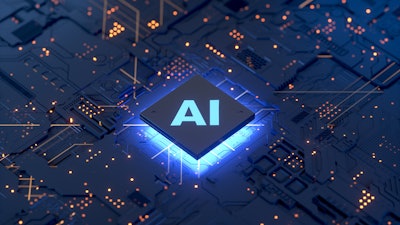
Artificial intelligence is one of the major technological advancements contributing to the growth of the manufacturing sector in the fourth industrial revolution. AI can be widely used in manufacturing to solve the hurdles like long machine downtime and quality issues. With the use of AI and machine learning, a manufacturer can improve operational efficiency, get insights into production data, forecast demands, and streamline operations.
A Capgemini research report found that European manufacturers are leading the implementation of AI solutions with 51 percent, followed by Japan at 30 percent, and the U.S. at 28 percent. The study also found that maintenance and quality control were the top AI use cases with 29 percent and 27 percent respectively. Manufacturers are implementing many more AI solutions and changing manufacturing forever.
These are the four elements of AI in Manufacturing that plants can implement to improve various parts of production:
1. Optimize Plant Operations
Industry 4.0 has started a digital transformation that aims to digitize, connect and optimize all the operations of a manufacturing plant. To achieve this transformation, manufacturers can use AI process mining, which is a swift way of finding bottlenecks in the system. The process uses AI and ML to analyze the available system’s data in order to visualize the operations and highlight the inefficiencies in the system.
Getting started with process optimization requires data from all the important assets in the system and the event logs of all equipment. Fortunately, modern digital factories use machinery with embedded sensors that can share data with the process mining tool easily. These tools can finish process mining in hours and provide valuable insights into the system. If a company has operations in multiple regions, the tools can compare the processes and identify points in the system requiring improvement.
To optimize the operations, you can use robots to automate repetitive tasks causing the bottlenecks or allocate extra tools and resources to solve the issue. AI also fulfils a huge role in process optimization solutions, such as automation, by creating smarter robots.
2. Predict Maintenance Requirements
One of the major reasons behind unplanned downtime is an inefficient maintenance method. Typical maintenance based on checks at regular intervals increases the probability of breakage and wear. On the other hand, AI-powered predictive maintenance uses real-time data and algorithms to predict maintenance requirements for the asset.
Predictive maintenance utilizes data from sensors spread across the system transferred by industrial IoT. This data is used by the computerized maintenance management system (CMMS) to visualize real-time conditions. The AI-based software takes into account the history of maintenance and real-time data to predict when an asset will require maintenance to avoid breakage and wear. According to a PwC report, predictive maintenance could improve uptime by nine percent, reduce costs by 12 percent, and extend the lifetime of aging assets by 20 percent.
Manufacturers with interconnected systems can easily implement predictive maintenance using the available data collection systems. In the beginning, the assets are inventoried, and the ones with the biggest impact on operations are chosen for predictive maintenance. With time, more assets can be brought under predictive maintenance for their optimization.
3. Upgrade Logistics Management
Logistics management is the lifeblood of any manufacturing plant. It plays a key role in making supply chains resilient and improving production efficiency. AI has multiple use cases in logistics management - including inventory management, material handling, transportation, and asset tracking.
As a starting point for your logistics management upgrades, you can get smart robots for material handling to reduce damage and improve production rates. Furthermore, AI-based inventory management systems can provide better inventory visibility for maximum asset utilization and minimum wastage. Finally, with transportation and asset tracking data, AI can provide optimal routes and delivery time estimates for a great customer experience.
4. Achieve Compliance with Quality Standards
An MIT study found that 59 percent of manufacturers are using AI for quality assurance. Some of the reasons behind this are cheaper equipment and tool costs. The common AI/ML quality control system uses computer vision to compare the products with acceptable product images fed by the manufacturer. Based on the feedback, the system learns from its mistakes and improves the results.
Implementing a computer vision quality control may require a high-definition camera and good lighting in the area. Customizing the ML platform based on the requirements also requires a skilled professional. Various AI-based systems are widely available in the market nowadays to make it easier and cheaper for you.
Manufacturers can also use AI to forecast demand and make top-level decisions, create digital twins, and improve product design. Based on the needs of the plant, AI can utilize data in different ways and provide solutions that make the plant more competitive. As the industry becomes more competitive, AI use cases will keep growing, and manufacturers who adopt the technology early will reap the benefits.
Eric Whitley has 30 years of experience in manufacturing, holding positions such as Total Productive Maintenance Champion for Autoliv ASP, an automotive safety system supplier that specializes in airbags and restraint systems. He is also an expert in lean and smart manufacturing practices and technologies. Over the years, Eric has worked with all sectors of industry including Food, Timber, Construction, Chemical and Automotive to name a few. Currently, he’s a part of the L2L team.