density storage is becoming common with drive-in, pushback and pallet flow racking and even floor-to-ceiling rack-supported buildings. Narrow aisles are leaving only inches for autonomous vehicles and robotic devices to pass.
With warehouses storing ever greater volumes and variability of product, the racking must also be rigorously engineered to meet all necessary building and construction codes.
Steel King
Critical Rack Tolerances
When the warehouse rack systems used with automation are more than 10 meters high, any out-of-tolerance dimensions can quickly cause errors or damage when automated systems attempt to store or retrieve items.
According to Gauger, exceptionally tight rack tolerances in the range of only one to two-millimeter variations have become essential today, even though it can be challenging for rack providers.
Extremely tight rack tolerances are required to use ASRS. These advanced warehouse management systems are designed to efficiently store, retrieve and manage inventory in manufacturing, distribution and storage facilities. ASRS combines conveyors, shuttles and robotic mechanisms with software control systems to automate the movement of goods from multiple levels within a storage facility to make efficient use of the available space.
Because of this, rack tolerances must be precise for the ASRS’s computer-controlled storage and retrieval system to work properly. If tolerances are off, loads can deposit into a beam, upright or in the wrong storage location.
Gauger points out that automated crane systems, commonly integrated with ASRS, must be paired with racking of remarkably precise construction to function reliably.
“When [a crane] expects a pallet to be at a defined location and height, there is little room for error,” explained Gauger. “If the rack does not meet required tolerances or FEM Racking and Shelving specifications, every rack location has to be mapped into the crane’s control system row by row, which is very time-consuming. To avoid having to map the entire system, they need the rack to be constructed to very tight tolerances.” FEM Racking and Shelving is an international organization that represents and protects the interests of the racking and shelving industry by promoting common technical standards.
The construction of the rack also plays an important role in facilitating automation. Although Cisco-Eagle can work with any vendor, Gauger often opts to partner with a preferred rack supplier, Stevens Point, WI-based Steel King Industries, an OEM that provides pallet rack and custom storage rack solutions nationally.
“The construction of the rack is very important, including where the holes are punched, how it is welded together, the straightness of the beams and the squareness of the uprights. This is as important as anything within the system’s design – and that is what they offer. For instance, they use primarily robotic welders to provide reliable and precise welds,” said Gauger, adding the two companies have collaborated on projects for over 30 years.
Engineered Solutions
Although Cisco-Eagle has its own engineers, it finds that working with a supplier like Steel King facilitates integration with automation because the OEM’s engineers provide valuable assistance with rack design. The collaboration enables full integration of AGV use and the optimization of extremely space-efficient high-density pallet rack designs, such as pallet flow and pushback.
“Since most warehouses are 25 to 40 feet tall, we can utilize the entire cubic space from wall to wall, floor to ceiling, with a rack like pallet flow or pushback. When you utilize AGVs to pick inventory from these locations, the benefits multiply even more through automation,” said Don Heemstra, Vice President, Sales at Steel King.
Pallet flow racks can store up to 100 percent more product than selective racks and reduce aisle space by 75 percent. These racks use dynamic flow rails inclined in a static rack structure, so loads placed on one end safely move by gravity on rollers to the unloading end, with speed controllers acting as gentle brakes.
When designed and installed correctly, removing each pallet load will cause the pallets behind it to move forward automatically.
Pushback pallet racks offer up to 90 percent more product storage than selective rack systems and up to 400 percent more selectivity than drive-in rack. Unlike static, single-pallet deep selective racks, a dynamic pushback rack system allows storing pallets two to five deep while providing easy access to various SKUs. Pallets are stored behind each other in a series of nested carts and load from the same side of the system.
This eliminates separate aisles for each function. Composed of a stable rack along with a series of inclined carts and rails, the pushback system allows one pallet to roll forward when a pallet is pulled.
“Even drive-in and bulk static rack can be integrated with some AGVs,” said Heemstra.
As the rack becomes larger and more complex, it must be designed for the specific location, expected seismic activity and required loads. When this is necessary, according to Cisco-Eagle’s Gauger, engineers at a rack supplier like Steel King help expedite the process of meeting code.
“Their engineers often research the building location, determine the seismic zone and tell us what we need to do to meet code, such as use larger base plates or additional bracing. Their expertise will also help us meet a new specification through the Rack Manufacturers Institute (RMI) that will be published in the 2024 International Building Code,” said Gauger.
According to Gauger, the OEM’s engineers also assist with design for racking, such as ASRS, which must often be strong enough to support stored pallet loads or mini loads up to 40 feet high. Larger unit-load ASRS are usually designed to handle pallet loads of 1,000 pounds or more, while smaller mini-load ASRS typically handle product loads of less than 1,000 pounds in totes, trays,or cartons.
“In our experience, they make some of the best-engineered rack in the industry. Rack quality and consistency are important considerations in integrating automation and prolonging its usable life, which is why they are a preferred supplier,” he said.
Viewing warehouse system automation from a wider lens, Gauger considers the future of automation and the importance of the engineered racking that serves as its foundation.
“As customers require faster fulfillment and warehouses greater productivity, automation will account for an ever-larger portion of the material handling marketplace,” he concluded.