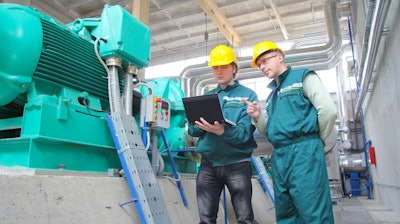
No one in the manufacturing industry wants to think about enduring extended downtime. But it can be the most impactful, yet avoidable cost businesses face. One 2016 study based on real survey data found 98 percent of organizations placed downtime costs at over $100,000 per hour. Some saw impacts as high as $5 million from a single hour of stoppage. In light of such costs, upgrading equipment may seem like the answer.
But it’s not as straightforward as it seems.
Legacy equipment, designed for decades of reliable service, forms the backbone of American manufacturing. To rip and replace entire systems is not only costly, it can be counterproductive due to the time involved in upgrading hardware and the downtime that can come with upgrades. And in-place equipment will resist any attempt at rapid transformation, making the transition more challenging.
Anyone who has ever been involved in a plant upgrade knows the time and effort put into minimizing downtime during the changeover. But upgrading equipment isn’t the only way to reduce downtime. Here are several other options that can help reduce the costs associated with unplanned downtime.
Determine Downtime’s Root Cause
Before you can solve a problem, you have to know what the problem is. First, identify the root cause of previous downtime.
- Is a specific machine causing the issue?
- Are there environmental issues like dust or excessive heat in play?
- Are problems occurring during a specific work shift, pointing toward operator error?
- Check any theories through step-by-step tests and process of elimination.
Once you've identified the source problem, take steps to correct it. Better still, document everything so the problem doesn’t repeat itself.
Plan Ahead
Maintenance is a part of manufacturing. If you put it off for too long you risk letting the machine choose when it happens.
Sticking to a preventive maintenance schedule will increase your equipment efficiency and lifespan. It will also decrease the probability of downtime caused by equipment failure. And yet almost two-thirds of respondents to a 2017 study used run-to-failure reactive maintenance methods at least part of the time.
While this maintenance method can be successful, it doesn’t allow you to pick the time when maintenance occurs. Part of any maintenance system should be securing all necessary documentation for your older legacy systems. But hard copy documents are easy to misplace or lose.
Best practices suggest maintaining PDF backups on inexpensive tablets. This makes documentation easy to store, transport, and access when needed while keeping original copies safe. If your systems are no longer supported by the OEM, maintenance should also include a risk assessment and, possibly, priority purchasing of replacement parts.
If space or other limitations keep you from maintaining on-hand stock, map out several possible sources with the parts available. This helps place parts in a stand-by position, limiting the chance of extended downtime.
Consider Tech Integration
Today, legacy systems can achieve modern IIoT connectivity through ready-made solutions. These third-party products and IoT-ready gateways enable data analysis through sensors and OPC servers. Installation of these devices can occur without a significant impact on productivity. After installation, retrofit technologies offer insight into a world of data, from lubrication issues to temperature fluctuations. Sensors can also help with spot vibration analysis and offer information on productivity.
Not only do such integrations offer a bigger, brighter window of information for maintenance, but they may help you spot previously overlooked issues or opportunities.
Empower Employee Communication
Top-down internal communication works well in most businesses. But is information moving as easily from the factory floor back up the corporate ladder? Frontline employees hold a wealth of knowledge. They hold true insight into the day-to-day operations of the company. Facilitating two-way communication means you can leverage that knowledge. This will help you fix big problems. But it will also help you identify and solve many of the small problems creating those larger issues.
Legacy industrial equipment is built to last. Its longevity is definitely a positive, giving businesses plenty of time to see a return on their investment. Adding in sensors and other tech extends this functionality, as does planning and preemptive maintenance. The result is lowered costs and less downtime, along with a better understanding of your plant operations.
Marla Keene is a Tech Writer for AX Control, Inc.