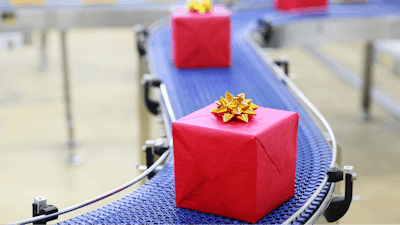
Downtime is typically one of the biggest costs in manufacturing. Many report the cost at $100,000 to $300,000 per hour, with a smaller percentage of businesses reporting the cost in excess of $1 million per hour. Below are six tips that can help you improve downtime prevention in your operation.
The first step in prevention of downtime is to understand your existing downtime causes. Without accurately tracking downtime and root cause, how will you know what to focus on? One tool that helps measure downtime is the Manufacturing Execution System (MES). Historically, the data depended on the diligence of the operator. Today, software solutions are now available to automate the collection of data from the machine to the MES.
Armed with accurate downtime information, you can plan an attack to address the top causes at the plant. Goal setting is a key strategy in this regard. As time moves forward, measure your progress and whether your strategy is working.
Training Pays Off
Some may be surprised to learn that human error is a large cause of downtime in manufacturing. In fact, human error more commonly causes downtime in manufacturing than in any other sector. Fortunately, there is a relatively low-cost partial solution to this problem. Proper training of employees will go a long way in reducing plant downtime.
As training techniques are becoming more visual, this task is becoming easier. Many companies are starting to migrate toward cloud-hosted, video-based training systems, which conveys the training in more easily understandable formats (think YouTube for manufacturing).
Preventive Maintenance Techniques
Preventive maintenance can help to reduce downtime by preventing the outages before they occur. It is a tried and true approach. For example, a 2017 study found that 60 percent of “best in class” operations were using some form of a preventive maintenance strategy. On average they saw an 11 percent reduction in year-on-year maintenance cost and a nine percent reduction in year-on-year unplanned downtime.
As the second step in the maintenance maturity model, preventive maintenance is a way to get started on the track to reliability.
Enact Autonomous Maintenance
Another maintenance strategy that can help to prevent downtime is implenting autonomous maintenance. This is the approach where basic maintenance tasks (like visual inspections, cleaning, and lubrication) are handled by operators as part of their standard work. Equipment runs efficiently, small issues are noticed more frequently (and way earlier), and maintenance staff time is freed for higher value tasks. It may require a culture shift, but autonomous maintenance can truly provide a step change in operational efficiency and downtime reduction.
Preventive maintenance techniques should help avoid unplanned downtime, but many of the tasks will require machines to be shut down. This can be a tough pill to swallow when you are trying to reduce all forms of downtime.
As your maintenance approach becomes more sophisticated, consider moving to predictive and prescriptive maintenance programs. This approach typically involves installing sensors to measure machine health characteristics. This data is then used to predict a machine failure before it occurs. This type of approach strikes the right balance between too many preventative tasks and waiting until machine breakdown. In this way downtime is truly minimized.
Many manufacturing operations have been slow to adopt this strategy. Fortunately, decreases in the price of predictive technology and analytics has lowered the barrier to entry and we are likely to see increased levels of adoption going forward.
Optimize Material Flow
Lastly, investigate flow of materials through the operation. You may be surprised to find downtime because of machines waiting on materials. Sometimes, communication with material delivery personnel is lacking. Other times, routes are not optimized for maximum efficiency. Perhaps storage locations do not make the most sense. Mapping the flow of materials through the site is often a valuable process that unlocks new insights. Inefficiencies may be found that can result in future prevention of downtime.
These six tips are certainly not an exhaustive list for preventing downtime in manufacturing. However, they are a great start and should hit on the most common reasons that downtime occurs. As you use these strategies, you should see downtime decrease in your operation, which in turn means increased efficiency and higher profits.
Bryan Christiansen is the founder and CEO of Limble CMMS.