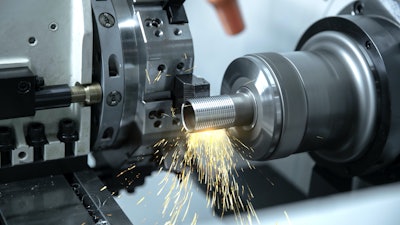
Have you ever experienced a sudden halt in your manufacturing operations due to spindle failure? In the world of manufacturing, spindle failure can lead to costly downtime, production inefficiencies and the need for expert spindle repair services.
In fact, the Society of Manufacturing Engineers (SME) reports, “When these systems deteriorate and fail due to contaminants, human error, improper maintenance, lubrication issues or poor spindle design, a quality rebuild is often required.”
Gaining insight into the common factors behind spindle failure is essential for maintaining efficiency and productivity within your facility. With that in mind, let's explore the common reasons behind spindle failure and how to prevent these issues from affecting your bottom line.
What Is Spindle Failure?
Spindle failure occurs when the spindle, the crucial turning component of computerized numerical control (CNC) machines and other manufacturing equipment, malfunctions or breaks down, compromising its ability to perform its intended function. Spindles are responsible for holding and rotating cutting tools and are essential for maintaining accuracy, precision and speed in machining processes.
A failing spindle can negatively impact manufacturing operations in various ways, including reduced production efficiency, poor parts finish or quality, excessive downtime and the need for costly repairs or replacements. By understanding the causes and signs of spindle failure, manufacturers can take proactive measures to maintain their equipment's reliability and keep their operations running smoothly.
9 Common Causes of Spindle Failure
1. Bearing Failure
Spindle bearings play a critical role in ensuring smooth operation and machining accuracy, and their failure can result from contamination, inadequate lubrication or being pushed beyond their operational limits. Regular inspections, proper lubrication and adherence to OEM recommendations can extend bearing life, preventing spindle failure and costly downtime.
2. Tooling Issues
It is essential to use appropriate, sharp cutting tools for optimal performance and to prevent spindle damage. Adequately maintained collets and tool holders also contribute to machining quality. Investing in high-quality tools and following maintenance guidelines can mitigate spindle failure risks and enhance productivity.
3. Thermal Growth and Expansion
Excessive heat and thermal expansion can compromise spindle performance, but implementing proper cooling methods and monitoring spindle temperature during operation can help avoid these issues. A well-managed thermal environment and the use of a non-contact heat sensor can ensure consistent machining quality and prevent potential spindle failure.
4. Misalignment
Spindle alignment is crucial for maintaining machining accuracy and preventing uneven wear and tear. Periodic checks and adjustments can keep your spindle aligned with other machine components, reducing the risk of failure and maintaining overall machine performance.
5. Excessive Vibration
Addressing sources of excessive vibration, such as imbalanced cutting tools or worn bearings, is essential for maintaining machining quality and preventing spindle damage. Incorporating vibration monitoring and balancing solutions can minimize the risk of vibration-induced spindle failure.
6. Warm-Up and Cool-Down Procedures
Following proper warm-up and cool-down procedures — as per the manufacturer — prevents issues such as component looseness, internal condensation and shortened spindle life. Following these guidelines ensures optimal spindle performance and longevity.
7. Air and Coolant Supply Contamination
Regular inspection and replacement of air filters, high-quality coolant filters and using air supply dryers in humid climates all contribute to spindle performance. Properly managing air and coolant supply minimizes contamination risks and prevents premature spindle failure.
8. Incorrect Machining Techniques
Employing recommended machining procedures and avoiding potentially damaging techniques — such as plunging into material — prevents excessive stress on spindle components. Adherence to proper techniques reduces the risk of spindle failure and maintains machining quality.
9. Tool Holder Problems
Regular inspection and maintenance of tool holders and drawbar assemblies is crucial for addressing issues such as tools sticking or slipping in the taper. Proper tool holder management helps prevent spindle failure and ensures consistent machining performance.
Tackle Spindle Failure Head-On for Long-Term Reliability
Proactively addressing the common causes of spindle failure is vital for maintaining efficiency and productivity in your manufacturing facility. By implementing regular maintenance procedures, selecting the right tools and investing in high-quality spindle components, you can help extend your spindle system's lifespan, ensuring the ongoing success of your business operations.
---
Jesse Riccardi is the General Manager of Northland Tool & Electronics. With over 15 years of spindle rebuilding experience, training and shop management, Jesse specializes in partnering with industry leaders to advance and improve the precision machine service market.